사출금형 공정에서 게이트는 용융된 수지가 금형 캐비티로 유입되는 입구로, 제품의 품질과 생산성에 직접적인 영향을 미치는 핵심 요소입니다. 본 문서는 다양한 게이트 종류의 특징, 적용 분야, 설계 기준 및 최적화 전략을 종합적으로 분석합니다. 2024년 기준 450억 달러 규모의 글로벌 사출금형 시장에서 게이트 설계의 중요성이 점점 더 부각되고 있으며, 올바른 게이트 선택은 제품 품질 향상과 생산 효율성 증대에 결정적 역할을 합니다.
스프루 게이트 (Sprue Gate)
스프루 게이트는 사출금형에서 가장 기본적이고 단순한 형태의 게이트 시스템으로, 용융된 수지가 스프루 부시를 통해 직접 캐비티로 유입되는 구조를 가집니다. 주로 단일 캐비티 금형이나 대형 부품 생산에 활용되며, 설계가 간단하고 제작비용이 저렴한 장점이 있습니다.
스프루 게이트의 직경은 일반적으로 1.5mm에서 3.0mm 범위에서 설계되며, 제품의 크기와 복잡성, 사용되는 수지의 특성에 따라 조정됩니다. 수지 점도가 높을수록 더 큰 직경이 필요하며, 충전 시간과 압력 요구사항도 고려해야 합니다.
주요 장점:
- 충전 압력 손실이 최소화되어 금형 충전이 원활함
- 수지 흐름에 대한 저항이 적어 충전 속도 향상
- 설계 및 제작이 간단하여 금형 제작 비용 절감
- 게이트 크기가 커서 고점도 수지나 유리섬유 강화 수지에 적합
주요 단점:
- 게이트 자국(gate mark)이 크고 뚜렷하게 남아 후가공 필요
- 게이트 주변의 응력 집중으로 인한 제품 강도 저하 가능성
- 수축 및 싱크 마크(sink mark) 발생 위험 증가
- 다중 캐비티 금형에 적용하기 어려움

스프루 게이트는 주로 단순한 형상의 두꺼운 부품, 대형 용기, 기술적 요구사항이 낮은 제품 등에 적합합니다. 특히 생산량이 적고 게이트 자국이 외관에 영향을 미치지 않는 제품이나 후가공이 예정된 제품에 효과적입니다.
최근에는 핫 런너(hot runner) 시스템과 결합하여 스프루 게이트의 단점을 보완하는 방식도 널리 사용되고 있습니다. 이를 통해 제품 냉각 시간 단축, 재료 낭비 감소, 사이클 타임 개선 등의 효과를 얻을 수 있습니다.
사이드 게이트 (Side Gate)

사이드 게이트는 수지가 제품의 측면으로 유입되는 게이트 유형으로, 다중 캐비티 금형에서 가장 널리 사용되는 방식입니다. 런너 시스템을 통해 여러 캐비티에 균일하게 수지를 분배할 수 있어 대량 생산에 적합합니다.
사이드 게이트의 일반적인 크기는 0.8mm에서 1.5mm 범위이며, 제품 두께의 약 50~80%를 기준으로 설계됩니다. 너무 작은 게이트는 충전 문제를 야기할 수 있고, 너무 큰 게이트는 싱크 마크나 게이트 제거의 어려움을 초래할 수 있어 적절한 크기 선정이 중요합니다.
구조적 특징:
- 파팅 라인(parting line)에 위치하여 금형 설계와 제작이 용이함
- 런너 시스템을 통해 다중 캐비티에 균일한 수지 분배 가능
- 게이트 위치와 크기 조정이 비교적 자유로움
- 핫 런너 시스템과의 호환성이 우수함
사이드 게이트는 다양한 제품 형상에 적용할 수 있는 높은 적응성을 가지고 있습니다. 특히 박스형 제품, 원통형 제품의 측면, 평면 제품 등에 효과적으로 적용할 수 있으며, 제품의 외관에 게이트 자국이 허용되는 경우 가장 경제적인 선택입니다.
냉각 시간과 사이클 타임 측면에서도 사이드 게이트는 효율적인 성능을 제공합니다. 게이트 크기를 최적화하여 충분한 충전을 보장하면서도 빠른 고화(solidification)가 가능하므로 생산성 향상에 기여합니다. 특히 전자 부품 하우징, 가전제품 부품, 자동차 내장재 등 중소형 정밀 부품 생산에 널리 활용됩니다.
핀 포인트 게이트 (Pin Point Gate)
핀 포인트 게이트는 극소형 게이트 시스템으로, 정밀한 제품 생산과 자동화된 게이트 절단을 가능하게 하는 고급 게이트 기술입니다. 일반적으로 3핀 포인트 시스템으로 구성되며, 이는 고정핀(fixed pin), 이젝터 핀(ejector pin), 그리고 게이트 핀(gate pin)으로 이루어져 복잡한 작동 메커니즘을 형성합니다.
핀 포인트 게이트의 가장 큰 특징은 그 크기에 있습니다. 일반적으로 직경 0.5mm 이하로 설계되며, 특수 정밀 부품의 경우 0.2mm까지 작아질 수 있습니다. 이렇게 미세한 게이트 설계는 특수한 가공 기술과 정밀한 설계 계산을 필요로 하며, 게이트 위치 선정에도 세심한 주의가 요구됩니다.
초정밀 설계
미세한 게이트 크기(0.2~0.5mm)로 인해 고정밀 가공 기술이 요구되며, 게이트 위치에 따른 수지 흐름 패턴과 충전 균형을 정확히 예측해야 합니다.
자동화된 게이트 절단
제품 배출 과정에서 이젝터 핀의 작동으로 게이트가 자동으로 절단되어 별도의 후가공 공정이 불필요하며, 생산 효율성이 크게 향상됩니다.
전자 부품 응용
미세한 게이트 자국과 정밀한 수지 주입 제어로 인해 스마트폰 부품, 커넥터, 반도체 패키징 등 고정밀 전자 부품 생산에 이상적입니다.
품질 향상 효과
게이트 자국이 최소화되고 수지 주입이 정밀하게 제어되어 웰드 라인 감소, 변형 최소화, 치수 안정성 향상 등 전반적인 제품 품질이 개선됩니다.
핀 포인트 게이트는 특히 핫 런너 시스템과 결합하여 사용될 때 가장 효과적인 성능을 발휘합니다. 이를 통해 수지 낭비를 최소화하고, 사이클 타임을 단축하며, 균일한 충전 패턴을 유지할 수 있습니다. 의료 기기, 광학 부품, 정밀 커넥터 등 높은 품질 요구사항을 가진 소형 정밀 부품 생산에 필수적인 게이트 시스템으로 자리 잡고 있습니다.
그러나 핀 포인트 게이트는 설계 및 제작 비용이 높고, 유지보수가 복잡하며, 유리섬유 강화 수지나 고점도 수지에는 적합하지 않다는 한계도 가지고 있습니다. 따라서 제품 특성과 생산 요구사항을 종합적으로 고려한 신중한 선택이 필요합니다.
팬 게이트 (Fan Gate)
팬 게이트는 넓은 면적을 통해 수지를 분산 주입하는 독특한 설계의 게이트 시스템으로, 특히 넓은 평면 형상의 제품 생산에 효과적입니다. 일반적인 게이트와 달리 넓은 너비(5~20mm)와 얇은 두께(0.5~1.0mm)를 가진 부채꼴 또는 직사각형 형태로 설계되며, 이러한 구조적 특성으로 인해 수지가 캐비티 내부로 넓게 분산되어 유입됩니다.
팬 게이트의 주요 설계 기준:
- 게이트 두께: 제품 두께의 약 40~60% (일반적으로 0.5~1.0mm)
- 게이트 너비: 제품 특성에 따라 5mm에서 20mm까지 다양하게 설계
- 게이트 테이퍼(taper): 수지 흐름 균형을 위해 1~3도의 경사 적용
- 위치: 제품의 넓은 평면 부위에 배치하여 균일한 충전 유도
팬 게이트는 특히 넓은 평면 형상을 가진 제품, 웰드 라인이 외관 품질에 중요한 영향을 미치는 제품, 변형에 민감한 얇은 평판 제품 등에 적합합니다. 넓은 면적을 통한 분산 주입 방식은 수지 흐름 패턴을 고르게 분포시켜 웰드 라인(weld line) 발생을 최소화하고 제품 내부의 응력 분포를 균일하게 만들어 변형을 줄이는 효과가 있습니다.
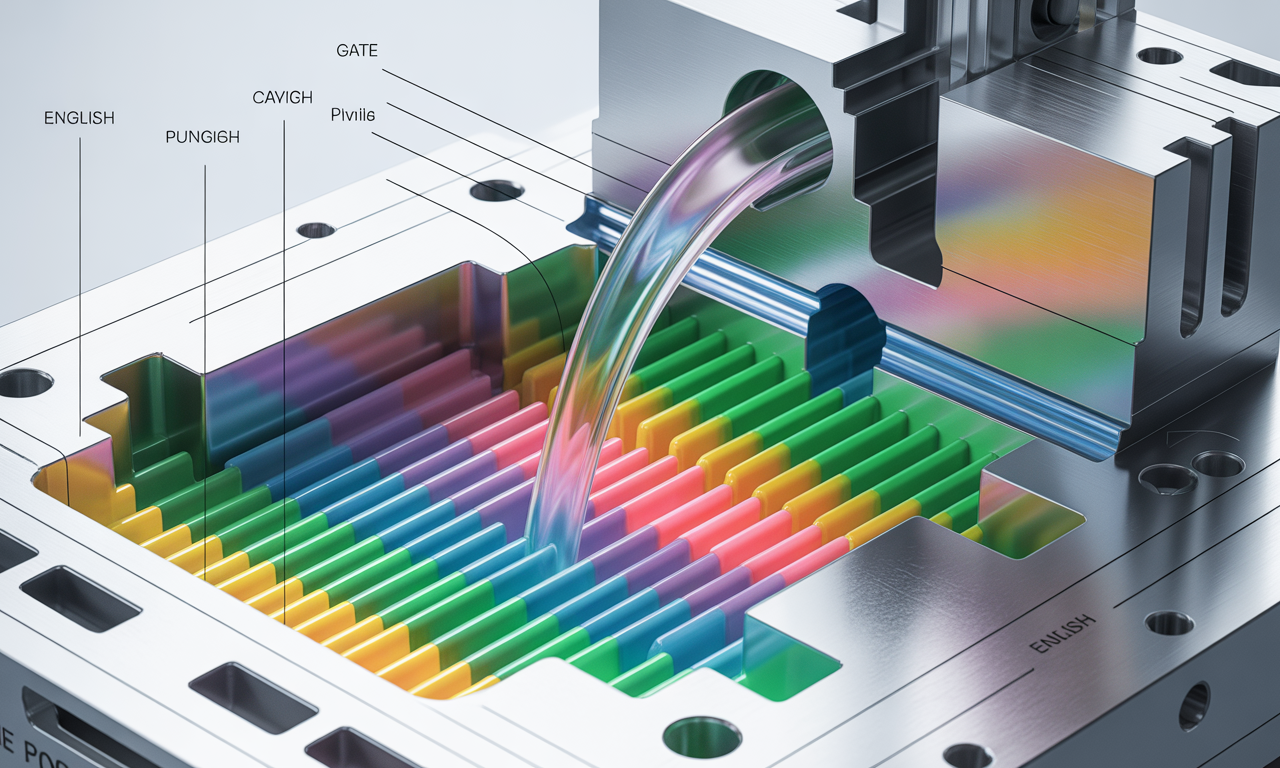
팬 게이트의 실제 적용 사례:
- 자동차 내장재: 대시보드, 도어 패널 등 넓은 평면 부품에 적용하여 표면 품질 향상
- 가전제품 케이스: TV 백커버, 모니터 하우징 등 얇고 넓은 평판 제품에 활용
- 태블릿/노트북 케이스: 균일한 충전과 변형 최소화가 필요한 얇은 전자기기 외장
- 플라스틱 패널: 간판, 디스플레이 패널 등 넓은 평면 제품의 변형 방지
그러나 팬 게이트는 게이트 절단 및 후가공이 복잡하고, 금형 설계와 제작이 다른 게이트 유형에 비해 난이도가 높다는 단점이 있습니다. 또한 게이트 부위의 두께 변화로 인한 냉각 시간 차이가 제품 변형에 영향을 줄 수 있어, 정밀한 냉각 시스템 설계가 함께 고려되어야 합니다.
다이어프램 게이트 (Diaphragm Gate)
다이어프램 게이트는 원형 또는 원통형 제품을 위해 특별히 설계된 게이트 시스템으로, 용융된 수지가 원주 방향으로 360° 균일하게 흐르도록 하는 독특한 구조를 가지고 있습니다. 이 게이트는 스프루에서 원형의 얇은 디스크 형태로 확장되어 제품의 중심축에 위치하며, 수지가 모든 방향으로 균등하게 분산되도록 합니다.
원형 구조
360° 원주 방향으로 수지가 균일하게 흐르는 디스크 형태의 구조
균형 충전
모든 방향에서 동시에 충전되어 수지 흐름 균형 최적화
변형 최소화
내부 응력이 균일하게 분산되어 제품 변형 감소
다이어프램 게이트의 두께는 일반적으로 0.8mm에서 1.5mm 범위에서 설계되며, 제품 두께의 약 50~70%를 기준으로 합니다. 게이트 직경은 제품의 크기와 형상에 따라 달라지지만, 주로 제품 직경의 1/3~1/2 정도로 설계하여 충분한 수지 흐름을 보장하면서도 게이트 절단이 용이하도록 합니다.
다이어프램 게이트는 수지 충전 균형이 특히 중요한 제품에 이상적입니다. 수지가 모든 방향에서 동시에 유입되기 때문에 웰드 라인이 거의 발생하지 않고, 내부 응력이 균일하게 분산되어 제품 변형이 최소화됩니다. 이러한 특성은 치수 안정성과 균일한 수축이 중요한 정밀 부품 생산에 큰 장점을 제공합니다.
다이어프램 게이트 적용 분야:
- 의료기기: 주사기 실린더, 주입 캡, 의료용 밸브 등
- 정밀 부품: 베어링 하우징, 기어 케이스, 부싱 등
- 전자 부품: 원형 커넥터, 센서 하우징, 전자기기 캡 등
- 화장품 용기: 원통형 용기, 크림 자르, 립스틱 케이스 등
그러나 다이어프램 게이트는 게이트 절단 과정이 복잡하고, 게이트 자국이 제품 중심에 남기 때문에 외관이 중요한 제품에는 적합하지 않을 수 있습니다. 또한 중공 부품이나 내부에 코어가 있는 제품에는 적용이 제한적이며, 금형 설계와 제작이 다른 게이트 유형에 비해 복잡하다는 단점이 있습니다.
서브마린 게이트 (Submarine Gate)

서브마린 게이트는 파팅 라인(parting line) 아래에 위치하는 터널식 게이트로, 자동 게이트 절단 메커니즘을 제공하는 고급 게이트 시스템입니다. 런너에서 약 15~25도의 각도로 경사진 터널을 통해 캐비티로 연결되며, 이 독특한 구조가 제품 사출 후 자동 게이트 분리를 가능하게 합니다.
서브마린 게이트의 직경은 일반적으로 0.7mm에서 1.2mm 범위에서 설계되며, 제품 두께와 크기, 수지 특성에 따라 조정됩니다. 터널 길이는 보통 직경의 2~3배로 설계하여 충분한 강도를 확보하면서도 제품 배출 시 원활한 게이트 절단이 이루어지도록 합니다.
서브마린 게이트의 주요 특징:
- 자동 게이트 절단: 제품 배출 과정에서 게이트가 자연스럽게 분리되어 별도의 절단 공정 불필요
- 게이트 자국 위치 제어: 제품의 비가시적 부분에 게이트 자국을 위치시킬 수 있음
- 다중 캐비티 적용: 균형 잡힌 충전을 위해 다중 캐비티 금형에 효과적으로 적용 가능
- 생산 자동화: 게이트 절단 공정이 불필요하여 생산 자동화 수준 향상
서브마린 게이트는 다중 캐비티 금형에서 균형 충전을 위한 이상적인 게이트 유형 중 하나입니다. 런너 시스템과 게이트 크기를 정밀하게 설계하여 모든 캐비티에 균일한 압력과 온도로 수지가 분배되도록 할 수 있습니다. 이는 대량 생산 환경에서 일관된 제품 품질을 보장하는 데 중요한 요소입니다.
특히 서브마린 게이트의 자동 게이트 절단 특성은 생산 자동화와 효율성 측면에서 큰 이점을 제공합니다. 제품이 금형에서 배출될 때 이젝터 핀의 작동으로 게이트가 자연스럽게 절단되므로, 별도의 게이트 절단 공정이 필요하지 않습니다. 이는 생산 사이클 타임 단축, 인력 비용 절감, 품질 향상 등 다양한 이점으로 이어집니다.
복잡한 형상 적합성
복잡한 형상의 소형 및 중형 부품, 특히 외관이 중요한 제품에 적합합니다.
산업별 응용
전자 제품 하우징, 소형 가전 부품, 자동차 내장재, 화장품 용기 등 다양한 산업 분야에 활용됩니다.
금형 유지보수
게이트 부분의 마모가 발생하기 쉬워 정기적인 금형 유지보수와 관리가 필요합니다.
자동화 생산
자동 게이트 절단으로 인해 로봇 자동화 시스템과의 통합이 용이하여 완전 자동화 생산에 적합합니다.
게이트 선택 가이드라인 및 최적화 전략
제품 분석
제품 형상, 크기, 재질, 품질 요구사항 등을 종합적으로 분석
게이트 유형 선정
제품 특성에 맞는 최적의 게이트 유형 선택
크기 및 위치 최적화
CAE 시뮬레이션을 통한 게이트 크기와 위치 최적화
지속적 개선
시제품 평가 및 양산 피드백을 통한 게이트 설계 개선
효과적인 게이트 선택은 제품 형상, 수지 특성, 생산 요구사항을 종합적으로 고려해야 합니다. 제품 형상별로 일반적으로 권장되는 게이트 유형이 존재하지만, 각 제품의 고유한 특성과 요구사항에 따라 최종 결정은 달라질 수 있습니다.
제품 유형 | 권장 게이트 유형 | 주요 고려사항 |
얇고 넓은 평면 제품 | 팬 게이트, 필름 게이트 | 균일한 충전, 변형 최소화 |
원형/원통형 제품 | 다이어프램 게이트, 링 게이트 | 360° 균일 충전, 웰드라인 방지 |
소형 정밀 부품 | 핀 포인트 게이트, 서브마린 게이트 | 정밀 충전 제어, 자동 게이트 절단 |
중대형 두꺼운 부품 | 스프루 게이트, 직접 게이트 | 충전 압력 최소화, 수축 제어 |
다중 캐비티 소형 부품 | 사이드 게이트, 서브마린 게이트 | 균형 충전, 생산 효율성 |
수지 특성에 따른 게이트 설계는 특히 중요합니다. 고점도 수지나 유리섬유 강화 수지는 더 큰 게이트 직경이 필요하며, 결정성 수지는 후압(packing pressure) 전달이 중요하므로 게이트 냉각 타이밍이 신중하게 고려되어야 합니다. 또한 게이트 위치는 수지 흐름 패턴, 웰드 라인 위치, 공기 트랩(air trap) 발생 가능성 등에 직접적인 영향을 미치므로 CAE 시뮬레이션을 통한 검증이 필수적입니다.
최신 게이트 기술 트렌드는 핫 런너 시스템과의 통합, 밸브 게이트 활용, 캐스케이드 충전(cascade filling) 기법 등으로 발전하고 있습니다. 특히 스마트 금형 기술과 결합한 능동적 게이트 제어 시스템은 사출 과정에서 실시간으로 게이트 개폐 타이밍과 흐름 속도를 조절하여 보다 정밀한 충전 제어를 가능하게 합니다. 이러한 첨단 기술은 자동차 경량화 부품, 의료기기, 고정밀 전자부품 등 품질 요구사항이 까다로운 분야에서 점차 확산되고 있으며, 금형 산업의 미래 발전 방향을 제시하고 있습니다.
'자동차 전문 채널 > 자동차 부품업계 관련 업무 지식' 카테고리의 다른 글
사출금형 구조설명: 히든코어와 히든파팅 (2) | 2025.05.30 |
---|---|
현대기아자동차 내장부품 내열싸이클 시험조건 분석 (1) | 2025.05.30 |
3D 데이터뷰어 프로그램 MODView 소개 (3) | 2025.05.29 |
사출금형 경사코어의 이해와 활용 (1) | 2025.05.29 |
금형에서 사용하는 용접의 종류와 특징 (0) | 2025.05.29 |
사출금형의 슬라이드코어 기술 가이드 (0) | 2025.05.29 |