자동차용 플라스틱 소재별 특성
현대 자동차 산업에서는 경량화와 연비 향상을 위해 플라스틱 소재의 활용이 지속적으로 증가하고 있습니다. 글로벌 자동차 산업에서 플라스틱 사용량은 연간 9%의 증가 추세를 보이며, 현대 자동차의 평균 플라스틱 사용량은 차량 중량의 20-25%에 달합니다. 2024년 기준 자동차 부품 중 플라스틱 소재 시장 규모는 약 840억 달러로 추정되며, 이는 연비 향상 및 이산화탄소 배출량 감소를 위한 경량화의 핵심 소재로서 플라스틱의 중요성을 보여줍니다.
폴리프로필렌(PP) 특성 및 응용
폴리프로필렌(PP)은 자동차 내 사용량 1위를 차지하는 플라스틱 소재로, 전체 플라스틱 사용량의 약 32%를 차지합니다. 이 소재는 내화학성과 내열성이 우수하여 150°C까지의 온도에서도 안정적인 성능을 유지합니다. 또한 우수한 가공성을 가지고 있으며, 0.9-0.91의 낮은 비중으로 경량화에 크게 기여합니다.
폴리프로필렌은 자동차의 범퍼, 계기판, 도어 트림, 팬 쉬라우드 등 다양한 부품에 주로 사용됩니다. 특히 범퍼와 같은 외장 부품에 적용될 때는 충격 강도를 개선하기 위해 탈크(활석)를 20-40% 첨가하는 것이 일반적입니다. 이러한 첨가물은 소재의 강성과 치수 안정성을 향상시키며, 열팽창 계수를 낮추는 효과가 있습니다.
환경적 측면에서도 폴리프로필렌은 재활용 등급 5등급으로 분류되며, 재활용률이 70% 이상으로 높은 편입니다. 자동차 해체 시 PP 부품은 비교적 쉽게 분리하여 재활용할 수 있으며, 재생 PP는 내장재나 비노출 부품에 재사용되어 순환경제에 기여합니다. 이러한 특성으로 인해 폴리프로필렌은 자동차 산업에서 가장 널리 사용되는 열가소성 수지로 자리매김하고 있습니다.
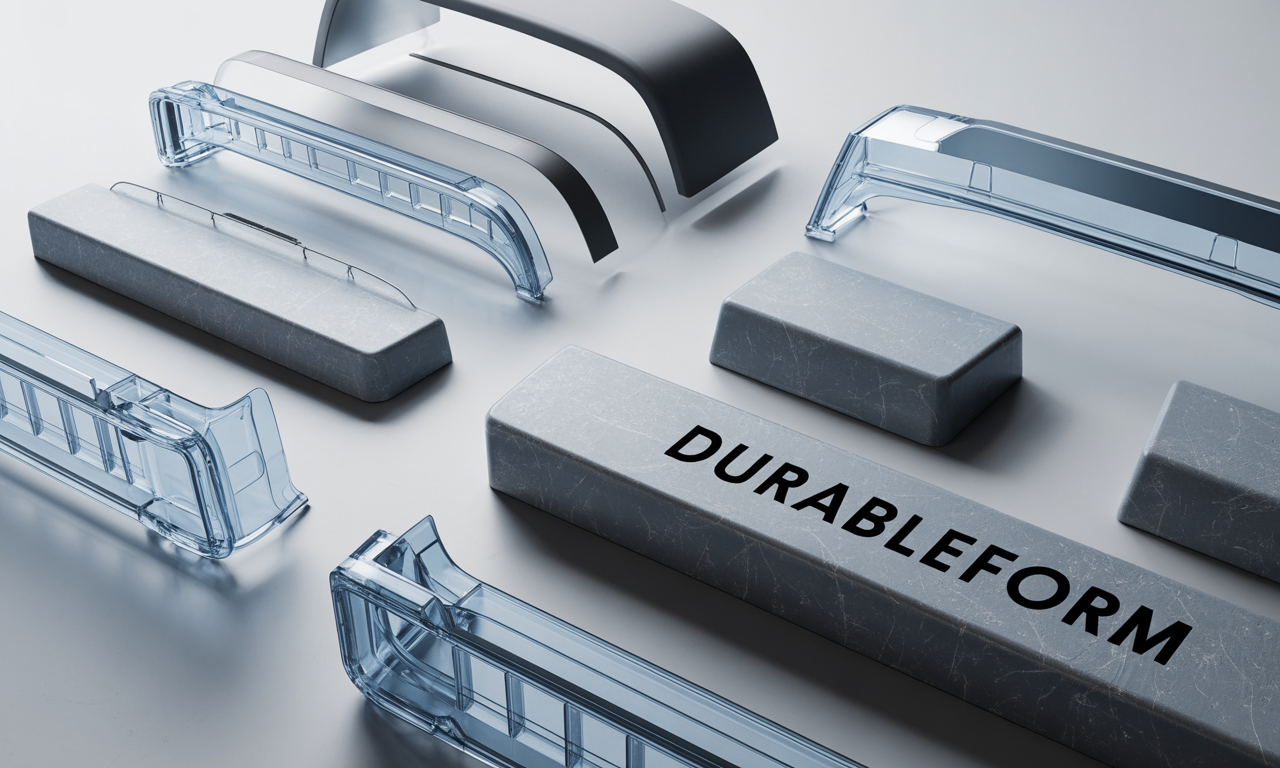
폴리프로필렌의 주요 특성
- 밀도: 0.9-0.91 g/cm³ (가장 가벼운 플라스틱 중 하나)
- 내열성: 약 150°C까지 견딜 수 있음
- 내화학성: 산, 알칼리, 용매에 대한 저항성 우수
- 가공성: 쉬운 사출 성형 및 압출 가공 가능
- 경제성: 비교적 저렴한 가격으로 대량 생산에 적합
- 재활용성: 재활용 등급 5등급, 재활용률 70% 이상
폴리우레탄(PU) 특성 및 응용
폴리우레탄(PU)은 자동차 내장재에서 중요한 역할을 하는 소재로, 특히 승객의 편안함과 안전에 직접적인 영향을 미치는 부품에 널리 사용됩니다. 시트 쿠션, 헤드레스트, 대시보드 패딩과 같은 부품에 주로 적용되며, 이 소재의 가장 큰 특징은 다양한 경도 조절이 가능하다는 점입니다. 쇼어 A 20부터 95까지의 넓은 범위에서 경도를 조절할 수 있어, 동일한 기본 화학 구조를 가지면서도 매우 부드러운 시트 쿠션부터 단단한 구조용 부품까지 다양한 용도로 활용됩니다.
폴리우레탄의 또 다른 중요한 특성은 뛰어난 진동 흡수 및 소음 저감 능력입니다. 이러한 특성은 자동차의 NVH(소음, 진동, 거칠기) 성능을 개선하여 승차감을 향상시키는 데 크게 기여합니다. 특히 PU 폼은 미세한 셀 구조로 인해 소리와 진동을 효과적으로 차단하며, 이는 고급 자동차에서 더욱 중요시되는 요소입니다.
폴리우레탄은 -40°C에서 120°C까지의 넓은 온도 범위에서 안정적인 성능을 유지하며, 내구성과 내마모성이 우수하여 자동차의 수명 주기 전반에 걸쳐 성능을 유지합니다. 그러나 폴리우레탄은 화재 시 유독가스를 발생시킬 수 있는 위험이 있어, 안전 규정을 충족시키기 위해 난연제를 첨가하는 것이 필수적입니다. 최근에는 환경 친화적인 바이오 기반 폴리올을 사용한 폴리우레탄 개발이 활발히 진행되고 있으며, 이는 석유 기반 원료 의존도를 줄이고 탄소 발자국을 감소시키는 데 도움을 줍니다.
온도 안정성
-40°C에서 120°C까지의 넓은 온도 범위에서 물성 유지, 극한 기후 조건에서도 안정적 성능 보장
NVH 성능
뛰어난 진동 흡수 및 소음 저감 특성으로 차량 내부의 소음과 진동을 효과적으로 차단
유연한 경도 조절
쇼어 A 20-95의 경도 범위로 동일 소재로 다양한 용도의 부품 제작 가능
내구성
우수한 내마모성과 장기간 하중에도 형태를 유지하는 성능으로 차량 수명 동안 기능 유지
아크릴로니트릴 부타디엔 스티렌(ABS) 특성 및 응용
아크릴로니트릴 부타디엔 스티렌(ABS)은 자동차 산업에서 매우 중요한 엔지니어링 플라스틱으로, 뛰어난 충격 강도와 우수한 표면 품질을 제공합니다. 이 소재의 가장 큰 장점은 내구성과 미관을 동시에 만족시킬 수 있다는 점입니다. ABS는 비중이 약 1.05로 금속보다 가볍지만, 40-50MPa의 높은 인장 강도를 가지고 있어 구조적 안정성이 요구되는 부품에도 사용할 수 있습니다.
자동차 부품 중에서는 그릴, 도어 핸들, 휠 커버, 콘솔 부품 등 주로 시각적으로 노출되는 부분에 ABS가 활용됩니다. 특히 ABS의 뛰어난 도금 적합성은 크롬 도금이 필요한 부품에 이상적인 소재로 만들어 줍니다. 로크웰 R105-115의 높은 표면 경도를 가지고 있어 일상적인 스크래치에 강하며, 고광택 표면 처리가 가능하여 고급스러운 외관을 연출할 수 있습니다.
그러나 ABS는 85-100°C 정도의 내열 온도를 가지고 있어 엔진룸이나 고온 환경에 노출되는 부품에는 적합하지 않습니다. 또한 UV 노출 시 변색 및 물성 저하 문제가 발생할 수 있어, 외장 부품에 사용될 경우 UV 안정제를 첨가하거나 보호 코팅을 적용하는 것이 필수적입니다. 이러한 제한에도 불구하고 ABS는 우수한 가공성과 표면 품질, 그리고 경제적인 가격으로 인해 자동차 내외장 부품에 널리 사용되고 있습니다. 최근에는 PC나 PA와 같은 다른 엔지니어링 플라스틱과 블렌딩하여 내열성이나 내화학성을 개선한 그레이드도 개발되고 있습니다.

ABS의 주요 기술 사양
물성 | 수치 |
비중 | 약 1.05 |
인장 강도 | 40-50MPa |
내열 온도 | 85-100°C |
표면 경도 | 로크웰 R105-115 |
충격 강도 | 200-400 J/m |
열변형 온도 | 약 95°C (1.8MPa) |
폴리아미드(PA, 나일론) 특성 및 응용
기계적 강도
인장 강도 70-85MPa, 고강성 응용분야 적합
내열성
150-180°C 고온 환경에서도 물성 유지
엔진 부품 적합성
내화학성과 내마모성으로 금속 대체 가능
흡습성
24시간 내 2-3% 흡습, 치수 안정성 관리 필요
폴리아미드(PA), 일반적으로 나일론이라 불리는 이 소재는 자동차 산업에서 가장 중요한 엔지니어링 플라스틱 중 하나입니다. 기계적 강도와 내열성이 뛰어나 금속을 대체할 수 있는 몇 안 되는 플라스틱 소재입니다. 폴리아미드는 150-180°C의 고온에서도 안정적인 성능을 유지하기 때문에 엔진 부품, 연료 시스템, 에어 인테이크 매니폴드와 같은 고온 환경에 노출되는 부품에 광범위하게 활용됩니다.
폴리아미드의 물성은 유리섬유 강화를 통해 더욱 향상됩니다. 일반적으로 15-50%의 유리섬유를 첨가하여 강성과 내구성을 크게 개선합니다. 유리섬유 30% 강화 PA66의 경우, 인장 강도가 약 150-180MPa까지 증가하며, 이는 일부 알루미늄 합금에 근접하는 수준입니다. 이러한 특성으로 인해 베어링, 기어, 라디에이터 탱크, 오일 팬과 같은 부품에서 금속을 대체하여 차량 중량을 크게 감소시킬 수 있습니다.
그러나 폴리아미드는 흡습성이 있어 물을 흡수하는 특성이 있으며, 이로 인한 치수 안정성 문제가 존재합니다. 일반적으로 24시간 내에 2-3%의 수분을 흡수할 수 있으며, 이는 소재의 물성 변화를 야기할 수 있습니다. 따라서 정밀한 치수가 요구되는 부품에 사용될 경우 적절한 건조 및 환경 관리가 필요합니다. 또한 폴리아미드의 종류에 따라 특성이 다양하게 나타나는데, PA6는 가공성이 우수하고 경제적인 반면, PA66은 더 높은 내열성과 기계적 강도를 제공합니다. PA11과 PA12는 흡습성이 낮아 치수 안정성이 중요한 부품에 선호됩니다. 최근에는 바이오 기반 PA가 개발되어 환경 친화적인 대안으로 주목받고 있습니다.
폴리카보네이트(PC) 및 PC/ABS 블렌드 특성
폴리카보네이트(PC)는 우수한 투명성, 뛰어난 내충격성, 그리고 높은 내열성을 갖춘 고성능 엔지니어링 플라스틱입니다. 약 130°C까지의 온도에서 안정적인 성능을 유지하며, 이러한 특성으로 인해 헤드램프 렌즈, 선루프, 대시보드와 같은 자동차 부품에 널리 사용됩니다. 특히 PC의 광학적 선명도는 헤드램프 렌즈에 이상적이며, 내충격성은 안전 관련 부품에 중요한 요소입니다.
순수한 PC는 가공이 어려울 수 있기 때문에, 자동차 산업에서는 PC/ABS 블렌드가 널리 사용됩니다. 이 블렌드는 PC의 우수한 기계적 특성과 내열성을 유지하면서도 ABS의 가공성을 활용하여 제조 공정을 용이하게 합니다. 또한 PC/ABS 블렌드는 저온에서의 충격성이 개선되어 겨울철 같은 극한 환경에서도 안정적인 성능을 보장합니다. 일반적으로 PC/ABS 블렌드는 70/30 또는 60/40의 비율로 제조되며, 용도에 따라 다양한 그레이드가 존재합니다.
그러나 PC와 PC/ABS 블렌드는 자외선에 취약하여 장기간 노출 시 황변 현상과 물성 저하가 발생할 수 있습니다. 이러한 문제를 해결하기 위해 자외선 차단 코팅이나 UV 안정제를 첨가하는 것이 필수적입니다. 또한 이 소재들은 비교적 고가이기 때문에 주로 고급차나 특별한 기능적 요구사항이 있는 부품에 한정적으로 사용됩니다. 최근에는 내스크래치성이 향상된 하드 코팅 기술과 함께 PC의 활용 범위가 확장되고 있으며, 경량화와 디자인 자유도 향상을 위해 글라스 패널 대체재로서의 가능성도 탐색되고 있습니다.

PC 및 PC/ABS 블렌드의 주요 특성
- 투명성: 빛 투과율 89% 이상 (순수 PC 기준)
- 내충격성: 노치드 아이조드 충격 강도 600-850 J/m
- 내열성: 열변형 온도 130-140°C (PC 기준)
- 굴곡 강도: 90-100 MPa
- 인장 강도: 55-65 MPa
- 비중: 1.2-1.25
"폴리카보네이트의 우수한 기계적 특성과 광학적 투명성은 자동차 조명 시스템의 혁신을 가능하게 했습니다. LED 헤드램프와 같은 현대적 조명 시스템은 PC의 열 관리 능력과 광학적 특성이 없었다면 구현하기 어려웠을 것입니다." - 한국자동차공학회 재료분과 연구보고서, 2023
열가소성 엘라스토머(TPE) 및 PVC 특성
열가소성 엘라스토머(TPE)는 고무와 같은 탄성을 가지면서도 열가소성 플라스틱처럼 가공할 수 있는 혁신적인 소재입니다. 이러한 특성으로 인해 자동차 산업에서는 도어 씰, 웨더스트립, 와이퍼 블레이드와 같은 유연성과 내구성이 동시에 요구되는 부품에 널리 활용됩니다. TPE는 용융 상태에서 성형이 가능하여 복잡한 형상을 쉽게 만들 수 있으며, 사출 성형, 압출, 블로우 몰딩 등 다양한 공정으로 제조할 수 있습니다.
TPE는 여러 종류로 나뉘며, 각각 고유한 특성을 가지고 있습니다. SEBS(스티렌-에틸렌-부틸렌-스티렌)는 뛰어난 내후성을 제공하여 외부 환경에 노출되는 부품에 적합합니다. TPV(열가소성 벌커나이즈드 엘라스토머)는 우수한 내유성을 가지고 있어 엔진 주변 부품에 사용됩니다. TPO(열가소성 올레핀)는 비교적 저렴한 가격으로 대량 생산에 적합합니다. 이러한 다양성은 자동차 설계자들에게 각 부품의 요구사항에 맞는 최적의 소재를 선택할 수 있는 유연성을 제공합니다.
유연성과 탄성
TPE는 -40°C에서도 유연성을 유지하며, 영구 압축변형이 적어 씰링 성능이 장기간 유지됩니다. 쇼어 하드니스 A 30-90 범위에서 조절 가능하여 다양한 용도로 활용할 수 있습니다.
재활용성
열가소성 특성으로 성형 폐기물을 재활용할 수 있어 환경 친화적입니다. 열경화성 고무와 달리 재가공이 가능하여 제조 과정에서의 폐기물을 최소화할 수 있습니다.
난연성
PVC는 본질적으로 난연성을 가지고 있어 와이어 하네스 절연체로 널리 사용됩니다. 자동차 안전 규정 충족을 위한 중요한 특성입니다.
내화학성
PVC는 다양한 화학 물질, 오일, 그리스에 대한 저항성이 우수하여 자동차 환경에서 안정적인 성능을 제공합니다. 연료 라인 근처 부품에도 적합합니다.
한편, PVC(폴리염화비닐)는 내화학성과 난연성이 우수한 소재로, 주로 와이어 하네스의 절연체로 사용됩니다. PVC는 가성비가 매우 우수하여 경제적인 대량 생산이 가능하며, 다양한 가소제와 첨가제를 통해 유연성과 내구성을 조절할 수 있습니다. 그러나 최근 환경 규제가 강화되면서 할로겐 화합물을 함유한 PVC의 사용이 제한되고 있으며, 이로 인해 TPE나 폴리올레핀 기반의 대체 소재 개발이 활발히 진행되고 있습니다. 특히 자동차 내장재에서는 VOC(휘발성 유기 화합물) 배출을 줄이기 위해 친환경적인 대체 소재로의 전환이 가속화되고 있습니다.
친환경 바이오 플라스틱 및 미래 동향
바이오 기반 소재 개발
바이오 기반 PA, PLA, PHA 등 환경 친화적 소재가 개발되고 있으며, 2025년까지 자동차 플라스틱의 15%가 바이오 소재로 대체될 전망입니다.
카본 파이버 복합 소재
강도/중량 비율이 10:1로 향상된 카본 파이버 복합 소재는 경량화와 안전성을 동시에 만족시킬 수 있는 해결책으로 부상하고 있습니다.
재활용 의무화
재활용 플라스틱 의무 사용 비율이 증가하고 있으며, EU는 2030년까지 35%를 목표로 하고 있습니다.
전기차용 소재 개발
배터리 전기차에 적합한 난연성, 내열성이 강화된 소재 개발이 활발히 진행 중입니다.
자동차 산업에서 친환경 바이오 플라스틱의 개발과 활용은 지속 가능한 미래를 위한 중요한 과제로 부상하고 있습니다. 바이오 기반 PA(폴리아미드), PLA(폴리유산), PHA(폴리하이드록시알카노에이트) 등 다양한 환경 친화적 소재가 개발되고 있으며, 이러한 소재들은 석유 기반 플라스틱의 대안으로 주목받고 있습니다. 연구에 따르면 2025년까지 자동차에 사용되는 플라스틱 중 약 15%가 바이오 소재로 대체될 것으로 전망됩니다.
고성능 복합 소재의 발전도 주목할 만한 동향입니다. 특히 카본 파이버 강화 플라스틱(CFRP)은 강도/중량 비율이 기존 소재 대비 10:1 이상 향상되어, 차량 경량화와 안전성 향상을 동시에 만족시킬 수 있는 해결책으로 각광받고 있습니다. 초기에는 고급 스포츠카나 전기차에 제한적으로 사용되었으나, 제조 기술의 발전과 비용 감소로 점차 대중화되고 있습니다.
환경 규제 강화도 자동차 플라스틱 소재 개발의 중요한 동력입니다. EU를 중심으로 재활용 플라스틱의 의무 사용 비율이 점차 증가하고 있으며, 2030년까지 차량에 사용되는 플라스틱의 35%를 재활용 소재로 대체하는 것을 목표로 하고 있습니다. 이러한 규제는 자동차 제조업체들로 하여금 순환경제를 고려한 소재 선택과 설계를 촉진하고 있습니다.
전기 자동차의 증가에 따라 배터리 관련 부품에 적합한 특수 소재 개발도 활발히 진행되고 있습니다. 특히 배터리 화재 위험을 줄이기 위한 고난연성 소재와 배터리 열관리를 위한 고내열성 소재의 중요성이 증가하고 있습니다. 또한 전자기 간섭(EMI) 차폐 기능을 갖춘 도전성 플라스틱도 전기차의 전자 시스템 보호를 위해 개발되고 있습니다. 이러한 다양한 트렌드는 자동차 플라스틱 소재가 단순한 경량화 소재를 넘어 기능성과 환경성을 동시에 만족시키는 방향으로 발전하고 있음을 보여줍니다.