본 문서는 무인운반차(AGV)의 기본 개념부터 다양한 유형, 실제 산업 적용 사례, 그리고 미래 발전 방향까지 포괄적으로 다룹니다. AGV 시스템의 기술적 원리와 내비게이션 방식, 하드웨어 및 소프트웨어 구성, 다양한 산업에서의 활용 사례, 도입 시 고려사항 등 AGV에 관한 모든 측면을 상세히 설명합니다.
AGV의 정의 및 기본 개념
무인운반차(Automated Guided Vehicle, AGV)는 프로그래밍된 경로를 따라 자율적으로 이동하며 물품을 운반하는 자동화된 이동 로봇입니다. 이 시스템은 인간의 직접적인 개입 없이 자율적으로 작동하며, 정해진 경로를 따라 물품을 한 위치에서 다른 위치로 이동시키는 기능을 수행합니다.
AGV는 기본적으로 차체, 구동 시스템, 제어 시스템, 내비게이션 시스템, 안전 시스템으로 구성됩니다. 차체는 운반할 화물을 싣는 구조물이며, 구동 시스템은 AGV를 움직이게 하는 모터와 바퀴로 구성됩니다. 제어 시스템은 AGV의 움직임과 작업을 관리하는 두뇌 역할을 합니다. 내비게이션 시스템은 AGV가 경로를 인식하고 따르도록 하는 기술로, 마그네틱 테이프, 레이저, 비전 등 다양한 방식이 사용됩니다. 안전 시스템은 충돌 방지와 비상 정지 기능을 제공하여 사람과 장비의 안전을 보장합니다.
AGV는 주로 물류센터, 공장, 창고와 같은 산업 환경에서 사용되어 반복적이고 시간 소모적인 물품 운반 작업을 자동화함으로써 작업 효율을 높이고 인력 비용을 절감합니다. 최근에는 기술 발전에 따라 병원, 호텔, 공항 등 다양한 서비스 산업으로도 그 활용 범위가 확대되고 있습니다.
AGV 시스템의 핵심 가치는 물류 프로세스의 자동화, 표준화, 효율화에 있으며, 이를 통해 생산성 향상, 인건비 절감, 작업 안전성 증대, 그리고 물류 흐름의 예측 가능성을 높이는 데 기여합니다.
AGV의 역사와 발전 과정
무인운반차(AGV)의 역사는 1950년대 초반으로 거슬러 올라갑니다. 최초의 상업적 AGV는 1953년 미국의 Barrett Electronics Corporation이 개발한 'Guide-O-Matic'이라는 견인형 카트였습니다. 이 초기 모델은 바닥에 설치된 전선을 감지하여 따라가는 단순한 방식으로 작동했습니다.
1960년대에 들어서면서 AGV 기술은 제조업에서 점차 채택되기 시작했으며, 특히 자동차 산업에서 조립 라인의 부품 운반에 활용되었습니다. 1970년대에는 마이크로프로세서가 도입되면서 AGV의 제어 시스템이 크게 개선되었고, 더욱 복잡한 작업을 수행할 수 있게 되었습니다.
1980년대와 1990년대에는 레이저 유도 방식이 등장하면서 AGV의 내비게이션 정확도가 크게 향상되었습니다. 반사기를 사용한 이 방식은 기존의 전선 추적 방식보다 유연성이 높고 설치가 간편하여 널리 채택되었습니다. 또한 이 시기에는 무선 통신 기술의 발전으로 중앙 제어 시스템과 AGV 간의 실시간 통신이 가능해졌습니다.
2000년대 이후에는 컴퓨터 비전, SLAM(Simultaneous Localization and Mapping) 기술, 인공지능의 발전으로 AGV의 자율성이 크게 향상되었습니다. 특히 자연 특징 인식 방식의 내비게이션이 도입되면서 바닥에 물리적인 가이드가 없이도 작동 가능한 자율주행 로봇(AMR: Autonomous Mobile Robot)으로 진화했습니다.
현재의 AGV는 5G, 클라우드 컴퓨팅, 빅데이터 분석, 인공지능 기술과 결합되어 더욱 스마트하고 효율적인 물류 시스템의 핵심 구성요소로 자리 잡고 있습니다. 초기의 단순한 물품 운반 기능에서 벗어나 재고 관리, 주문 처리, 생산 계획과 연동되는 통합 물류 솔루션으로 그 역할이 확장되고 있습니다.
AGV와 AMR(자율이동로봇)의 차이
무인운반차(AGV)
AGV는 미리 정의된 경로를 따라 움직이도록 프로그래밍된 장비입니다. 전통적인 AGV는 물리적 가이드(마그네틱 테이프, 와이어, QR코드 등)를 따라 이동하며, 이러한 미리 정의된 경로에서 벗어날 수 없습니다. 경로를 변경하기 위해서는 물리적인 인프라를 수정해야 하는 경우가 많아 유연성이 제한적입니다.
AGV는 주로 정해진 지점 간 반복적인 이동이 필요한 환경, 예를 들어 생산 라인에서 작업장 간 자재 이동이나 창고 내 특정 경로를 따라 물품을 운반하는 작업에 적합합니다. 장애물을 만났을 때는 단순히 정지하는 경우가 많으며, 환경 변화에 대한 적응력이 상대적으로 낮습니다.
자율이동로봇(AMR)
AMR은 보다 발전된 형태의 로봇으로, 환경을 인식하고 자체적으로 경로를 계획할 수 있는 능력을 갖추고 있습니다. AMR은 SLAM(Simultaneous Localization and Mapping) 기술을 이용해 자신의 위치를 실시간으로 파악하고 환경 지도를 만들면서 이동합니다. 따라서 물리적 가이드 없이도 자유롭게 이동할 수 있으며, 장애물을 만났을 때도 우회 경로를 찾아 목적지에 도달할 수 있습니다.
AMR은 유동적인 환경 또는 빈번한 레이아웃 변경이 발생하는 공간에서 효과적이며, 다양한 작업을 수행할 수 있는 유연성을 제공합니다. 또한 여러 대의 AMR이 협업하여 복잡한 물류 작업을 수행하는 시스템으로 발전하고 있습니다.
최근에는 두 기술 간의 경계가 점차 모호해지고 있습니다. 최신 AGV 시스템은 AMR의 일부 특성을 채택하여 제한된 범위 내에서 경로 재계획이 가능하도록 발전하고 있으며, 반대로 AMR도 효율성을 위해 주요 이동 경로를 최적화하는 특성을 갖추고 있습니다. 결국 두 시스템의 선택은 적용 환경의 특성, 필요한 유연성 수준, 비용 효율성 등을 종합적으로 고려하여 결정해야 합니다.
AGV의 핵심 역할과 필요성
작업 효율성 향상
AGV는 24시간 연속 작동이 가능하며, 일관된 속도와 정확도로 물품을 운반합니다. 인간 작업자보다 빠르고 정확한 이동으로 물류 프로세스의 효율성을 크게 향상시킵니다. 또한 동시에 여러 대의 AGV를 운영하여 대규모 물류 작업을 효과적으로 처리할 수 있습니다.
비용 절감
초기 투자 비용은 높을 수 있으나, 장기적으로는 인건비 절감, 에너지 효율성, 유지보수 비용 감소 등으로 상당한 비용 절감 효과를 가져옵니다. 특히 24시간 운영 환경이나 인력 채용이 어려운 지역에서 더욱 큰 경제적 이점을 제공합니다.
안전성 강화
AGV는 다양한 안전 센서와 시스템을 갖추고 있어 사고 위험을 최소화합니다. 무거운 물품의 운반 과정에서 발생할 수 있는 작업자 부상을 예방하고, 위험한 환경(고온, 유독물질 등)에서도 안전하게 작업할 수 있습니다. 이는 산업 안전 규정 준수와 작업 환경 개선에 기여합니다.
데이터 기반 의사결정
최신 AGV 시스템은 운행 데이터, 화물 정보, 위치 데이터 등을 실시간으로 수집하고 분석할 수 있습니다. 이를 통해 물류 흐름 최적화, 병목 현상 파악, 자원 할당 개선 등 데이터 기반의 의사결정이 가능해집니다.
현대 산업 환경에서 AGV의 필요성은 날로 증가하고 있습니다. 글로벌 경쟁 심화로 인한 생산성 향상 요구, 인력 부족 및 인건비 상승, 유연한 생산 시스템의 필요성, 그리고 안전 규제 강화 등이 AGV 도입을 가속화하는 주요 요인입니다. 특히 코로나19 이후 비대면 자동화에 대한 관심이 높아지면서 AGV 시장은 더욱 빠르게 성장하고 있습니다.
또한 AGV는 스마트팩토리와 물류 4.0 구현의 핵심 요소로서, 디지털 전환(Digital Transformation)을 추진하는 기업들에게 중요한 투자 대상이 되고 있습니다. 생산 시스템, 창고 관리 시스템(WMS), 제조 실행 시스템(MES)과의 통합을 통해 전체 공급망을 최적화하는 역할을 수행하고 있습니다.
AGV의 시장 성장 동향
무인운반차(AGV) 시장은 전 세계적으로 급속한 성장 추세를 보이고 있습니다. 시장 조사 기관 MarketsandMarkets에 따르면, 글로벌 AGV 시장 규모는 2021년 약 37억 달러에서 2026년까지 약 85억 달러로 연평균 성장률(CAGR) 18.0%의 성장이 예상됩니다. 특히 아시아태평양 지역은 제조업 기반이 강하고 인건비 상승 압박이 커 가장 빠른 성장을 보이고 있습니다.
산업별로는 자동차, 전자제품, 식음료, 물류, 제약 산업에서 AGV 도입이 활발하며, 특히 전자상거래의 폭발적 성장으로 물류 센터에서의 활용이 크게 증가하고 있습니다. 또한 병원, 호텔, 공항 등 서비스 산업에서도 AGV 도입이 확대되는 추세입니다.
AGV 시장 성장을 촉진하는 주요 요인으로는 첫째, 인건비 상승과 인력 부족 문제가 전 세계적으로 심화되면서 자동화에 대한 수요가 증가하고 있습니다. 둘째, 전자상거래의 급성장으로 대규모 물류센터의 효율적 운영이 필수적이 되었습니다. 셋째, 스마트팩토리 구축 추세에 따라 생산 및 물류 자동화의 핵심 요소로 AGV가 주목받고 있습니다. 넷째, 코로나19 이후 비대면 자동화 수요가 크게 증가했습니다. 마지막으로, AGV 기술의 발전과 가격 경쟁력 향상으로 중소기업에서도 도입이 가능해지고 있습니다.
시장 트렌드로는 AMR(자율이동로봇)과의 기술적 융합, 인공지능과 빅데이터 분석 기능의 강화, 협동 로봇과의 통합, 클라우드 기반 원격 모니터링 시스템 도입, 그리고 '로봇 어스 어 서비스(RaaS)' 모델의 확산이 주목받고 있습니다. 이러한 새로운 기술과 비즈니스 모델의 등장은 AGV 시장의 성장을 더욱 가속화할 것으로 전망됩니다.
주요 글로벌 AGV 제조사 소개
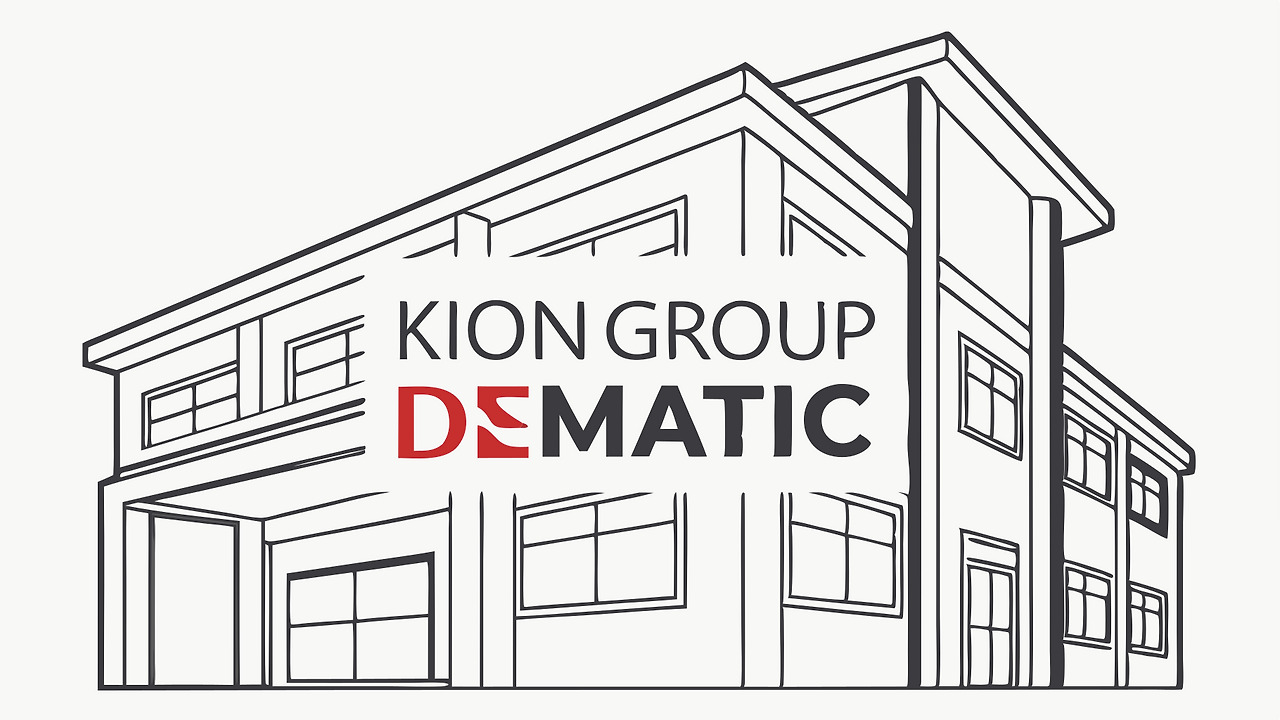
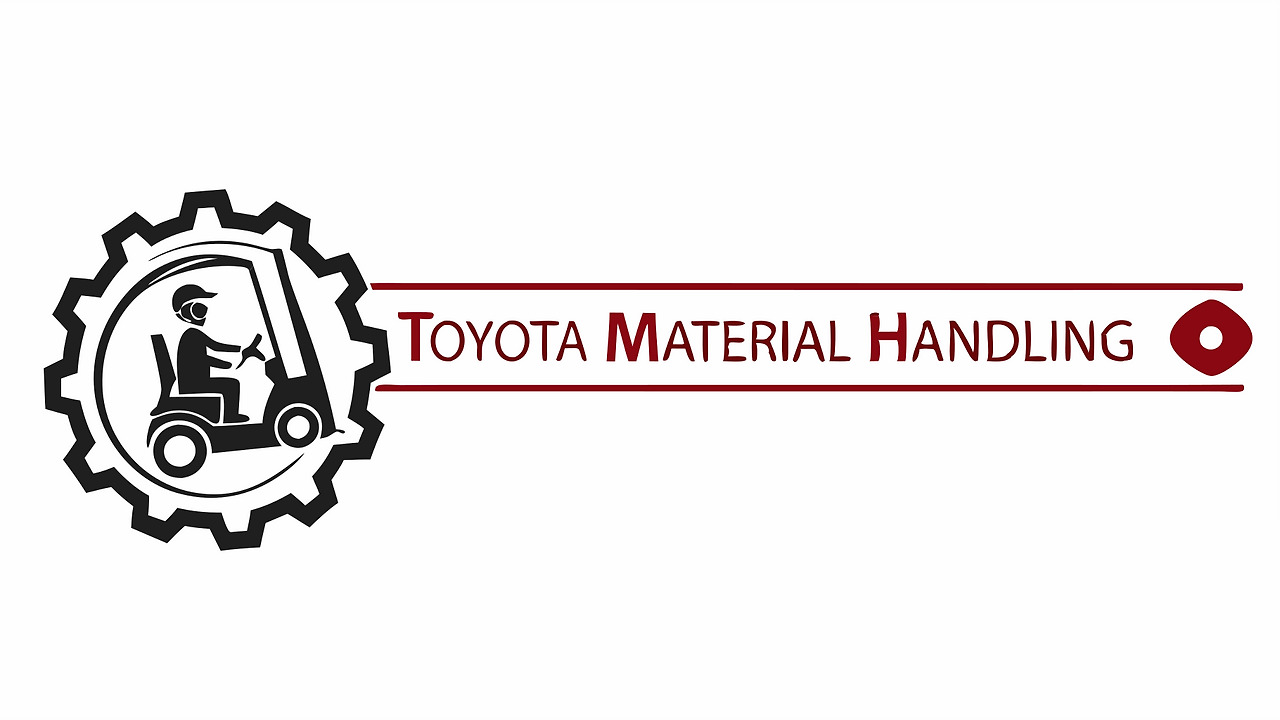
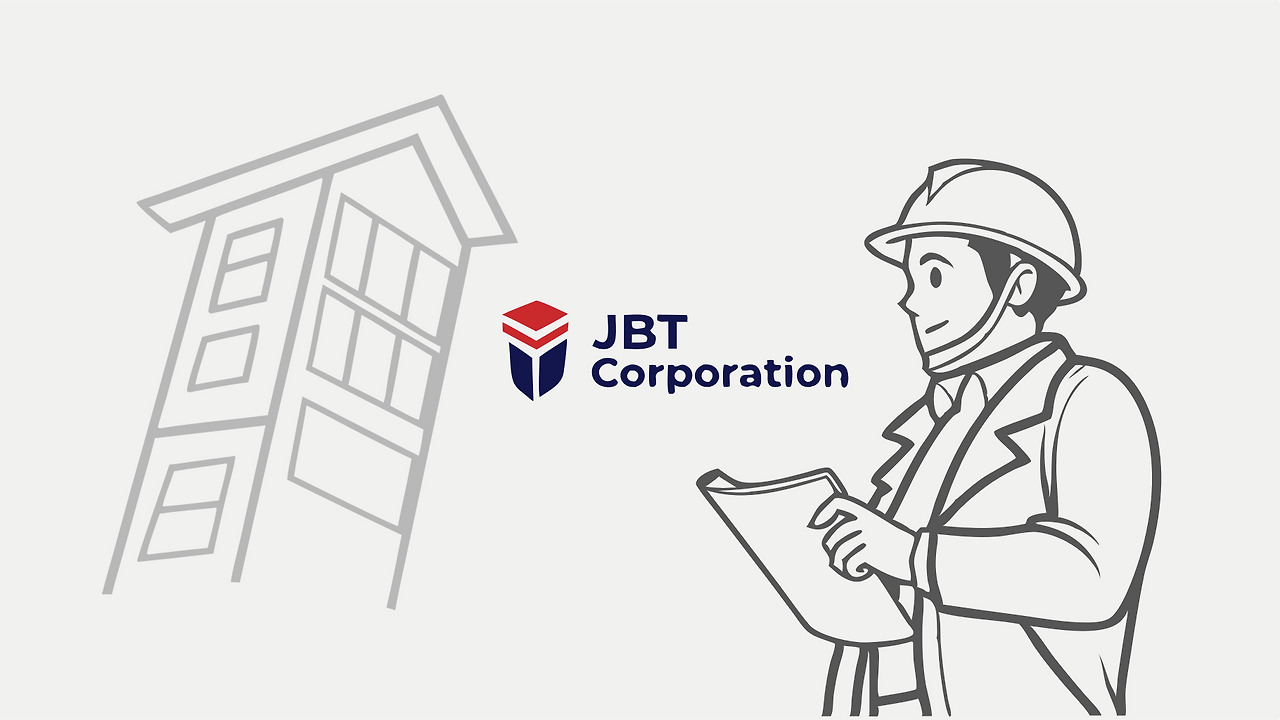
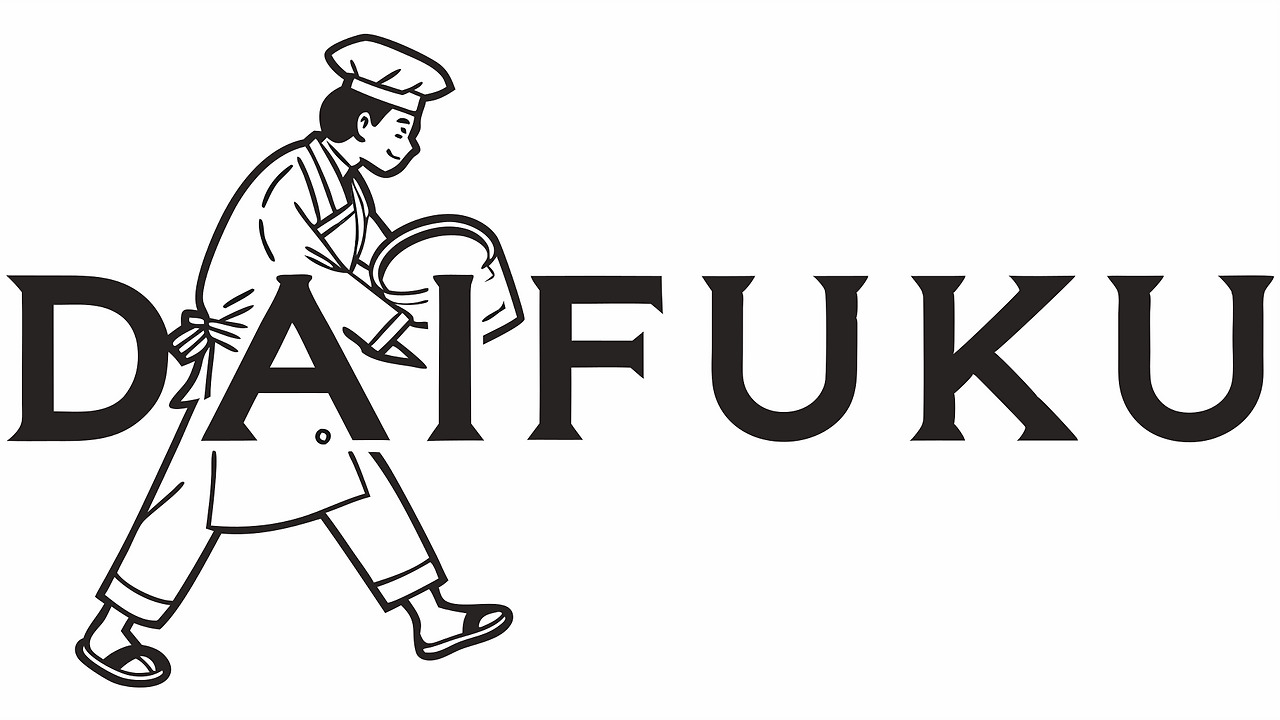
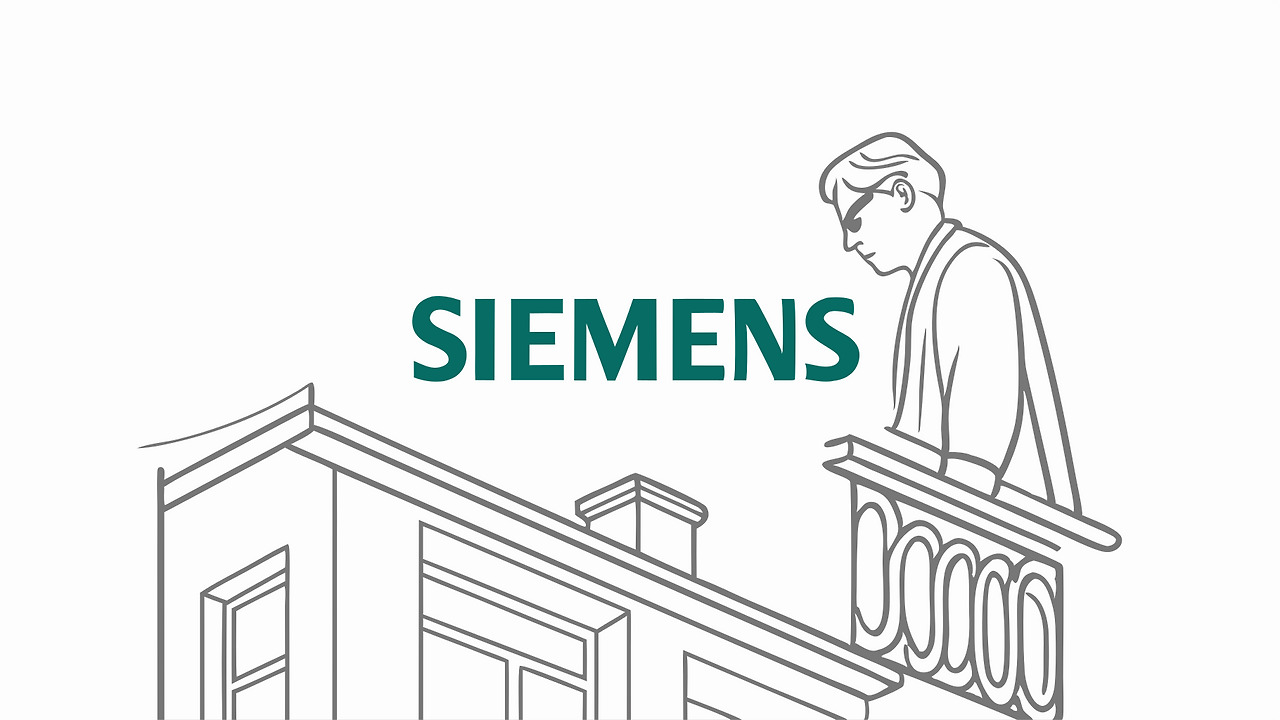
글로벌 AGV 시장에는 다양한 제조사들이 경쟁하고 있으며, 각각 고유한 기술과 전문 분야를 보유하고 있습니다. 주요 제조사들과 그들의 특징은 다음과 같습니다.
유럽 기반 제조사
독일의 KION 그룹(Dematic)은 물류 자동화 솔루션의 선두주자로, 특히 웨어하우스 자동화 시스템과 통합된 AGV 솔루션을 제공합니다. 스웨덴의 Kollmorgen은 AGV 내비게이션 시스템과 제어 소프트웨어 분야의 선도 기업으로, 다양한 OEM 제조사에 기술을 공급합니다. 독일의 Siemens는 산업 자동화 분야에서 폭넓은 포트폴리오를 갖추고 있으며, 통합 제조 솔루션의 일부로 AGV 시스템을 제공합니다.
아시아 기반 제조사
일본의 Toyota Material Handling은 글로벌 최대 지게차 제조사로, AGV 시장에서도 강세를 보이고 있습니다. 특히 견인형 및 지게차형 AGV 분야에 강점이 있습니다. 일본의 Daifuku는 물류 자동화 시스템 분야의 글로벌 리더로, 특히 대규모 생산 시설과 물류 센터용 AGV 시스템에 특화되어 있습니다. 한국의 현대건설기계와 두산산업차량도 지게차 기반 AGV 시장에서 점유율을 높여가고 있습니다.
북미 기반 제조사
미국의 JBT Corporation은 식품 가공 및 공항 서비스 분야에 특화된 AGV를 제공하며, 특수 환경에 적합한 맞춤형 솔루션으로 유명합니다. Seegrid는 비전 유도 기술을 기반으로 한 AGV 시스템을 개발하여 유연한 자동화 솔루션을 제공합니다. 캐나다의 Savant Automation은 중소규모 창고와 제조 시설을 위한 비용 효율적인 AGV 솔루션으로 알려져 있습니다.
이들 글로벌 제조사들은 각자의 기술적 강점과 시장 포지셔닝을 기반으로 경쟁하고 있으며, 최근에는 인수합병을 통한 시장 확대와 기술 역량 강화가 활발히 이루어지고 있습니다. 예를 들어, KION 그룹은 Dematic을 인수하여 물류 자동화 역량을 크게 강화했으며, Toyota는 여러 지역의 AGV 전문 기업들을 인수하며 글로벌 네트워크를 확장하고 있습니다.
또한 기존의 물류 장비 제조사뿐 아니라 소프트웨어 기업과 로봇 전문 기업들도 AGV 시장에 진입하면서 경쟁 구도가 더욱 복잡해지고 있습니다. 특히 클라우드 기반 제어 시스템, 인공지능 기술 등을 접목한 혁신적인 솔루션을 제공하는 스타트업들의 등장도 주목할 만한 트렌드입니다.
국내 AGV 시장의 특징과 규모
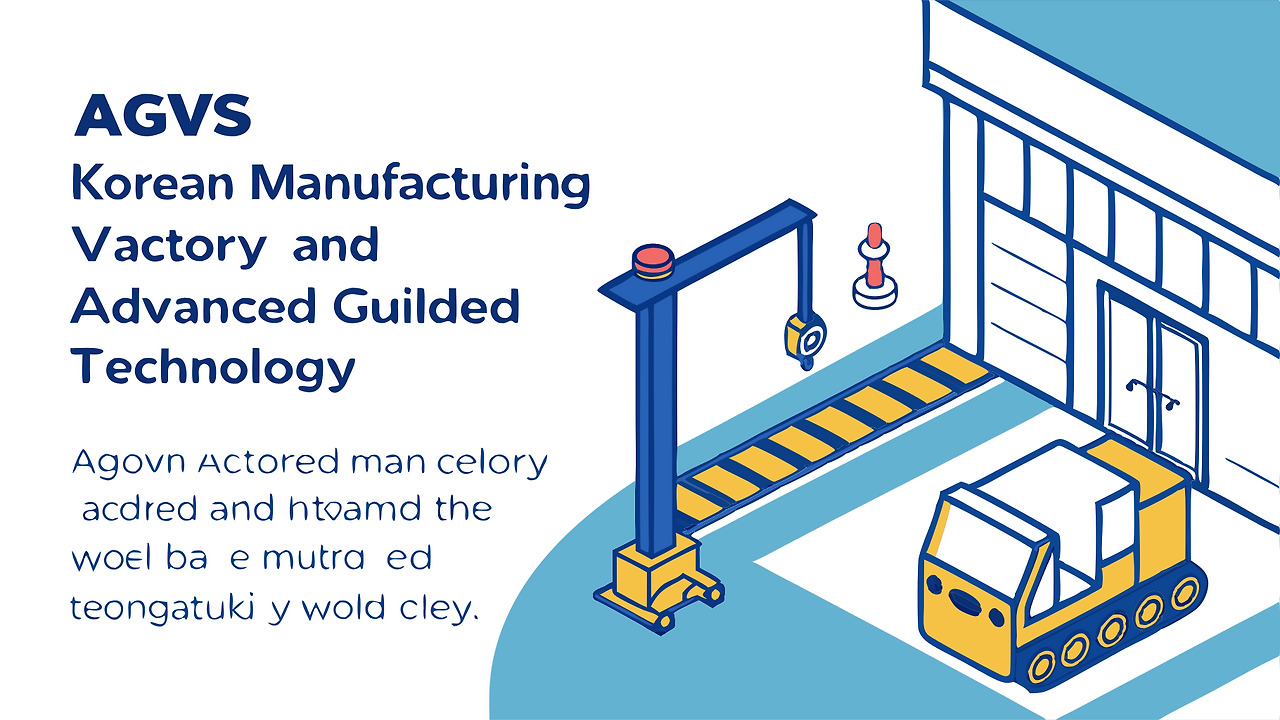
한국의 AGV 시장은 제조업 강국이라는 특성을 기반으로 꾸준히 성장하고 있으며, 특히 자동차, 전자, 반도체, 철강, 조선 등 주요 산업 분야에서의 수요가 높은 편입니다. 한국 AGV 시장은 2022년 기준 약 4,000억원 규모로 추정되며, 연평균 15% 이상의 성장률을 보이고 있습니다.
국내 AGV 시장의 주요 특징
- 국내 대기업 중심의 도입: 삼성, 현대, LG, 포스코 등 대기업을 중심으로 AGV 도입이 활발하게 이루어지고 있으며, 점차 중견·중소기업으로 확대되는 추세
- 정부 지원 정책: 스마트팩토리 보급·확산 사업, 제조업 혁신 3.0 등 정부의 제조업 디지털 전환 지원 정책이 AGV 도입 확대에 기여
- 수입 의존도 높음: 고성능 AGV 시스템은 여전히 해외 제품 의존도가 높은 편이나, 국내 업체들의 기술력도 점차 향상 중
- 서비스형 로봇(RaaS) 모델 확산: 초기 도입 비용을 낮추기 위한 월 구독형 서비스 모델이 확산 중
국내 주요 AGV 기업 현황
회사명 | 주요 제품 및 특징 | 주요 고객군 |
고영로보틱스 | 비전 기반 AMR, 물류 로봇 시스템 | 반도체, 디스플레이 산업 |
유진로봇 | 서비스 로봇, 물류 AMR | 병원, 서비스업, 물류센터 |
로보스타 | 산업용 로봇, AGV 시스템 | 자동차, 전자 산업 |
현대건설기계 | 지게차형 AGV | 제조업, 물류센터 |
두산산업차량 | 견인형 AGV, 팔레트 운반형 AGV | 제조업, 물류창고 |
한국 AGV 시장의 주요 동향으로는 첫째, 스마트팩토리 구축 사업의 일환으로 AGV 도입이 증가하고 있습니다. 둘째, 인력 고령화와 구인난으로 인한 자동화 수요가 증가하고 있습니다. 셋째, 국내 기업들의 기술 개발 투자가 확대되어 자체 기술력이 향상되고 있습니다. 특히 SLAM 기술, 인공지능 기반 제어 시스템 등에서 국산화가 진행 중입니다. 넷째, 5G 기반 원격 모니터링 및 제어 기술의 도입이 확산되고 있습니다. 마지막으로, 산학연 협력을 통한 R&D가 활발히 진행되고 있습니다.
국내 AGV 시장의 과제로는 첫째, 중소기업을 위한 저가형 AGV 솔루션 개발이 필요합니다. 둘째, 핵심 부품 및 소프트웨어의 국산화가 더욱 확대되어야 합니다. 셋째, 전문 인력 양성을 위한 교육 프로그램 확충이 시급합니다. 넷째, 표준화 및 안전 인증 체계 구축이 필요합니다. 마지막으로, 글로벌 경쟁력 강화를 위한 정부 지원 확대가 요구됩니다.
AGV 시스템의 기술적 원리
AGV(무인운반차) 시스템은 크게 하드웨어 구성요소와 소프트웨어 시스템으로 나눌 수 있으며, 이들이 유기적으로 결합하여 자율적인 물품 운반을 가능하게 합니다. AGV의 기술적 원리를 구성하는 핵심 요소들을 살펴보겠습니다.
내비게이션 시스템
AGV의 내비게이션 시스템은 미리 정의된 경로를 따라 이동하거나 환경을 인식하여 자율적으로 경로를 생성하는 역할을 합니다. 주요 내비게이션 방식으로는 마그네틱 테이프/스폿 방식, 와이어 가이드 방식, 레이저 반사기 방식, 비전 기반 방식, SLAM(Simultaneous Localization and Mapping) 기술 등이 있습니다. 각 방식은 정확도, 유연성, 설치 비용, 유지보수 용이성 등에서 차이가 있습니다.
위치 인식 및 경로 계획
AGV는 자신의 현재 위치를 정확히 파악하고, 목적지까지의 최적 경로를 계획해야 합니다. 위치 인식을 위해 엔코더, 자이로스코프, 가속도계와 같은 내부 센서와 더불어 레이저 스캐너, 카메라, RFID 리더 등의 외부 센서가 사용됩니다. 경로 계획 알고리즘은 A* 알고리즘, 다익스트라 알고리즘 등을 기반으로 하며, 장애물 회피 및 교통 관리 기능을 포함합니다.
제어 시스템
AGV의 두뇌 역할을 하는 제어 시스템은 내비게이션, 모터 제어, 안전 관리, 임무 수행 등 전체 작동을 조율합니다. 보통 메인 컨트롤러(PLC, 임베디드 컴퓨터 등)와 모터 제어기, 센서 인터페이스, 통신 모듈로 구성됩니다. 최근에는 인공지능 기술이 적용되어 학습 기반의 지능형 제어가 가능해지고 있습니다.
교통 관리 시스템
다수의 AGV가 동시에 작동하는 환경에서는 충돌 방지와 효율적인 작업 분배를 위한 교통 관리 시스템이 필수적입니다. 이 시스템은 중앙 집중식 또는 분산식으로 구현될 수 있으며, AGV 간 우선순위 설정, 교착 상태(deadlock) 방지, 경로 조정 등의 기능을 수행합니다.
AGV 시스템의 통신 기술은 AGV와 중앙 제어 시스템, 그리고 AGV 간의 정보 교환을 담당합니다. 주로 Wi-Fi, Bluetooth, 5G 등의 무선 통신 기술이 사용되며, 실시간 위치 정보, 상태 데이터, 작업 명령 등이 전송됩니다. 통신의 안정성과 보안성은 AGV 시스템의 신뢰성에 큰 영향을 미칩니다.
에너지 관리 기술은 AGV의 작동 시간과 효율성을 결정짓는 중요한 요소입니다. 대부분의 AGV는 충전식 배터리를 사용하며, 자동 충전 시스템, 에너지 소비 최적화 알고리즘, 배터리 상태 모니터링 기술 등이 적용됩니다. 최근에는 리튬이온 배터리, 수소 연료전지 등 고효율 에너지원도 도입되고 있습니다.
안전 시스템은 AGV 작동 중 발생할 수 있는 사고를 방지하기 위한 필수 요소입니다. 레이저 스캐너, 범퍼 센서, 3D 카메라 등의 안전 센서와 비상 정지 버튼, 경고음, 경고등과 같은 경고 장치가 통합되어 안전한 작동을 보장합니다. 또한 소프트웨어적으로 안전 구역 설정, 속도 제한, 충돌 예측 알고리즘 등이 구현됩니다.
AGV의 내비게이션 방식 개요
물리적 가이드 기반 내비게이션
마그네틱 테이프/스폿, 와이어 가이드, 색상 또는 반사 테이프와 같은 물리적 요소를 바닥에 설치하여 AGV가 이를 감지하고 따라가는 방식입니다. 설치가 간단하고 비용이 저렴하지만, 경로 변경 시 물리적인 인프라를 수정해야 하는 제약이 있습니다.
마커 기반 내비게이션
QR코드, 바코드, RFID 태그와 같은 마커를 환경 내 주요 위치에 설치하고, AGV가 이를 인식하여 자신의 위치를 파악하는 방식입니다. 물리적 가이드 방식보다 유연성이 높고, 추가 정보(작업 지시, 지점별 속도 제한 등)를 마커에 저장할 수 있습니다.
레이저 내비게이션
환경 내 고정된 위치에 레이저 반사기를 설치하고, AGV에 장착된 레이저 스캐너가 이를 감지하여 삼각측량 방식으로 정확한 위치를 계산하는 방식입니다. 높은 정확도와 신뢰성이 특징이지만, 초기 설치 비용이 높고 환경 변화에 민감할 수 있습니다.
자연 특징 기반 내비게이션(SLAM)
Simultaneous Localization and Mapping(SLAM) 기술을 활용하여 환경의 자연적인 특징(벽, 기둥, 선반 등)을 인식하고 지도를 생성하면서 동시에 자신의 위치를 파악하는 방식입니다. 물리적 인프라 없이도 작동 가능하여 높은 유연성을 제공하지만, 계산 복잡도가 높고 동적 환경에서 안정성 확보가 과제입니다.
각 내비게이션 방식은 고유한 장단점을 가지고 있어, 적용 환경과 요구사항에 따라 적합한 방식이 달라집니다. 예를 들어, 경로 변경이 거의 없는 고정된 생산 라인에서는 물리적 가이드 방식이 비용 효율적일 수 있으며, 자주 레이아웃이 변경되는 창고 환경에서는 SLAM 기술이 더 적합할 수 있습니다.
최근에는 여러 내비게이션 기술을 혼합한 하이브리드 방식도 많이 사용됩니다. 예를 들어, 메인 경로는 마그네틱 테이프를 따라 이동하되, 특정 작업 구역에서는 비전 시스템이나 SLAM을 활용하는 방식입니다. 이를 통해 각 기술의 장점을 최대화하고 단점을 보완할 수 있습니다.
내비게이션 기술의 발전 추세는 점차 물리적 인프라 의존도를 낮추고 환경 인식 능력을 높이는 방향으로 진행되고 있습니다. 특히 인공지능과 딥러닝 기술의 발전으로 카메라만으로도 정확한 위치 인식과 장애물 회피가 가능한 비전 기반 내비게이션이 주목받고 있습니다. 또한 5G 통신과 클라우드 컴퓨팅을 활용한 협업 내비게이션 기술도 발전하고 있어, 여러 AGV가 실시간으로 정보를 공유하며 더욱 효율적으로 작동할 수 있는 환경이 조성되고 있습니다.
마그네틱테이프 유도형 AGV
마그네틱테이프 유도형 AGV는 가장 널리 사용되는 내비게이션 방식 중 하나로, 바닥에 설치된 마그네틱 테이프를 따라 AGV가 이동하는 시스템입니다. 이 방식은 구현이 간단하고 비용 효율적이어서 많은 산업 현장에서 채택하고 있습니다.
작동 원리
마그네틱테이프 유도형 AGV의 핵심 원리는 다음과 같습니다:
- 자기장 감지: AGV 하부에 설치된 자기 센서가 바닥에 부착된 마그네틱 테이프에서 발생하는 자기장을 감지합니다.
- 중앙선 추적: 제어 시스템은 자기장 감지 정보를 바탕으로 AGV가 테이프의 중앙을 따라 이동하도록 조정합니다.
- 방향 및 속도 제어: 자기장의 세기와 방향을 분석하여 AGV의 방향과 속도를 실시간으로 제어합니다.
- 분기점 관리: 경로 분기점에서는 추가적인 마그네틱 마커(스폿)를 설치하여 AGV가 적절한 경로를 선택하도록 합니다.
장점
- 비교적 저렴한 초기 설치 비용
- 단순한 구조로 유지보수가 용이함
- 내비게이션 시스템의 높은 신뢰성
- 전자기 간섭이 적은 환경에서 안정적 작동
- 경로 변경 시 테이프만 재부착하면 되는 편리성
- 복잡한 소프트웨어나 강력한 컴퓨팅 성능이 필요 없음
단점
- 경로 유연성 제한(미리 정의된 경로만 이동 가능)
- 테이프 손상 시 내비게이션 오류 발생 가능
- 바닥 청소 및 유지관리에 주의 필요
- 분진이나 오염물질이 많은 환경에서 성능 저하
- 다수의 AGV 운영 시 교통 관리가 복잡해질 수 있음
- 레이아웃 변경 시 물리적 테이프 재설치 필요
주요 적용 분야
마그네틱테이프 유도형 AGV는 다음과 같은 환경에 특히 적합합니다:
- 고정된 레이아웃의 생산 라인: 경로 변경이 거의 없는 조립 라인이나 생산 현장
- 중소규모 창고: 주요 이동 경로가 고정적인 중소 규모 물류 창고
- 비용 효율성이 중요한 환경: 초기 투자 비용을 최소화해야 하는 중소기업
- 단순한 운영 환경: 경로가 단순하고 장애물이 적은 환경
마그네틱테이프 유도형 AGV의 기술적 발전 방향으로는 더 높은 정확도를 제공하는 고감도 자기 센서, 손상된 테이프 구간을 극복할 수 있는 보조 내비게이션 시스템 통합, 그리고 마그네틱 테이프를 바닥 내부에 매립하여 보호하는 방식 등이 있습니다. 또한 마그네틱 테이프에 RFID 태그를 결합하여 더 많은 정보(위치 데이터, 속도 제한 등)를 제공하는 하이브리드 시스템도 개발되고 있습니다.
비록 최신 내비게이션 기술에 비해 유연성이 제한적이지만, 마그네틱테이프 유도형 AGV는 여전히 비용 효율성과 신뢰성 면에서 많은 산업 현장에서 선호되는 솔루션으로 자리잡고 있습니다.
유선(와이어가이드) AGV
유선(와이어가이드) AGV는 마그네틱테이프와 함께 전통적인 AGV 내비게이션 방식 중 하나로, 바닥에 매립된 전선을 통해 생성되는 자기장을 감지하여 경로를 따라가는 시스템입니다. 이 방식은 1950년대 최초의 상업용 AGV에 사용된 이후 안정성과 내구성으로 인해 오랫동안 산업 현장에서 활용되어 왔습니다.
작동 원리
유선 유도형 AGV의 작동 원리는 다음과 같습니다:
- 유도 전선: 바닥 표면 아래 5-15mm 깊이에 전선을 매립하고, 이 전선에 특정 주파수(일반적으로 1-15kHz)의 교류 전류를 흘립니다.
- 자기장 생성: 전류가 흐르는 전선 주위에 형성되는 자기장이 내비게이션 신호로 작용합니다.
- 감지 센서: AGV 하부에 설치된 안테나 코일이 이 자기장을 감지하여 전선과의 거리와 방향을 판단합니다.
- 제어 시스템: 감지된 신호를 기반으로 AGV가 전선 경로를 정확히 따라가도록 조향 시스템을 제어합니다.
- 분기점 관리: 경로 분기점에서는 다른 주파수의 전류를 사용하거나 별도의 제어 신호를 전송하여 AGV가 올바른 경로를 선택하도록 합니다.
장점
- 매우 높은 신뢰성과 정확성
- 바닥 아래 매립되어 있어 물리적 손상 가능성이 낮음
- 바닥 청소나 일상적인 작업에 영향을 받지 않음
- 가혹한 환경(먼지, 습기 등)에서도 안정적 성능
- 전선을 통한 전력 및 데이터 전송 가능
단점
- 초기 설치 비용이 높고 공사가 복잡함
- 바닥 공사가 필요하여 시설 운영 중단 초래 가능
- 경로 변경 시 바닥 재공사 필요
- 극도로 제한된 경로 유연성
- 전기적 간섭에 취약할 수 있음
주요 적용 분야
유선 유도형 AGV는 다음과 같은 환경에 특히 적합합니다:
- 장기간 레이아웃 변경이 없는 생산 시설: 자동차 조립 라인, 대형 제조 공장
- 극한 환경: 먼지가 많거나 고온/저온 환경, 강한 진동이 있는 환경
- 고도의 정확성이 요구되는 작업: 정밀 부품 운반, 좁은 공간에서의 작동
- 장기적 운영이 예상되는 대규모 시설: 초기 투자비용이 높지만 장기적으로 유지보수 비용이 낮음
기술적 발전 추세로는 더 효율적인 전력 소비를 위한 최적화된 전송 주파수, 더 정확한 위치 파악을 위한 고감도 안테나 시스템, 그리고 전선을 통한 고급 데이터 통신(경로 정보, 속도 제한, 작업 지시 등)이 가능한 기술이 개발되고 있습니다. 또한 유선 유도 방식과 다른 내비게이션 기술(레이저, 비전 등)을 결합한 하이브리드 시스템도 등장하고 있어, 유선의 안정성과 다른 기술의 유연성을 함께 활용할 수 있게 되었습니다.
비록 설치 비용과 유연성 측면에서 한계가 있지만, 유선 유도형 AGV는 특히 극한 환경이나 장기적 안정성이 중요한 산업 현장에서 여전히 중요한 위치를 차지하고 있습니다. 새로운 기술의 등장에도 불구하고, 그 독보적인 신뢰성으로 인해 많은 기업들이 핵심 생산 라인에서는 여전히 이 전통적인 방식을 선호하고 있습니다.
QR/바코드 기반 AGV
QR코드나 바코드를 활용한 AGV 내비게이션 시스템은 바닥이나 벽에 부착된 QR코드 또는 바코드 마커를 스캔하여 위치를 파악하고 이동 경로를 결정하는 방식입니다. 이 방식은 물리적 가이드 방식(마그네틱 테이프, 와이어)보다 유연성이 높고, 레이저 내비게이션이나 SLAM보다는 비용이 저렴한 중간 수준의 솔루션으로 자리잡고 있습니다.
작동 원리
QR/바코드 기반 AGV의 작동 원리는 다음과 같습니다:
- 마커 설치: 사전에 정의된 위치에 QR코드나 바코드 마커를 바닥이나 벽면에 부착합니다. 각 마커에는 고유한 위치 정보와 추가 데이터(방향 지시, 속도 제한 등)가 인코딩되어 있습니다.
- 스캐너 장착: AGV에는 QR코드/바코드를 스캔할 수 있는 이미징 장치(카메라, 바코드 스캐너)가 장착됩니다.
- 마커 인식: AGV가 이동하면서 마커를 인식하여 현재 위치와 다음 행동에 대한 정보를 얻습니다.
- 위치 추정: 마커 사이의 구간에서는 휠 인코더, 관성 측정 장치(IMU) 등을 활용한 추측 항법(dead reckoning)으로 위치를 추정합니다.
- 경로 계획: 마커에서 얻은 정보와 목적지 정보를 바탕으로 최적 경로를 계산하고 이동합니다.
장점
- 설치가 간편하고 비용 효율적임
- 마커에 다양한 정보를 저장할 수 있어 고급 기능 구현 가능
- 경로 변경이 필요할 때 마커만 재배치하면 됨
- 바닥 청소나 유지보수에 영향을 적게 받음
- 다른 내비게이션 시스템과 쉽게 통합 가능
- 바코드/QR코드 기술이 성숙하여 신뢰성 높음
단점
- 마커 간 간격에서는 위치 오차 누적 가능
- 마커 손상이나 오염 시 인식 오류 발생 가능
- 마커의 지속적인 관리와 유지보수 필요
- 조명 조건에 영향을 받을 수 있음
- 완전한 자율 내비게이션에는 제한적
- 다수의 마커 설치 및 관리에 따른 운영 부담
주요 적용 분야
QR코드/바코드 기반 AGV는 다음과 같은 환경에 특히 적합합니다:
- 중소규모 창고 및 물류 센터: 지게차형 AGV나 카트형 AGV가 운영되는, 비교적 단순한 이동 패턴을 가진 환경
- 경로 변경이 가끔 필요한 제조 현장: 주기적으로 레이아웃이 변경되지만 완전한 자율성은 필요하지 않은 환경
- 임시 설치 환경: 별도의 바닥 공사 없이 빠르게 설치해야 하는 경우
- 하이브리드 내비게이션 시스템: 다른 내비게이션 방식(예: 마그네틱 테이프)과 함께 보조적으로 사용
QR코드/바코드 기반 내비게이션 기술의 발전 방향으로는 내구성이 높은 고성능 마커 개발, 더 넓은 각도와 먼 거리에서도 인식 가능한 고급 이미징 기술, 마커 간 위치 추정 정확도를 높이기 위한 센서 퓨전 기술, 그리고 마커 데이터와 중앙 관리 시스템 간의 실시간 동기화 기능 등이 있습니다.
이 기술은 특히 기존 바코드/QR코드 인프라를 이미 갖춘 물류 환경에서 쉽게 도입할 수 있는 장점이 있습니다. 많은 창고 관리 시스템(WMS)이 이미 이러한 코드 체계를 사용하고 있어 AGV 시스템과의 통합이 수월하기 때문입니다. 또한 새로운 데이터 매트릭스 기술과 증강 현실(AR) 기술을 접목한 고급 마커 시스템도 개발되고 있어, 더욱 정확하고 다양한 정보를 제공할 수 있는 가능성이 열리고 있습니다.
라이다(LiDAR) 및 비전 기반 AGV
라이다(LiDAR) 및 비전 기반 AGV 내비게이션 시스템은 레이저 스캐닝 기술이나 카메라를 활용하여 주변 환경을 인식하고 위치를 파악하는 고급 내비게이션 방식입니다. 이 기술은 물리적 가이드 방식보다 훨씬 높은 유연성을 제공하며, 특히 레이저 내비게이션은 높은 정확도로 인해 고급 물류 환경에서 널리 사용되고 있습니다.
라이다(LiDAR) 기반 내비게이션
라이다 기반 내비게이션의 핵심 원리는 다음과 같습니다:
- 반사기 설치: 환경 내 고정된 위치(벽, 기둥 등)에 레이저 반사기(reflector)를 설치합니다.
- 레이저 스캐닝: AGV에 장착된 레이저 스캐너가 360도 회전하며 주변을 스캔하고 반사기의 위치를 감지합니다.
- 삼각측량: 여러 반사기의 상대적 위치를 측정하여 삼각측량 방식으로 AGV의 정확한 위치와 방향을 계산합니다.
- 경로 계획: 미리 입력된 환경 지도와 현재 위치 정보를 바탕으로 목적지까지의 최적 경로를 계획합니다.
- 장애물 감지: 레이저 스캐너는 동시에 주변 장애물을 감지하여 충돌을 방지합니다.
비전 기반 내비게이션
비전 기반 내비게이션의 핵심 원리는 다음과 같습니다:
- 카메라 장착: AGV에 단일 또는 복수의 카메라(일반 카메라, 스테레오 카메라, 3D 카메라 등)를 장착합니다.
- 이미지 처리: 카메라로 촬영한 이미지를 실시간으로 처리하여 주변 환경의 특징(천정 구조물, 벽면 패턴, 표지 등)을 인식합니다.
- 위치 인식: 미리 저장된 참조 이미지나 특징점 지도와 현재 이미지를 비교하여 위치를 파악합니다.
- 시각적 주행: 인식된 환경 특징을 기반으로 주행 경로를 생성하고 따라갑니다.
- 객체 인식: 컴퓨터 비전 기술을 활용하여 사람, 물체, 장애물 등을 인식하고 대응합니다.
라이다 기반 내비게이션의 장점
- 1-2cm 수준의 매우 높은 위치 정확도
- 조명 조건에 덜 민감함
- 반사기만 설치하면 되어 비교적 간단한 인프라
- 신뢰성 높고 안정적인 성능
- 동시에 안전 센서 역할도 수행
비전 기반 내비게이션의 장점
- 풍부한 환경 정보 획득 가능
- 특정 마커 없이도 작동 가능
- 3D 공간 인식 가능
- 객체 인식 및 분류 기능
- 상대적으로 저렴한 하드웨어 비용
라이다 기반 내비게이션의 단점
- 반사기 설치 및 유지관리 필요
- 초기 설정 및 맵핑 작업 복잡
- 고가의 장비 비용
- 먼지가 많은 환경에서 성능 저하 가능
비전 기반 내비게이션의 단점
- 조명 조건에 민감
- 계산 리소스 요구량 높음
- 환경 변화에 취약할 수 있음
- 정확도가 라이다보다 낮을 수 있음
최근에는 라이다와 비전 기술을 함께 활용하는 센서 퓨전 접근법이 증가하고 있습니다. 이를 통해 각 기술의 장점을 살리고 단점을 보완하여 더욱 강력하고 신뢰성 높은 내비게이션 시스템을 구현할 수 있습니다. 예를 들어, 라이다의 정확한 거리 측정 능력과 비전 시스템의 풍부한 객체 인식 능력을 결합하여 보다 지능적인 AGV 운영이 가능해집니다.
또한 인공지능과 딥러닝 기술의 발전으로 비전 기반 내비게이션의 성능이 크게 향상되고 있으며, 라이다 기술도 소형화, 고성능화, 저가격화가 진행되면서 활용 범위가 넓어지고 있습니다. 특히 솔리드 스테이트 라이다(Solid-state LiDAR)와 같은 새로운 기술의 등장으로 더욱 내구성 있고 경제적인 시스템 구현이 가능해지고 있습니다.
자연특징 내비게이션(SLAM) AGV
자연특징 내비게이션, 특히 SLAM(Simultaneous Localization And Mapping) 기술을 활용한 AGV는 물리적 가이드나 인위적 마커에 의존하지 않고, 환경의 자연적인 특징을 인식하여 지도를 생성하고 위치를 파악하는 고급 내비게이션 시스템입니다. 이 기술은 AGV를 넘어 자율이동로봇(AMR)의 핵심 기술로 자리잡고 있으며, 산업 자동화의 새로운 지평을 열고 있습니다.
SLAM 기술의 작동 원리
SLAM 기반 내비게이션의 핵심 원리는 다음과 같습니다:
- 센서 데이터 수집: 라이다(LiDAR), 카메라, 초음파 센서, 관성 측정 장치(IMU) 등 다양한 센서를 통해 주변 환경 데이터를 수집합니다.
- 특징점 추출: 수집된 데이터에서 벽, 기둥, 선반 등 환경의 고유한 특징점(landmark)을 식별합니다.
- 지도 생성: 인식된 특징점들을 연결하여 환경의 지도를 실시간으로 생성합니다.
- 위치 추정: 현재 센서 데이터와 생성된 지도를 비교하여 로봇의 위치와 방향을 추정합니다.
- 동시 최적화: 지도 생성과 위치 추정을 동시에 수행하며 지속적으로 정보를 업데이트합니다.
- 경로 계획: 생성된 지도와 현재 위치를 바탕으로 목적지까지의 최적 경로를 계획합니다.
장점
- 물리적 인프라(마그네틱 테이프, 반사기 등) 설치가 필요 없음
- 높은 유연성으로 환경 변화에 쉽게 적응 가능
- 초기 설치 비용 절감 및 설치 시간 단축
- 레이아웃 변경 시 재프로그래밍만으로 대응 가능
- 장애물 감지 및 회피 능력이 우수함
- 지속적인 환경 학습을 통한 성능 개선
단점
- 컴퓨팅 요구사항이 높아 고성능 하드웨어 필요
- 환경이 너무 단조롭거나 지속적으로 변하는 경우 성능 저하
- 초기 맵핑 과정에서 시간과 전문성 필요
- 위치 정확도가 전통적인 방식보다 떨어질 수 있음
- 복잡한 알고리즘으로 인한 문제 해결의 어려움
- 고가의 센서 및 프로세싱 장비 비용
SLAM 기술의 유형
SLAM 기술은 사용하는 센서와 알고리즘에 따라 여러 유형으로 나눌 수 있습니다:
- 2D SLAM: 주로 단일 평면에서의 이동을 위한 2차원 지도를 생성합니다. 2D 라이다를 활용하며, 대부분의 실내 AGV에 적용됩니다.
- 3D SLAM: 3차원 공간을 모델링하여 층간 이동이나 복잡한 지형에서도 작동 가능합니다. 3D 라이다, 깊이 카메라 등을 활용합니다.
- Visual SLAM: 카메라 이미지를 주요 입력으로 사용하여 시각적 특징을 기반으로 맵핑과 위치 추정을 수행합니다.
- LiDAR SLAM: 라이다 센서 데이터를 기반으로 하며, 거리 측정의 정확도가 높아 산업용 AGV에 많이 사용됩니다.
- Fusion SLAM: 여러 종류의 센서 데이터를 통합하여 더 높은 정확도와 안정성을 제공합니다.
SLAM 기술의 발전 방향으로는 보다 효율적인 알고리즘 개발로 계산 요구사항 감소, 딥러닝과의 결합을 통한 더 지능적인 환경 인식, 더 작고 저렴하면서도 정밀한 센서 개발, 그리고 여러 로봇 간 지도 정보 공유를 통한 협업적 SLAM 구현 등이 있습니다.
SLAM 기술은 특히 레이아웃 변경이 빈번한 물류 센터, 사람과 로봇이 함께 작업하는 협업 환경, 그리고 다양한 작업을 유연하게 수행해야 하는 생산 시설에서 큰 이점을 제공합니다. 비록 현재는 초기 비용과 기술적 복잡성으로 인해 도입 장벽이 있지만, 하드웨어 성능 향상과 소프트웨어 발전으로 점차 보편화되고 있으며, 미래 로봇 내비게이션의 표준 기술로 자리잡아가고 있습니다.
혼합형 내비게이션 AGV
혼합형(하이브리드) 내비게이션 AGV는 두 가지 이상의 내비게이션 기술을 조합하여 각 기술의 장점을 활용하고 단점을 보완하는 시스템입니다. 이러한 접근 방식은 특히 다양한 작업 환경과 요구사항을 가진 복잡한 산업 현장에서 유연성과 신뢰성을 동시에 확보하기 위해 점차 보편화되고 있습니다.
혼합형 내비게이션의 주요 조합 유형
가이드 기반 + 자연 특징 기반
가장 일반적인 조합으로, 마그네틱 테이프나 QR코드와 같은 물리적 가이드와 SLAM이나 비전 시스템을 함께 사용합니다. 주요 이동 경로는 물리적 가이드를 따라 이동하고, 특정 작업 구역이나 예외 상황에서는 자연 특징 내비게이션으로 전환합니다.
라이다 + 비전 시스템
라이다의 정확한 거리 측정 능력과 비전 시스템의 풍부한 환경 인식 능력을 결합합니다. 라이다는 주로 위치 파악과 장애물 감지에 활용되고, 카메라는 객체 식별과 세부 특징 인식에 사용됩니다.
절대 위치 + 상대 위치 측정
GPS, 비콘, QR코드 등을 통한 절대 위치 측정과 휠 인코더, IMU(관성 측정 장치) 등을 통한 상대 위치 측정을 결합합니다. 절대 위치 데이터가 가용할 때는 이를 기준으로 하고, 그 사이에는 상대 위치 추정으로 연속성을 유지합니다.
인프라 기반 + 무인프라 방식
설치된 인프라(반사기, 비콘 등)가 있는 구역에서는 이를 활용하고, 인프라가 없는 구역에서는 자체 센서와 알고리즘으로 내비게이션합니다. 이 방식은 단계적 자동화 도입에 유용합니다.
혼합형 내비게이션의 작동 원리
혼합형 내비게이션 AGV의 핵심 작동 원리는 다음과 같습니다:
- 다중 센서 시스템: 여러 종류의 센서(라이다, 카메라, 자기 센서, 휠 인코더 등)를 장착하여 다양한 환경 데이터를 수집합니다.
- 센서 퓨전: 수집된 여러 센서 데이터를 통합 처리하여 더 정확하고 신뢰성 있는 정보를 생성합니다.
- 상황 인식: 현재 환경과 작업 조건을 분석하여 최적의 내비게이션 방식을 결정합니다.
- 동적 전환: 환경이나 작업 요구사항에 따라 내비게이션 방식을 자동으로 전환합니다.
- 오류 보정: 한 시스템에서 오류가 발생하더라도 다른 시스템으로 보완하여 작동 연속성을 유지합니다.
장점
- 단일 내비게이션 방식보다 높은 신뢰성과 견고성
- 다양한 환경 조건에 적응 가능한 유연성
- 내비게이션 오류 발생 시 대체 시스템으로 백업
- 기존 인프라와 신기술의 점진적 통합 가능
- 작업 특성에 따라 최적의 내비게이션 방식 선택 가능
단점
- 시스템 복잡성 증가로 개발 및 유지보수 난이도 상승
- 여러 센서와 처리 시스템으로 인한 비용 증가
- 다양한 시스템 간 통합 및 조율의 기술적 어려움
- 더 많은 연산 능력과 에너지 소비 필요
- 다중 시스템 보정 및 설정의 복잡성
실제 적용 사례로는, 대형 물류 센터에서 주요 이동 통로는 마그네틱 테이프를 따라 이동하고 세부 작업 구역에서는 비전 기반 정밀 위치 파악을 하는 시스템, 또는 공장 내 고정 작업장 간 이동은 레이저 내비게이션을 사용하고 동적 환경이 많은 구역에서는 SLAM으로 전환하는 시스템 등이 있습니다.
혼합형 내비게이션 기술의 발전 방향으로는 인공지능 기반의 자동 모드 전환 알고리즘 개발, 다양한 센서 데이터의 더 효율적인 통합을 위한 고급 센서 퓨전 기술, 클라우드 기반 맵 처리와 온보드 프로세싱의 결합, 그리고 다중 AGV 간 내비게이션 정보 공유를 통한 협업적 내비게이션 구현 등이 있습니다.
혼합형 내비게이션은 특히 기존 시스템에서 새로운 기술로 전환하는 과도기적 환경이나, 다양한 작업 조건을 가진 복잡한 산업 현장에서 큰 가치를 제공합니다. 초기 투자와 복잡성이 증가하지만, 장기적으로는 더 높은 안정성과 유연성으로 인해 투자 대비 효과가 우수한 솔루션으로 평가받고 있습니다.
슬리브형 AGV(셔틀 AGV)
슬리브형 AGV(셔틀 AGV)는 낮은 프로파일의 소형 로봇으로 선반 아래로 진입하여 전체 선반 유닛을 들어 올려 운반하는 방식의 무인운반차입니다. 특히 자동화된 창고 시스템에서 저장 공간의 효율적 활용과 빠른 물품 접근을 위해 널리 사용되고 있으며, '언더라이드 AGV(Underride AGV)' 또는 '선반 반송 로봇'이라고도 불립니다.
슬리브형 AGV의 작동 원리
슬리브형 AGV의 기본 작동 원리는 다음과 같습니다:
- 위치 이동: AGV가 목표 선반 아래로 정확히 이동합니다.
- 선반 인식: 센서를 통해 선반의 정확한 위치와 상태를 인식합니다.
- 리프팅 메커니즘 작동: 내장된 리프팅 시스템을 통해 선반을 바닥에서 몇 센티미터 들어올립니다.
- 선반 운반: 선반을 안정적으로 들어 올린 상태에서 목적지(작업자 스테이션, 다른 보관 위치 등)로 이동합니다.
- 선반 하역: 목적지에 도착하면 리프팅 시스템을 낮추어 선반을 내려놓습니다.
- 다음 작업 준비: 새로운 임무를 위해 대기 위치로 이동하거나 다음 선반으로 이동합니다.
기술적 특징
- 낮은 프로파일 설계: 선반 아래로 쉽게 진입할 수 있는 얇은 높이
- 정밀 리프팅 시스템: 무거운 선반을 안정적으로 들어 올릴 수 있는 견고한 리프트 메커니즘
- 고정밀 내비게이션: 선반 아래 정확히 위치하기 위한 정밀한 위치 제어 시스템
- 배터리 관리: 장시간 작동을 위한 고효율 배터리와 자동 충전 시스템
- 안전 센서: 이동 중 장애물 감지와 충돌 방지를 위한 센서 시스템
- 통합 제어: 창고 관리 시스템(WMS)과 연동되는 지능형 제어 시스템
주요 적용 분야
- 전자상거래 물류 센터: 다품종 소량 주문의 효율적 처리
- 자동화 창고: 공간 활용 최적화와 빠른 피킹 작업
- 제조업 부품 창고: 필요한 부품을 생산 라인으로 신속 공급
- 냉장/냉동 창고: 저온 환경에서의 자동화된 물품 취급
- 소매업 백룸 관리: 매장 재고의 효율적 관리와 보충
- 도서관 자동화: 도서 보관 및 검색 자동화
슬리브형 AGV의 장단점
장점
공간 효율성: 바닥 면적을 최대한 활용하며 선반 간 통로 폭을 최소화할 수 있습니다. 고밀도 보관이 가능해 창고 용량이 크게 증가합니다.
장점
작업 효율성: '상품을 사람에게(Goods-to-Person)' 방식으로 피킹 효율을 크게 향상시킵니다. 작업자는 고정된 작업 스테이션에서 작업할 수 있어 이동 시간이 절약됩니다.
장점
유연한 확장성: 로봇과 선반을 모듈식으로 추가하여 시스템을 쉽게 확장할 수 있습니다. 초기 투자를 최소화하고 사업 성장에 따라 점진적 투자가 가능합니다.
단점
초기 설치 비용: 전체 시스템(로봇, 선반, 소프트웨어 등) 구축에 상당한 투자가 필요합니다. 특히 소규모 기업에는 초기 부담이 클 수 있습니다.
단점
특화된 선반 요구: 일반 선반보다 AGV와 호환되는 특수 설계된 선반이 필요하여 기존 창고 인프라를 활용하기 어려울 수 있습니다.
단점
중량 제한: 대부분의 슬리브형 AGV는 중량 제한이 있어 매우 무거운 물품 취급에는 제한이 있을 수 있습니다.
슬리브형 AGV 기술의 최신 발전 동향으로는 더 높은 적재 용량을 가진 모델 개발, 더 빠른 이동 속도와 리프팅 성능 구현, 인공지능을 활용한 주문 예측 및 선제적 선반 배치 최적화, 군집 제어 알고리즘을 통한 다수 로봇의 효율적 조율, 그리고 증강 현실(AR)을 활용한 피킹 작업 지원 시스템 등이 있습니다.
대표적인 슬리브형 AGV 시스템으로는 아마존의 Kiva(현 Amazon Robotics), 키바시스템즈의 후속 모델인 Locus Robotics, 중국의 Geek+, 그리고 한국의 뉴로메카 등이 있으며, 전 세계적으로 전자상거래의 폭발적 성장에 따라 이 분야의 수요와 기술 개발이 계속 증가하고 있습니다.
팔레트운반형 AGV
팔레트운반형 AGV는 표준 팔레트에 적재된 화물을 운반하기 위해 특별히 설계된 무인운반차로, 창고, 물류 센터, 제조 시설 등에서 널리 사용됩니다. 이 유형의 AGV는 기존의 수동 지게차나 팔레트 잭을 대체하여 자동화된 물류 운영을 가능하게 합니다.
팔레트운반형 AGV의 구조와 작동 원리
팔레트운반형 AGV의 기본 구성과 작동 원리는 다음과 같습니다:
- 기본 구조: 일반적으로 포크(fork) 메커니즘이 장착된 형태로, 팔레트 하부의 개구부에 포크를 삽입하여 들어올릴 수 있도록 설계되어 있습니다.
- 팔레트 접근: AGV가 정확한 각도와 위치로 팔레트에 접근합니다. 이를 위해 비전 시스템이나 정밀 위치 센서가 활용됩니다.
- 포크 삽입: 포크를 팔레트 개구부에 정확히 삽입합니다. 이 과정에서 팔레트 위치를 정밀하게 감지하는 센서가 작동합니다.
- 리프팅: 유압 또는 전동 리프팅 시스템을 통해 팔레트를 필요한 높이로 들어올립니다.
- 운반: 팔레트를 들어 올린 상태에서 목적지로 이동합니다. 이동 중에는 균형 유지와 안전 주행을 위한 다양한 제어 시스템이 작동합니다.
- 하역: 목적지에 도착하면 팔레트를 지정된 위치에 정확히 내려놓습니다.
팔레트운반형 AGV의 주요 유형
- 포크형(Fork-Type): 전통적인 지게차와 유사한 형태로, 앞쪽에 포크가 설치되어 팔레트를 정면에서 접근하여 들어올립니다.
- 스트래들형(Straddle-Type): 팔레트 측면에서 접근하여 양 다리(straddle) 사이로 팔레트를 끼우고 들어올리는 방식입니다.
- 컨베이어 통합형: AGV 상부에 컨베이어가 설치되어 있어 팔레트를 들어올린 후 상부 컨베이어로 이동시켜 운반하는 방식입니다.
- 리프트 데크형(Lift Deck): 전체 상부 플랫폼이 상하로 이동하여 팔레트를 들어올리는 방식입니다.
핵심 기술 요소
- 포크 제어 시스템: 정확한 포크 삽입과 리프팅을 위한 정밀 제어 기술
- 하중 감지 및 관리: 다양한 무게의 팔레트를 안전하게 처리하기 위한 하중 감지 및 관리 시스템
- 3D 센싱: 팔레트 위치와 형태를 정확히 인식하기 위한 3D 비전 또는 라이다 기술
- 안정성 제어: 이동 중 화물의 안정성을 유지하기 위한 제어 알고리즘
- 안전 기능: 무거운 화물 운반에 따른 특화된 안전 센서 및 시스템
장점
- 표준 팔레트 호환성: 기존의 물류 인프라와 호환되어 도입이 용이함
- 높은 적재 용량: 대부분 1-2톤 이상의 화물을 운반할 수 있어 중량물 취급에 적합
- 다층 적재 가능: 일부 모델은 높은 위치의 랙에도 팔레트를 적재할 수 있음
- 작업 안전성: 무거운 팔레트 취급 시 발생할 수 있는 작업자 부상 위험 감소
- 24시간 운영: 인간 작업자의 피로나 교대 없이 연속 작동 가능
단점
- 팔레트 표준화 필요: 일정한 규격과 품질의 팔레트가 필요함
- 초기 투자 비용: 고성능 리프팅 메커니즘과 안전 시스템으로 인한 높은 비용
- 공간 요구사항: 팔레트 접근과 조작을 위한 충분한 공간이 필요함
- 기술적 복잡성: 정확한 팔레트 감지와 포크 조작의 기술적 어려움
- 바닥 상태 의존성: 평평하고 안정적인 바닥 조건이 필요함
주요 적용 분야
팔레트운반형 AGV는 다음과 같은 환경에서 특히 효과적으로 활용됩니다:
- 물류 창고: 입고, 출고, 보관 공정에서 팔레트 단위의 물품 이동
- 제조 시설: 원자재 공급, 반제품 이동, 완제품 보관 등의 작업
- 냉장/냉동 창고: 극한 환경에서의 팔레트 운반 자동화
- 대형 유통 센터: 대량의 팔레트 이동이 필요한 유통 현장
- 항만/공항 물류: 컨테이너와 연계된 팔레트 물류 처리
최근 기술 발전 동향으로는 인공지능과 머신 비전을 활용한 더 정확한 팔레트 인식 및 접근 기술, 다양한 팔레트 유형을 자동으로 감지하고 대응하는 적응형 포크 시스템, 보다 높은 리프팅 높이와 적재 용량을 가진 모델 개발, 그리고 팔레트 정보를 자동으로 스캔하고 인식하는 통합 식별 시스템 등이 있습니다.
팔레트운반형 AGV는 물류 자동화의 중요한 구성 요소로, 특히 인력 부족과 안전 요구사항이 증가하는 현대 산업 환경에서 그 중요성이 계속 증가하고 있습니다. 앞으로는 더욱 지능적이고 유연한 팔레트 취급 기능을 갖춘 모델들이 계속 개발될 것으로 전망됩니다.
견인(토잉)형 AGV
견인(토잉)형 AGV는 여러 개의 카트나 트레일러를 연결하여 견인하는 방식으로 대량의 물품을 효율적으로 운반하는 무인운반차입니다. 기차와 유사한 형태로 작동하며, 특히 생산 라인 간 자재 공급이나 반복적인 운반 경로가 있는 환경에서 널리 사용됩니다.
견인형 AGV의 구조와 작동 원리
견인형 AGV의 기본 구성과 작동 원리는 다음과 같습니다:
- 기본 구조: 전방에 강력한 구동 시스템을 갖추고 후방에 카트를 연결할 수 있는 히치(hitch) 또는 커플링 시스템이 장착되어 있습니다.
- 카트 연결: 특수 설계된 카트나 트레일러를 AGV의 히치에 연결합니다. 자동 또는 수동 연결 방식이 있습니다.
- 하중 분산: 견인 AGV 자체는 화물을 적재하지 않고 견인력만 제공하며, 실제 화물은 연결된 카트에 분산 적재됩니다.
- 경로 주행: 내비게이션 시스템(마그네틱 테이프, 레이저 등)을 통해 정해진 경로를 따라 이동합니다.
- 코너링 제어: 여러 카트를 견인할 때 특히 중요한 코너링 제어 시스템이 안정적인 회전을 가능하게 합니다.
- 카트 분리/결합: 특정 지점에서 카트를 자동으로 분리하거나 새로운 카트를 결합할 수 있는 시스템을 갖춘 경우도 있습니다.
견인형 AGV의 주요 특징
다중 카트 견인: 일반적으로 3-5개, 때로는 그 이상의 카트를 동시에 견인할 수 있어 한 번의 이동으로 대량 물품 운반이 가능합니다. 카트 디자인은 용도에 따라 다양하게 맞춤 제작됩니다.
고견인력 설계
여러 카트를 효과적으로 견인하기 위한 강력한 모터와 구동 시스템을 갖추고 있습니다. 일부 모델은 수 톤의 화물을 견인할 수 있는 능력을 보유하고 있습니다.
경로 최적화
카트 결합/분리 지점, 대기 구역, 최적 이동 경로 등을 고려한 종합적인 운영 계획이 중요합니다. 효율적인 경로 설계는 전체 시스템 성능에 큰 영향을 미칩니다.
안전 시스템
긴 이동 편성으로 인한 특수한 안전 요구사항을 충족하기 위한 전후방 안전 센서, 비상 정지 시스템, 소리/빛 경고장치 등이 장착됩니다. 특히 회전 시 넓은 공간이 필요하므로 이에 대한 안전 대책이 중요합니다.
장점
- 높은 운반 효율성: 한 번의 이동으로 다량의 물품을 운반할 수 있음
- 에너지 효율성: 다수의 AGV를 개별 운영하는 것보다 에너지 효율이 높음
- 공간 활용: 주행 통로 하나로 여러 카트가 이동하여 공간 효율적
- 시스템 단순화: 제어해야 할 AGV 수가 적어 시스템 복잡성 감소
- 유연한 적재: 다양한 종류의 카트를 연결하여 여러 물품 유형 운반 가능
- 비용 효율성: 견인 유닛 하나로 여러 카트를 운영하여 비용 절감
단점
- 공간 제약: 회전 반경이 크고 넓은 통로가 필요함
- 경로 유연성 제한: 복잡한 경로나 좁은 공간에서 운영이 어려움
- 인프라 의존성: 대부분 고정된 경로를 따라 이동하도록 설계됨
- 카트 관리: 카트 결합/분리 지점의 관리와 조율이 필요함
- 속도 제한: 안전한 견인을 위해 속도가 제한적임
- 고정 용량: 견인력과 카트 수가 고정되어 소량 운반 시 비효율적일 수 있음
주요 적용 분야
견인형 AGV는 다음과 같은 환경에서 특히 효과적으로 활용됩니다:
- 자동차 제조 공장: 조립 라인에 부품 공급, 공정 간 반제품 이동
- 대규모 제조 시설: 원자재 공급, 완제품 운반 등 규칙적인 물류 이동
- 신문 인쇄소: 용지 롤 운반, 인쇄된 신문 배포 구역으로 이동
- 우편/택배 분류 센터: 대량의 우편물/소포 이동
- 식품 가공 시설: 원료 공급, 포장된 제품 운반
- 병원/의료 시설: 린넨, 의약품, 식사, 의료 폐기물 등 정기적인 운반 작업
최근 기술 발전 동향으로는 자동 카트 연결/분리 시스템 개발, 더 정밀한 코너링 제어를 위한 고급 알고리즘, 카트별 상태 모니터링 및 추적 기능, 더 높은 견인력과 에너지 효율성을 위한 구동 시스템 개선, 그리고 유연한 경로 변경이 가능한 내비게이션 시스템 통합 등이 있습니다.
견인형 AGV는 오랜 역사를 가진 검증된 기술이지만, 최신 센서와 제어 기술의 통합으로 계속 발전하고 있으며, 대규모 물류 이동이 규칙적으로 발생하는 산업 환경에서 여전히 가장 효율적인 자동화 솔루션 중 하나로 인정받고 있습니다.
카트형 AGV
카트형 AGV는 상단에 평평한 적재 공간을 갖춘 소형 무인운반차로, 주로 부품, 반제품, 공구 등 비교적 가벼운 물품을 효율적으로 운반하는 데 사용됩니다. 이 유형의 AGV는 제조 현장, 물류 센터, 병원 등 다양한 환경에서 유연한 물류 이동을 지원하는 가장 보편적인 AGV 형태 중 하나입니다.
카트형 AGV의 구조와 특징
카트형 AGV의 기본 구성과 주요 특징은 다음과 같습니다:
- 기본 구조: 일반적으로 낮은 높이의 플랫폼 형태로, 상부에 평평한 적재 공간과 하부에 구동 시스템을 갖추고 있습니다.
- 적재 플랫폼: 평평한 상단 표면에 물품을 직접 적재하거나, 특수 설계된 컨테이너, 바구니, 또는 랙을 올려놓을 수 있습니다.
- 크기와 용량: 일반적으로 폭 0.5-1m, 길이 0.8-1.5m 크기에 50-500kg 정도의 적재 용량을 가지고 있으나, 용도에 따라 다양한 크기와 용량이 존재합니다.
- 내비게이션 시스템: 마그네틱 테이프, QR코드, 레이저 내비게이션, SLAM 등 다양한 내비게이션 방식을 적용할 수 있습니다.
- 충전 시스템: 자동 충전 스테이션을 활용한 배터리 충전 또는 배터리 교체 방식을 사용합니다.
카트형 AGV의 변형 유형
- 평면형(Flat Deck): 가장 기본적인 형태로, 평평한 상단 표면에 물품을 직접 적재
- 컨베이어 통합형: 상단에 롤러나 벨트 컨베이어가 설치되어 물품의 자동 적재/하역 가능
- 리프트 테이블형: 적재 플랫폼의 높이를 조절할 수 있어 다양한 높이의 작업대와 연동 가능
- 특수 랙 장착형: 특정 부품이나 컨테이너에 최적화된 특수 랙이나 홀더 장착
- 모듈형: 용도에 따라 상단 모듈을 교체하여 다양한 기능으로 변형 가능
주요 기술 요소
- 정밀 구동 시스템: 좁은 공간에서도 정확한 이동과 회전이 가능한 구동 및 조향 시스템
- 하중 감지: 적재 하중을 감지하여 최적의 가속/감속 및 에너지 관리를 수행
- 안전 시스템: 전/후방 안전 센서, 비상 정지 버튼, 경고 신호 등 작업자 안전을 위한 장치
- 상호작용 인터페이스: 작업자와의 통신을 위한 디스플레이, 버튼, 표시등 등의 인터페이스
- 연동 시스템: 작업 스테이션, 생산 설비, 자동 문 등 주변 시스템과의 연동 기능
카트형 AGV의 장단점
장점
- 다용도성: 다양한 종류의 물품을 운반할 수 있는 유연한 설계
- 컴팩트한 크기: 좁은 공간에서도 효율적으로 작동 가능
- 쉬운 작동 및 유지보수: 단순한 구조로 관리가 용이함
- 비용 효율성: 다른 AGV 유형에 비해 상대적으로 저렴한 비용
- 확장성: 필요에 따라 쉽게 추가 도입이 가능한 모듈식 시스템
단점
- 제한된 적재 용량: 대형 중량물 운반에는 적합하지 않음
- 적재물 보안: 고정 장치가 없으면 급정지나 충돌 시 적재물 이탈 가능성
- 수동 적재/하역: 대부분 작업자의 수동 적재 및 하역 작업 필요
- 평평한 바닥 필요: 불규칙한 표면이나 경사면에서 운영이 어려움
- 통로 필요: 양방향 통행을 위한 충분한 통로 폭 확보 필요
주요 적용 분야
카트형 AGV는 다음과 같은 환경에서 특히 효과적으로 활용됩니다:
제조 현장
생산 라인 간 부품 및 반제품 운반, 공구 및 소모품 배달, 완제품 운반 등 경량 물류 작업에 활용됩니다. 특히 전자 제품, 자동차 부품, 정밀 기계 등의 생산 현장에서 널리 사용됩니다.
의료 환경
병원에서 약품, 린넨, 의료 용품, 검체, 식사 등을 운반하는 데 활용됩니다. 청결하고 조용한 작동으로 환자 환경에 적합합니다.
소형 물류 센터
소형 제품 피킹, 분류 작업, 포장 구역으로의 제품 운반 등에 활용됩니다. 특히 전자상거래 물류에서 주문별 물품 수집과 운반에 효과적입니다.
연구 시설 및 실험실
실험 샘플, 장비, 위험물질 등의 안전한 운반에 활용됩니다. 특히 클린룸 환경에서도 사용 가능한 모델이 있습니다.
최근 기술 발전 동향으로는 자율 적재/하역 기능 강화, IoT 기술을 활용한 실시간 위치 및 상태 모니터링, 협업 로봇(코봇)과의 통합을 통한 피킹 및 적재 자동화, 인공지능 기반 경로 최적화 및 작업 우선순위 결정, 그리고 증강현실(AR)을 활용한 운영자 인터페이스 개선 등이 있습니다.
카트형 AGV는 비교적 단순한 구조와 쉬운 통합성으로 인해 자동화 도입의 첫 단계로 많이 선택되며, 다양한 산업 현장에서 점진적 자동화 전략의 중요한 구성 요소가 되고 있습니다. 특히 인간 작업자와의 협업을 고려한 설계와 안전 기능으로, 완전 자동화가 아닌 부분 자동화 환경에서도 효과적으로 활용될 수 있는 장점이 있습니다.
지게차형 AGV
지게차형 AGV는 기존의 수동 지게차를 자동화한 형태로, 팔레트나 대형 화물을 들어 올리고 높은 선반에도 적재할 수 있는 기능을 갖춘 무인운반차입니다. 이 유형의 AGV는 창고 및 물류 센터에서 특히 높은 공간 활용도를 요구하는 환경에 적합하며, 기존 수동 지게차의 역할을 자동화하여 효율성과 안전성을 높일 수 있습니다.
지게차형 AGV의 구조와 작동 원리
지게차형 AGV의 기본 구성과 작동 원리는 다음과 같습니다:
- 기본 구조: 전통적인 지게차와 유사한 형태로, 전방에 포크(fork)를 갖추고 있으며 이를 수직으로 들어 올릴 수 있는 마스트(mast) 시스템을 갖추고 있습니다.
- 리프팅 시스템: 유압 또는 전동 방식의 리프팅 시스템을 통해 포크를 수직으로 올리고 내릴 수 있으며, 일부 모델은 5-10m 이상의 높이까지 도달할 수 있습니다.
- 포크 제어: 포크의 수평 이동, 틸팅(기울기 조절), 사이드 시프트(좌우 이동) 등을 정밀하게 제어할 수 있는 메커니즘을 갖추고 있습니다.
- 내비게이션: AGV의 일반적인 내비게이션 방식(마그네틱 테이프, 레이저, 비전 등)을 사용하며, 특히 정확한 위치 정밀도가 중요합니다.
- 인식 시스템: 팔레트와 랙의 정확한 위치를 인식하기 위한 비전 시스템, 레이저 센서, 3D 센서 등을 활용합니다.
- 안전 시스템: 무거운 화물을 다루는 특성상 강화된 안전 기능(하중 감지, 장애물 감지, 경고 시스템 등)을 갖추고 있습니다.
지게차형 AGV의 주요 유형
- 카운터밸런스형: 후방에 무거운 카운터웨이트를 배치하여 균형을 유지하는 전통적인 지게차 디자인
- 리치트럭형: 마스트가 전후로 이동 가능하여 좁은 통로에서도 효율적으로 작동 가능
- VNA(Very Narrow Aisle)형: 매우 좁은 통로에서 작동할 수 있도록 설계된 특수 유형
- 스태커형: 단순화된 디자인으로 비교적 가벼운 팔레트 취급에 적합한 유형
- 하이브리드형: 지게차 기능과 다른 AGV 특성(예: 컨베이어 통합)을 결합한 유형
핵심 기술 요소
- 3D 비전 시스템: 팔레트와 랙의 정확한 위치를 인식하고 정밀한 포크 조작 가능
- 하중 감지 및 관리: 다양한 무게의 화물을 안전하게 처리하기 위한 시스템
- 정밀 제어: 마스트, 포크, 주행 부분의 정밀한 제어를 위한 고급 알고리즘
- 안정성 제어: 높은 위치에서 작업 시 안정성을 유지하기 위한 안전 시스템
- 랙 매핑: 창고 랙 시스템의 정확한 3D 매핑과 위치 데이터베이스 구축
지게차형 AGV의 장단점
장점
- 수직 공간 활용: 높은 랙까지 접근 가능하여 창고 공간을 효율적으로 활용
- 기존 인프라 호환성: 표준 팔레트 및 기존 창고 랙 시스템과 호환
- 높은 적재 용량: 대부분 1-3톤 이상의 화물을 처리할 수 있는 능력
- 유연한 작업: 다양한 높이와 위치에서 팔레트 취급 가능
- 점진적 자동화: 기존 수동 지게차와 함께 운영 가능하여 단계적 도입 용이
단점
- 높은 초기 비용: 복잡한 리프팅 메커니즘으로 인한 고비용
- 기술적 복잡성: 3D 공간에서의 정확한 위치 파악과 제어의 어려움
- 공간 요구사항: 안전 운영을 위한 충분한 통로 폭 필요
- 특수 인프라: 일부 모델은 특수한 통로 설계나 랙 시스템 필요
- 유지보수 복잡성: 유압 시스템 등 복잡한 기계 요소의 유지보수 필요
주요 적용 분야
지게차형 AGV는 다음과 같은 환경에서 특히 효과적으로 활용됩니다:
- 대형 물류 창고: 입고, 출고, 보관 공정에서 팔레트 단위 물품의 고단 적재 및 이동
- 제조업 창고: 원자재 및 완제품의 효율적인 보관 및 운반
- 냉장/냉동 창고: 극한 환경에서 인력 대체를 통한 효율적 운영
- 유통 센터: 다양한 제품을 효율적으로 보관하고 픽킹하는 환경
- 항만 컨테이너 터미널: 표준화된 화물의 적재 및 이동
전통적 지게차형 AGV (1세대)
기본적인 자동화 기능을 갖추었으나 미리 정의된 고정 경로만 따라 이동 가능. 단순한 센서와 제한된 인식 능력으로 인해 특수 환경에서만 효과적으로 작동.
비전 강화 지게차형 AGV (2세대)
카메라와 비전 시스템을 통해 팔레트와 랙을 더 정확히 인식. 제한된 환경 적응력을 갖추었으나 여전히 구조화된 환경에서 최적의 성능 발휘.
지능형 지게차형 AGV (3세대)
인공지능과 고급 센서 기술을 통해 환경 변화에 적응 가능. 동적 경로 계획, 자동 장애물 회피, 그리고 복잡한 창고 환경에서의 자율 운영 능력 보유.
협업형 지게차 AGV (미래)
다른 AGV, 창고 관리 시스템, 로봇팔 등과 실시간 협업이 가능한 통합 시스템. 클라우드 기반 제어와 예측 분석을 통한 자원 최적화 기능.
지게차형 AGV 기술의 최신 발전 동향으로는 더 정확한 3D 비전 시스템과 깊이 센서를 통한 향상된 팔레트 인식 기술, 머신러닝을 활용한 적응형 적재 및 하역 알고리즘, 보다 에너지 효율적인 리프팅 시스템, 그리고 창고 관리 시스템(WMS)과의 더욱 긴밀한 통합을 통한 실시간 재고 관리 등이 있습니다.
이러한 발전으로 지게차형 AGV는 단순한 운반 장치를 넘어 지능형 창고 관리 시스템의 핵심 구성 요소로 진화하고 있으며, 특히 높은 수직 공간 활용도가 중요한 현대 물류 환경에서 그 중요성이 더욱 증가하고 있습니다.
협동형 AGV(콜라보레이티브 AGV)
협동형 AGV(콜라보레이티브 AGV)는 사람과 안전하게 같은 공간에서 작업할 수 있도록 설계된 고급 무인운반차입니다. 전통적인 AGV가 주로 사람이 없는 격리된 공간에서 작동하는 것과 달리, 협동형 AGV는 인간 작업자와 동일한 작업 공간을 공유하면서 효율적으로 협업할 수 있는 첨단 안전 기능과 지능형 상호작용 능력을 갖추고 있습니다.
협동형 AGV의 핵심 특성
협동형 AGV가 갖추어야 할 주요 특성은 다음과 같습니다:
- 고급 안전 시스템: 사람과 장애물을 정확히 감지하고 안전하게 대응할 수 있는 다층적 안전 시스템을 갖추고 있습니다.
- 적응형 속도 제어: 주변 환경과 인간의 존재에 따라 자동으로 속도를 조절하는 기능을 보유합니다.
- 직관적 인터페이스: 작업자가 쉽게 이해하고 상호작용할 수 있는 시각, 음성 또는 제스처 기반 인터페이스를 제공합니다.
- 학습 능력: 반복적인 작업을 통해 환경과 작업 패턴을 학습하고 적응하는 능력을 갖추고 있습니다.
- 유연한 작업 전환: 다양한 작업 간 쉽게 전환할 수 있고, 즉각적인 작업 변경에 대응 가능합니다.
- 예측 가능한 행동: 인간 작업자가 AGV의 다음 행동을 예측할 수 있도록 일관되고 명확한 동작 패턴을 유지합니다.
안전 기술
- 다계층 안전 센서: 레이저 스캐너, 3D 카메라, 초음파 센서 등 다양한 센서의 조합
- 안전 구역 설정: 속도에 따라 동적으로 조정되는 다중 안전 구역
- 비상 정지 시스템: 즉각적인 정지가 가능한 고급 제동 시스템
- 충돌 예측: 움직임을 예측하여 미리 충돌 가능성을 감지하는 알고리즘
- 압력 감지 범퍼: 접촉 시 즉시 감지하고 정지하는 물리적 안전 장치
인간-로봇 상호작용
- 직관적 상태 표시: 의도와 상태를 명확히 전달하는 조명, 디스플레이, 소리
- 음성 인식 및 명령: 음성으로 간단한 지시를 내릴 수 있는 기능
- 제스처 인식: 손동작이나 신체 동작을 인식하여 반응하는 기능
- 터치스크린 인터페이스: 직관적인 사용자 조작이 가능한 화면
- 작업자 식별: 개별 작업자를 인식하고 맞춤형 상호작용 제공
협동형 AGV의 작동 모드
협동형 AGV는 일반적으로 다음과 같은 여러 작동 모드를 지원합니다:
완전 자율 모드
AGV가 완전히 자율적으로 작업을 수행하며, 인간은 단지 감독 역할만 수행합니다. 예정된 작업을 자동으로 수행하면서 장애물을 회피하고 환경 변화에 적응합니다.
팔로잉 모드
작업자를 따라다니는 모드로, 피킹 작업이나 물품 수집 과정에서 작업자의 생산성을 높이는 데 유용합니다. 특정 거리를 유지하며 작업자를 자동으로 추적합니다.
수동 제어 모드
작업자가 리모컨, 조이스틱, 태블릿 등을 통해 AGV를 직접 제어하는 모드입니다. 복잡하거나 예외적인 상황에서 유용하게 활용됩니다.
티칭 모드
작업자가 AGV에 특정 경로나 작업을 직접 가르치는 모드로, 프로그래밍 없이도 새로운 작업을 쉽게 설정할 수 있습니다.
장점
- 공간 활용 극대화: 별도의 격리된 구역 없이 인간 작업 공간을 함께 사용
- 작업 유연성: 완전 자동화가 어려운 복잡한 작업에서도 효율적 지원
- 인간의 창의성과 로봇의 효율성 결합: 각각의 강점을 살린 협업
- 점진적 자동화: 일시에 완전 자동화 없이 단계적 전환 가능
- 낮은 인프라 요구사항: 특별한 안전 펜스나 분리 구조물 불필요
- 작업자 부담 감소: 반복적이거나 육체적으로 힘든 작업 대체
한계 및 과제
- 높은 기술적 복잡성: 고급 센서와 AI 알고리즘으로 인한 비용 상승
- 완벽한 안전 보장의 어려움: 인간 행동의 예측 불가능성 처리
- 법적, 규제적 문제: 인간-로봇 협업에 관한 안전 규정 준수
- 작업자 훈련 필요: 로봇과 효과적으로 협업하기 위한 교육 필요
- 심리적 저항: 로봇과 밀접하게 작업하는 것에 대한 작업자 불안감
- 속도 제한: 안전을 위해 인간 근처에서 속도 제한 필요
주요 적용 분야
협동형 AGV는 다음과 같은 환경에서 특히 효과적으로 활용됩니다:
- e-커머스 피킹 작업: 작업자를 따라다니며 수집한 물품을 담는 보조 역할
- 주문형 제조 환경: 자주 변경되는 작업과 유연한 생산 라인
- 병원 및 의료 시설: 의료진과 환자가 있는 환경에서의 안전한 물품 운반
- 소매업: 고객이 있는 매장 내에서의 재고 보충 및 물류 작업
- 연구 및 개발 시설: 다양한 실험 장비와 재료의 운반 및 관리
- 식품 가공 및 제약 산업: 깨끗한 환경에서의 정밀한 자재 취급
협동형 AGV 기술의 최신 발전 동향으로는 인공지능과 딥러닝을 활용한 더 자연스러운 인간 행동 예측 및 대응 능력, AR(증강현실)을 활용한 직관적인 작업자 인터페이스, 제스처 및 자연어 인식을 통한 더 자연스러운 명령 체계, 그리고 택타일(촉각) 피드백과 햅틱 기술을 통한 더 섬세한 상호작용 등이 있습니다.
협동형 AGV는 완전 자동화와 인간 작업의 중간 단계로, 각각의 장점을 활용하면서 단점을 보완하는 효율적인 솔루션입니다. 특히 다양성과 적응성이 요구되는 현대 산업 환경에서 점점 더 중요한 역할을 담당할 것으로 예상됩니다. 인간과 로봇의 협업을 통해 생산성 향상뿐 아니라 작업 환경의 질적 개선에도 기여할 수 있는 미래지향적 기술로 평가받고 있습니다.
특수목적 AGV(클린룸, 의료, 위험물)
특수목적 AGV는 일반 산업 환경을 넘어 클린룸, 의료 시설, 위험물 취급 구역 등 특수한 조건과 요구사항을 가진 환경에서 작동하도록 설계된 무인운반차입니다. 이러한 AGV는 일반 AGV의 기본 기능에 더해 특정 환경에 맞는 추가적인 기능과 안전 조치를 갖추고 있어, 고도로 규제된 산업이나 특수 환경에서도 자동화의 이점을 누릴 수 있게 합니다.
클린룸용 AGV
클린룸은 미립자, 미생물, 화학물질 등의 오염을 극도로 제한하는 환경으로, 반도체, 제약, 정밀 전자 제조 등의 산업에서 중요합니다. 클린룸용 AGV의 주요 특성은 다음과 같습니다:
설계 특징
- 오염 방지 재질: 입자 방출이 적은 특수 재질 사용(스테인레스 스틸, 특수 코팅 플라스틱 등)
- 밀폐형 구조: 내부 부품에서 발생하는 입자가 외부로 방출되지 않도록 설계
- HEPA 필터 통합: 배기 시스템에 고효율 입자 필터 장착
- 정전기 방지: 정전기 발생을 최소화하는 설계와 접지 시스템
- 충전 설계: 특수 무선 충전 방식으로 클린룸 내부에서 충전 가능
주요 적용 분야
- 반도체 제조: 웨이퍼 운반, 장비 간 자재 이동
- 디스플레이 생산: 유리 기판 및 패널 운반
- 제약 생산: 무균 의약품 및 원료 이동
- 바이오테크: 샘플 및 생물학적 물질 운반
- 정밀 광학: 렌즈 및 광학 부품 이동
의료용 AGV
병원, 진료소, 노인 돌봄 시설 등 의료 환경에서 사용되는 AGV는 위생, 안전, 조용한 작동이 중요합니다. 의료용 AGV의 주요 특성은 다음과 같습니다:
설계 특징
- 위생적 설계: 쉽게 세척 및 소독 가능한 표면과 구조
- 향균 재질: 박테리아 성장을 억제하는 특수 재질 사용
- 저소음 작동: 환자의 안정을 위한 정숙한 구동 시스템
- 자동문 연동: 병원 내 자동문 및 엘리베이터와 연동 가능
- UV 살균 기능: 일부 모델은 운반물 또는 이동 경로 살균 기능 보유
- 경보 및 대피 프로토콜: 응급 상황에서의 안전한 대응 방안
주요 적용 분야
- 검체 운반: 검사실과 병동 간의 검체 이동
- 약품 배송: 약국에서 병동으로의 약품 운반
- 린넨 및 세탁물: 깨끗한 린넨 배송 및 사용된 린넨 수거
- 식사 배달: 환자 식사 트레이 배송 및 수거
- 의료 폐기물: 안전한 의료 폐기물 수거 및 처리
- 의료 장비: 이동형 X-레이, 초음파 등 장비 이동
위험물 취급용 AGV
독성 물질, 방사성 물질, 가연성 물질 등 인체에 유해하거나 위험한 물질을 다루는 환경에서 사용되는 AGV입니다. 위험물 취급용 AGV의 주요 특성은 다음과 같습니다:
방폭 설계
폭발 위험이 있는 환경에서 사용되는 AGV는 스파크나 과열을 방지하는 방폭 설계(Ex-proof)를 갖추고 있습니다. 모든 전기 부품이 밀폐되어 있으며, 특수 방폭 인증을 받은 구성요소만 사용합니다.
방사선 차폐
방사성 물질 취급 환경에서는 전자 부품을 방사선으로부터 보호하기 위한 차폐 설계가 적용됩니다. 원격 모니터링과 제어 기능이 강화되어 최소한의 인간 개입만으로 작동 가능합니다.
화학물질 저항성
화학 산업에서 사용되는 AGV는 산, 알칼리, 용제 등에 내성이 있는 특수 재질과 코팅을 사용합니다. 유출 감지 센서와 밀폐형 컨테이너 시스템을 갖추고 있으며, 비상 상황에서의 안전 프로토콜이 내장되어 있습니다.
극한 온도 대응
초저온 또는 고온 환경에서 작동하는 AGV는 특수 단열 설계와 내열/내한성 재질을 사용합니다. 온도 변화에 민감한 부품을 보호하기 위한 능동형 온도 조절 시스템을 갖추고 있습니다.
주요 적용 분야
- 화학 공장: 독성/가연성 화학물질 운반
- 원자력 시설: 방사성 물질 및 폐기물 취급
- 제약 위험물: 세포독성 약물, 생물학적 위험물질 취급
- 군사 시설: 폭발물, 민감한 물질 운반
- 석유화학 산업: 가연성 액체 및 가스 관련 물품 운반
안전 인증과 규정 준수
특수목적 AGV는 해당 산업의 엄격한 규제와 인증 요건을 충족해야 합니다. 클린룸용 AGV는 ISO 클래스 인증, 의료용 AGV는 의료기기 관련 규정, 위험물 취급 AGV는 ATEX, IECEx 등의 방폭 인증을 취득해야 합니다.
고급 모니터링 및 기록
규제가 엄격한 환경에서는 작업 이력의 철저한 기록과 추적이 필요합니다. 특수목적 AGV는 모든 작동과 상태를 상세히 기록하고, 실시간 모니터링이 가능한 시스템을 갖추고 있으며, 감사 및 규정 준수 증명을 위한 보고서 생성 기능을 제공합니다.
특수 센서 기술
일반 환경을 넘어선 특수 조건 감지를 위한 센서를 장착합니다. 가스 감지기, 방사선 감지기, 온도/습도 센서, 압력 센서 등 환경 특성에 맞는 특수 센서가 통합되어 있으며, 센서 데이터 기반의 자동 대응 프로토콜이 구현되어 있습니다.
중복 안전 시스템
중요 시스템의 이중화를 통해 고신뢰성을 확보합니다. 주요 제어 시스템과 안전 장치의 백업 시스템 구현, 내결함성(fault-tolerant) 설계를 통한 부분 고장 시에도 안전 기능 유지, 그리고 정기적인 자가 진단 및 예방적 유지보수 기능을 갖추고 있습니다.
특수목적 AGV 분야의 최신 기술 동향으로는 AI 기반의 환경 적응 능력 향상, IoT 센서와 연동된 실시간 환경 모니터링 및 대응 시스템, 생체모방 설계를 통한 극한 환경 적응력 개선, 그리고 5G 통신을 활용한 원격 제어 및 모니터링 고도화 등이 있습니다.
이러한 특수목적 AGV는 인간이 직접 수행하기 위험하거나 어려운 환경에서의 작업 자동화를 가능하게 함으로써, 작업자 안전 향상, 오염 위험 감소, 일관된 품질 유지 등 다양한 이점을 제공합니다. 앞으로도 첨단 재료 과학, 센서 기술, 인공지능의 발전과 함께 더욱 정교하고 신뢰성 있는 특수목적 AGV가 개발될 것으로 전망됩니다.
대형 중량물 운반용 AGV
대형 중량물 운반용 AGV는 수십 톤에서 수백 톤에 이르는 초중량 화물을 운반하기 위해 특별히 설계된 무인운반차입니다. 이러한 AGV는 조선소, 중공업 공장, 풍력 터빈 제조 시설, 대형 항만 등에서 사용되며, 일반 AGV보다 월등히 큰 규모와 강력한 운반 능력을 갖추고 있습니다. 대형 산업 설비, 선박 블록, 대형 구조물 등 기존 운반 장치로는 처리하기 어려운 대형 화물의 이동 자동화에 중요한 역할을 합니다.
대형 중량물 운반용 AGV의 구조와 특징
대형 중량물 운반용 AGV의 기본 구성과 주요 특징은 다음과 같습니다:
- 견고한 프레임 구조: 초중량 화물을 안정적으로 지지할 수 있는 고강도 강철 프레임과 구조 설계
- 다축 구동 시스템: 다수의 구동 휠과 조향 시스템을 통한 정밀한 이동 제어
- 하중 분산 시스템: 화물의 무게를 여러 축에 고르게 분산시키는 기술
- 강력한 동력원: 디젤 엔진, 전기 모터, 또는 하이브리드 시스템의 고출력 동력 장치
- 정밀 유압 시스템: 대형 화물의 리프팅과 위치 조정을 위한 고급 유압 장치
- 특수 내비게이션: 무거운 하중 조건에서도 정확한 이동을 위한 강화된 내비게이션 시스템
대형 중량물 운반용 AGV의 주요 유형
- 모듈형 트랜스포터: 여러 개의 독립적인 모듈을 조합하여 초대형 화물을 운반하는 시스템
- 플랫폼형 AGV: 대형 평평한 플랫폼 형태로, 화물을 상부에 직접 적재하여 운반
- 선박 블록 운반기: 조선소에서 선박 블록을 운반하기 위한 특수 설계 AGV
- 러그 캐리어: 대형 컨테이너나 화물을 하부에서 지지하여 들어 올리는 방식의 AGV
- 중장비 운반기: 굴착기, 불도저 등 대형 장비 자체를 운반하는 AGV
주요 기술적 특성
- 고정밀 하중 측정: 화물의 무게와 무게중심을 정확히 측정하는 시스템
- 동적 안정성 제어: 이동 중 화물의 안정성을 유지하기 위한 첨단 제어 시스템
- 정밀 동기화 제어: 여러 AGV가 하나의 화물을 동시에 운반할 때 필요한 동기화 기술
- 지면 압력 관리: 지면에 가해지는 압력을 분산시켜 바닥 손상을 방지하는 기술
- 자동 수평 유지: 불규칙한 지형에서도 화물의 수평을 자동으로 유지하는 기능
대형 중량물 운반용 AGV의 장단점
장점
- 초중량 화물의 안전한 운반: 인력으로 처리하기 위험한 대형 화물의 안전한 이동
- 정밀한 위치 제어: 대형 화물도 밀리미터 단위의 정확한 위치에 배치 가능
- 작업 공간 최적화: 크레인보다 작업 공간을 효율적으로 활용 가능
- 인건비 절감: 다수의 작업자가 필요한 작업을 자동화하여 비용 절감
- 24시간 운영: 쉬지 않고 지속적인 작업 가능
- 작업자 안전 향상: 위험한 중량물 취급 작업에서 인적 요소 제거
단점
- 높은 초기 투자 비용: 특수 설계와 고급 기술로 인한 고비용
- 인프라 요구사항: 강화된 바닥, 넓은 작업 공간 등 특수 인프라 필요
- 에너지 소비: 대형 화물 운반에 따른 높은 에너지 소비량
- 복잡한 유지보수: 특수 부품과 기술이 필요한 유지보수 체계
- 제한된 유연성: 특정 작업에 최적화되어 다목적 활용이 제한적
- 운영 전문성: 고도의 기술적 지식이 필요한 운영 시스템
주요 적용 분야
대형 중량물 운반용 AGV는 다음과 같은 산업 분야에서 활발히 활용됩니다:
조선업
선박 블록 운반, 대형 엔진, 프로펠러 등 초중량 부품 이동에 사용됩니다. 특히 수백 톤에 이르는 선박 블록을 조립장에서 도크로 운반하는 과정에서 중요한 역할을 합니다.
중공업
대형 터빈, 발전 장비, 기계 설비 등 초대형 산업 장비의 공장 내 이동과 배치에 활용됩니다. 정밀한 위치 제어가 가능해 조립 라인에서 중요하게 사용됩니다.
풍력 발전 산업
대형 블레이드, 타워 섹션, 나셀 등 풍력 터빈 구성요소의 운반에 사용됩니다. 길이가 80미터 이상인 블레이드의 공장 내 이동과 배치에 필수적입니다.
항만 및 물류 터미널
초대형 컨테이너, 중장비, 특수 화물 등의 운반에 활용됩니다. 특히 RoRo(Roll-on/Roll-off) 작업이나 프로젝트 카고 처리에 유용합니다.
기술 발전 동향
대형 중량물 운반용 AGV 분야의 최신 기술 발전 동향은 다음과 같습니다:
- 스마트 연동 시스템: 여러 대의 AGV가 네트워크로 연결되어 하나의 대형 화물을 협업하여 운반하는 기술
- 친환경 동력원: 전기 구동 방식, 수소 연료전지 등 저탄소 친환경 동력 시스템 개발
- AI 기반 경로 최적화: 화물의 크기와 무게를 고려한 최적 경로 자동 계산 기술
- 디지털 트윈 통합: 실시간 3D 시뮬레이션을 통한 작업 계획 및 모니터링
- 첨단 서스펜션 시스템: 불규칙한 지형에서도 화물의 안정성을 유지하는 능동형 서스펜션
- 원격 조작 기능: 복잡한 상황에서 원격 조작으로 전환 가능한 하이브리드 제어 시스템
대형 중량물 운반용 AGV는 전통적인 크레인이나 포크리프트로는 처리하기 어려운 초대형 화물의 정밀하고 안전한 이동을 가능하게 함으로써, 대형 제조업의 생산성과 안전성을 크게 향상시키고 있습니다. 특히 조선, 중공업 등 한국의 주요 산업 분야에서 경쟁력 강화의 핵심 요소로 자리잡고 있으며, 지속적인 기술 발전을 통해 더욱 정교하고 효율적인 시스템으로 발전하고 있습니다.
미래에는 AI와 IoT 기술의 발전으로 더욱 자율적이고 지능화된 대형 중량물 운반 시스템이 등장할 것으로 예상되며, 특히 복수의 AGV가 마치 하나의 유기체처럼 협업하여 초대형 구조물을 정밀하게 운반하는 군집 지능형 시스템이 산업 현장의 새로운 표준이 될 것으로 전망됩니다.
초소형·소형 AGV
초소형·소형 AGV는 좁은 공간이나 특수 환경에서 경량 물품을 효율적으로 운반하기 위해 설계된 소형화된 무인운반차입니다. 일반 AGV보다 크기가 작고 민첩하며, 특히 제한된 공간이나 정밀한 작업이 필요한 환경에서 활용됩니다. 이러한 소형 AGV는 물류 센터의 좁은 통로, 사무실 환경, 소매점, 전자 제조 공정 등 다양한 분야에서 점차 그 활용도가 높아지고 있습니다.
초소형·소형 AGV의 정의와 분류
초소형·소형 AGV는 일반적으로 다음과 같이 분류할 수 있습니다:
초소형 AGV (마이크로 AGV)
- 크기: 일반적으로 30cm x 30cm 미만
- 적재 용량: 수백 그램~수 킬로그램
- 주요 특징: 극도로 작은 크기, 매우 민첩한 움직임, 특수 목적 설계
- 적용 분야: 전자 부품 조립, 실험실 자동화, 소형 부품 물류
소형 AGV
- 크기: 일반적으로 30cm x 30cm ~ 80cm x 80cm
- 적재 용량: 5kg~100kg
- 주요 특징: 컴팩트한 디자인, 좁은 공간 기동성, 다목적 활용
- 적용 분야: 전자상거래 피킹, 사무실 배송, 소매업, 소형 부품 물류
초소형·소형 AGV의 구조적 특징
크기가 작은 만큼 소형 AGV는 일반 AGV와는 다른 구조적 특징을 가지고 있습니다:
- 경량 프레임: 알루미늄, 고강도 플라스틱 등 가벼우면서도 견고한 소재 사용
- 소형 구동 시스템: 비록 작지만 정밀 제어가 가능한 소형 모터와 구동계
- 컴팩트한 배터리: 공간 제약에도 불구하고 충분한 작동 시간을 제공하는 고밀도 배터리
- 통합 센서 패키지: 작은 공간에 효율적으로 배치된 다양한 센서 시스템
- 모듈식 설계: 다양한 용도에 맞게 상부 모듈을 교체할 수 있는 유연한 구조
- 특수 이동 메커니즘: 좁은 공간에서의 기동성을 높이기 위한 전방향 휠, 메카넘 휠 등 활용
장점
- 뛰어난 공간 효율성: 좁은 공간이나 밀집된 환경에서도 작동 가능
- 저렴한 도입 비용: 일반 AGV보다 상대적으로 낮은 투자 비용
- 유연한 배치: 필요에 따라 쉽게 재배치하고 확장 가능
- 낮은 에너지 소비: 작은 크기로 인한 효율적 에너지 사용
- 안전성: 낮은 무게와 속도로 인한 충돌 위험 감소
- 다목적성: 다양한 작업에 맞게 쉽게 적응 가능
한계 및 과제
- 제한된 적재 용량: 무거운 화물 운반에는 부적합
- 짧은 배터리 수명: 공간 제약으로 인한 배터리 용량 제한
- 제한된 센서 범위: 소형화로 인한 센서 성능 제한
- 외부 요인에 취약: 바닥 장애물이나 기울어진 표면에 민감
- 통신 안정성 확보: 작은 안테나와 전력으로 인한 통신 과제
- 운영 관리 복잡성: 다수의 소형 로봇 조율 필요
주요 적용 분야
초소형·소형 AGV가 특히 효과적으로 활용되는 분야는 다음과 같습니다:
전자 제조
스마트폰, 컴퓨터, 반도체 등 전자 제품 제조 현장에서 소형 부품 운반, PCB 이송, 조립 라인 간 연결 작업 등에 활용됩니다. 클린룸 환경에 적합한 특수 설계 모델도 있습니다.
소매업 및 창고
전자상거래 및 소매업 물류 센터에서 소형 제품 피킹, 포장 구역으로의 운반, 재고 보충 등에 활용됩니다. 특히 좁은 통로가 많은 환경에서 효과적입니다.
사무실 및 서비스 환경
기업 사무실, 병원, 호텔 등에서 문서, 소포, 사무용품, 의약품 등의 배송 작업에 활용됩니다. 사람이 많은 환경에서 안전하게 작동할 수 있는 설계가 중요합니다.
연구소 및 실험실
자동화된 실험실에서 샘플, 시약, 실험 장비 등의 운반 작업에 활용됩니다. 정밀한 위치 제어와 안정적인 이동이 중요합니다.
초소형·소형 AGV의 기술적 특징
전방향 이동 시스템
메카넘 휠, 옴니 휠 등 특수 휠 시스템을 통해 좁은 공간에서도 모든 방향으로 자유롭게 이동 가능
효율적 에너지 관리
제한된 배터리 용량을 최대한 활용하기 위한 저전력 설계와 지능형 전력 관리 시스템
군집 지능
다수의 소형 AGV가 협업하여 더 큰 작업을 효율적으로 수행하는 협업 알고리즘
소형화된 센서 기술
작은 크기에도 불구하고 정확한 환경 인식을 위한 미니어처 센서와 통합 시스템
초소형·소형 AGV 기술의 최신 발전 동향으로는 인공지능을 활용한 더 스마트한 환경 인식 및 의사결정 능력, 소형 드론과의 협업을 통한 3D 물류 시스템 구현, 에너지 하베스팅 기술과 초고밀도 배터리를 통한 작동 시간 연장, 그리고 집단 지능 알고리즘을 통한 대규모 로봇 군집의 효율적 운영 등이 있습니다.
소형 AGV는 특히 산업 현장의 미세 자동화(micro-automation)와 분산 물류(distributed logistics) 트렌드에 부합하여, 대형 중앙집중식 시스템보다 유연하고 민첩한 자동화 솔루션을 제공합니다. 특히 전자상거래의 빠른 주문 처리 요구와 개인화된 제조 트렌드에 대응하기 위한 유연한 물류 시스템의 핵심 구성 요소로 자리잡고 있습니다.
미래에는 더욱 소형화되고 지능화된 AGV가 개발되어, 단순한 운반 기능을 넘어 환경 모니터링, 재고 관리, 품질 검사 등 다양한 부가 기능을 수행하는 종합적인 자동화 플랫폼으로 발전할 것으로 전망됩니다.
AGV의 기본 하드웨어 구성요소
무인운반차(AGV)는 다양한 하드웨어 구성요소들이 유기적으로 결합하여 작동합니다. 이러한 구성요소들은 AGV의 용도와 유형에 따라 차이가 있지만, 기본적인 하드웨어 구성요소들은 대부분의 AGV에 공통적으로 포함되어 있습니다. 이 구성요소들의 품질과 성능은 AGV의 전반적인 성능, 신뢰성 및 수명에 직접적인 영향을 미칩니다.
프레임 및 섀시
- 기본 구조: AGV의 모든 구성요소를 지지하는 기본 뼈대로, 강철, 알루미늄 또는 복합 소재로 제작
- 설계 고려사항: 예상 적재 하중, 내구성, 무게 중심, 모듈식 확장 가능성
- 특수 요구사항: 방수, 방진, 방폭, 클린룸 호환성 등 작업 환경에 따른 특수 처리
구동 시스템
- 모터: DC 모터, BLDC(브러시리스 DC) 모터, 서보 모터 등 정밀 제어가 가능한 전기 모터
- 구동륜: 트랙션 휠, 캐스터, 메카넘 휠, 옴니 휠 등 이동 방식에 따른 다양한 휠 시스템
- 변속/감속 장치: 토크와 속도를 조절하기 위한 기어 시스템
- 조향 메커니즘: 차동 조향, 아크만 조향, 전방향 조향 등 다양한 방식
전원 공급 시스템
- 배터리: 납산, 리튬이온, LFP(리튬인산철), 니켈 기반 배터리 등 다양한 유형
- 충전 시스템: 접촉식, 무선 충전, 배터리 교체 방식 등
- 전력 관리: 배터리 상태 모니터링, 전력 효율 최적화, 과방전/과충전 방지
- 대체 전원: 수소 연료전지, 하이브리드 시스템 등 특수 목적의 전원 시스템
적재 메커니즘
- 포크: 팔레트 운반을 위한 포크 시스템(지게차형 AGV)
- 리프팅 테이블: 상하 이동이 가능한 적재 플랫폼
- 컨베이어: 자동 적재/하역을 위한 롤러 또는 벨트 컨베이어
- 특수 그리퍼: 특정 형태의 물품을 취급하기 위한 전용 장치
- 회전 테이블: 물품의 방향을 조절할 수 있는 회전 장치
제어 및 통신 하드웨어
메인 컨트롤러
AGV의 두뇌 역할을 하는 중앙 처리 장치로, 일반적으로 산업용 PC, PLC(Programmable Logic Controller) 또는 전용 마이크로컨트롤러로 구성됩니다. 센서 데이터 처리, 경로 계획, 모터 제어, 작업 관리 등 AGV의 모든 기능을 조율합니다.
모터 컨트롤러
구동 모터와 조향 모터를 정밀하게 제어하는 전용 하드웨어로, PWM(Pulse Width Modulation) 신호 생성, 전류 제한, 회생 제동, 과열 방지 등의 기능을 수행합니다. 정확한 속도와 위치 제어를 위해 엔코더 피드백을 처리합니다.
통신 모듈
중앙 관제 시스템, 다른 AGV, 주변 장치와의 데이터 교환을 위한 하드웨어로, Wi-Fi, Bluetooth, 5G, 전용 RF 통신 등 다양한 무선 통신 기술을 사용합니다. 안정적인 데이터 송수신을 위한 안테나 시스템도 포함됩니다.
사용자 인터페이스
작업자와의 상호작용을 위한 하드웨어로, 상태 표시등, 디스플레이 패널, 터치스크린, 비상 정지 버튼, 제어 스위치 등으로 구성됩니다. 일부 고급 모델은 음성 인식이나 제스처 인식 하드웨어도 포함하고 있습니다.
센서 시스템
AGV의 '눈과 귀' 역할을 하는 센서 시스템은 다음과 같은 주요 구성요소를 포함합니다:
- 내비게이션 센서: 마그네틱 센서, 바코드/QR 스캐너, 레이저 스캐너, 카메라 등
- 위치 및 운동 센서: 엔코더, IMU(관성 측정 장치), 자이로스코프, 가속도계
- 장애물 감지 센서: 초음파 센서, ToF(Time of Flight) 센서, 범퍼 센서, 라이다
- 환경 감지 센서: 온도, 습도, 가스, 먼지, 소음 등 환경 조건 측정
- 안전 센서: 레이저 안전 스캐너, 압력 감지 매트, 비전 기반 인체 감지
- 상태 모니터링 센서: 배터리 상태, 모터 온도, 진동, 하중 센서 등
추가 하드웨어 구성요소
냉각 시스템
고성능 AGV에서는 전자 장비와 모터의 열 관리를 위한 냉각 시스템이 중요합니다. 패시브 쿨링(히트싱크, 방열판), 액티브 쿨링(팬, 액체 냉각), 그리고 온도 센서와 제어 회로로 구성됩니다. 특히 연속 작동 환경이나 고온 작업 환경에서 중요한 요소입니다.
보조 시스템
AGV의 보조 기능을 위한 추가 하드웨어로, 바코드 프린터, RFID 태그 부착기, 포장재 디스펜서, 경로 마커 설치 장치 등이 포함될 수 있습니다. 또한 자체 진단 및 원격 유지보수를 위한 하드웨어 인터페이스도 중요한 구성요소입니다.
하드웨어 구성요소 선택 시 고려해야 할 핵심 요소로는 신뢰성과 내구성, 정밀도와 성능, 유지보수 용이성, 에너지 효율성, 확장성과 호환성, 그리고 비용 효율성이 있습니다. 특히 산업 환경에서는 가혹한 조건(진동, 먼지, 온도 변화 등)에 내성이 있는 산업용 등급의 하드웨어 선택이 중요합니다.
최근 하드웨어 기술 발전 동향으로는 모듈식 설계를 통한 쉬운 업그레이드와 유지보수, IoT 기능이 통합된 스마트 컴포넌트, 에너지 효율이 높은 모터와 배터리 기술, 그리고 소형화와 경량화를 통한 공간 효율성 개선 등이 있습니다. 특히 리튬이온 배터리 기술의 발전, 고효율 BLDC 모터의 보편화, 그리고 더 작고 강력한 프로세싱 유닛의 등장으로 AGV의 성능과 효율성이 크게 향상되고 있습니다.
적절한 하드웨어 구성요소의 선택과 통합은 AGV 시스템의 성공적인 구현과 운영에 결정적인 영향을 미칩니다. 특히 사용 환경과 용도에 최적화된 하드웨어 구성은 AGV의 성능뿐 아니라 총소유비용(TCO)과 투자수익률(ROI)에도 직접적인 영향을 미치므로 신중한 계획과 선택이 필요합니다.
AGV 내 센서 종류와 역할
AGV(무인운반차)는 주변 환경을 인식하고 안전하게 이동하기 위해 다양한 센서를 활용합니다. 이러한 센서들은 AGV의 '감각 기관' 역할을 하며, 위치 파악, 장애물 감지, 안전 확보, 작업 수행 등 다양한 기능을 지원합니다. AGV 시스템의 성능과 신뢰성은 센서의 정확도와 적절한 통합에 크게 의존하므로, 다양한 센서를 이해하고 최적의 조합을 구성하는 것이 중요합니다.
내비게이션 및 위치 인식 센서
AGV가 환경 내에서 자신의 위치를 파악하고 목적지까지 이동하기 위한 센서들입니다:
마그네틱 센서
바닥에 부착된 마그네틱 테이프나 스폿에서 발생하는 자기장을 감지하는 센서입니다. 경로 추적이나 위치 표시에 사용되며, 간단한 구조와 높은 신뢰성이 특징이지만 고정된 경로만 따를 수 있는 제한이 있습니다.
바코드/QR 스캐너
바닥이나 벽에 부착된 바코드 또는 QR코드를 읽어 위치 정보와 작업 지시를 받는 센서입니다. 추가 정보 저장이 가능하고 설치가 간편하지만, 코드가 손상되거나 오염되면 인식이 어려울 수 있습니다.
레이저 스캐너/라이다(LiDAR)
레이저 빔을 발사하고 반사된 빔을 측정하여 거리와 각도를 계산하는 센서입니다. 정밀한 위치 측정과 지도 작성(매핑)에 사용되며, 높은 정확도와 넓은 감지 범위가 특징이지만 가격이 높고 먼지가 많은 환경에서 성능이 저하될 수 있습니다.
비전 시스템(카메라)
2D 또는 3D 카메라를 통해 환경을 시각적으로 인식하는 센서입니다. 풍부한 정보 수집이 가능하고 자연 특징 인식에 유용하지만, 조명 조건에 민감하고 이미지 처리에 높은 연산 능력이 필요합니다.
운동 및 자세 감지 센서
AGV의 움직임, 속도, 각도 등을 측정하는 센서들입니다:
휠 엔코더
- 기능: 휠의 회전 수와 방향을 측정하여 이동 거리와 속도 계산
- 장점: 높은 정밀도, 간단한 구조, 신뢰성 높음
- 한계: 휠 슬립이 발생하면 오차 누적, 절대 위치 파악 불가
IMU(관성 측정 장치)
- 기능: 가속도계, 자이로스코프, 때로는 지자기계를 포함한 복합 센서
- 장점: 자세(roll, pitch, yaw) 측정, 외부 참조 없이 작동
- 한계: 시간에 따른 드리프트(오차 누적) 발생
자이로스코프
- 기능: 회전 속도와 각도 변화 측정
- 장점: 높은 반응성, 정밀한 회전 감지
- 한계: 장기간 사용 시 오차 누적
가속도계
- 기능: 선형 가속도 측정, 충격 감지
- 장점: 움직임 시작/정지 감지, 진동 모니터링
- 한계: 노이즈에 민감, 중력 영향 받음
안전 및 장애물 감지 센서
AGV의 안전한 작동과 충돌 방지를 위한 센서들입니다:
2D 안전 레이저 스캐너
AGV의 가장 중요한 안전 센서 중 하나로, 일정 높이에서 360도 또는 특정 각도 범위를 스캔하여 장애물을 감지합니다. 안전 인증을 받은 스캐너는 여러 안전 구역(경고 구역, 감속 구역, 정지 구역)을 설정할 수 있으며, 인체나 장애물 감지 시 즉각적인 정지 신호를 발생시킵니다. 정확도가 높고 신뢰성이 우수하지만 가격이 비싸고 단일 평면만 감지하는 한계가 있습니다.
3D 감지 센서
여러 평면 또는 3D 공간에서 장애물을 감지하는 센서로, 3D 라이다, ToF(Time of Flight) 카메라, 스테레오 비전 카메라 등이 포함됩니다. 상부 돌출 장애물, 계단, 경사로 등 2D 스캐너가 감지하지 못하는 장애물을 파악할 수 있습니다. 또한 물체의 크기와 형태를 인식할 수 있어 더 지능적인 대응이 가능하지만, 데이터 처리에 높은 연산 능력이 필요하고 가격이 높은 편입니다.
- 초음파 센서: 음파를 발사하고 반사된 신호로 거리를 측정하는 센서로, 비용이 저렴하고 투명 물체도 감지 가능하지만 정확도가 상대적으로 낮고 반사 특성에 영향 받음
- 범퍼 센서: 물리적 접촉 시 작동하는 가장 기본적인 안전 장치로, 마지막 방어선 역할을 하며 충돌 시 즉각 정지
- 압력 감지 매트: AGV 주변에 설치하여 무게를 감지하는 센서로, 특히 큰 AGV의 측면이나 후방 안전을 위해 사용
- 정전용량식 센서: 전기장 변화를 감지하여 인체나 금속 물체 접근 시 반응하는 센서
작업 및 상태 모니터링 센서
AGV의 작업 수행과 상태 점검을 위한 센서들입니다:
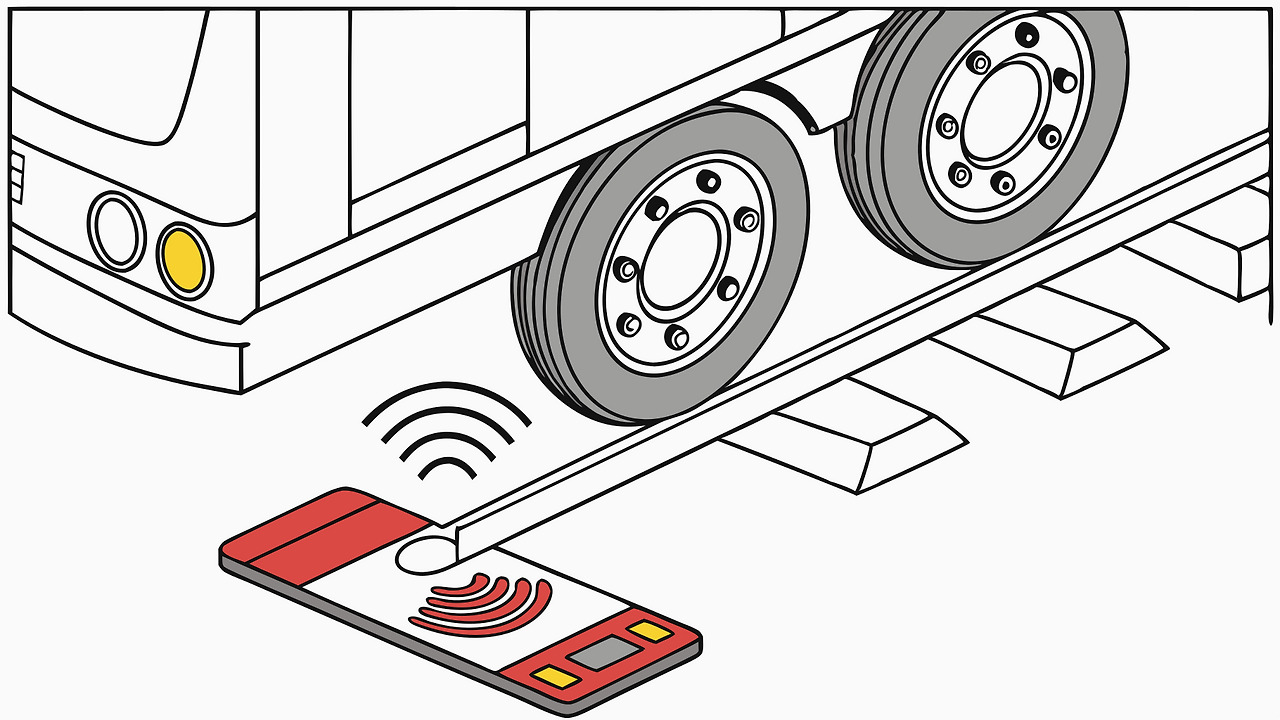
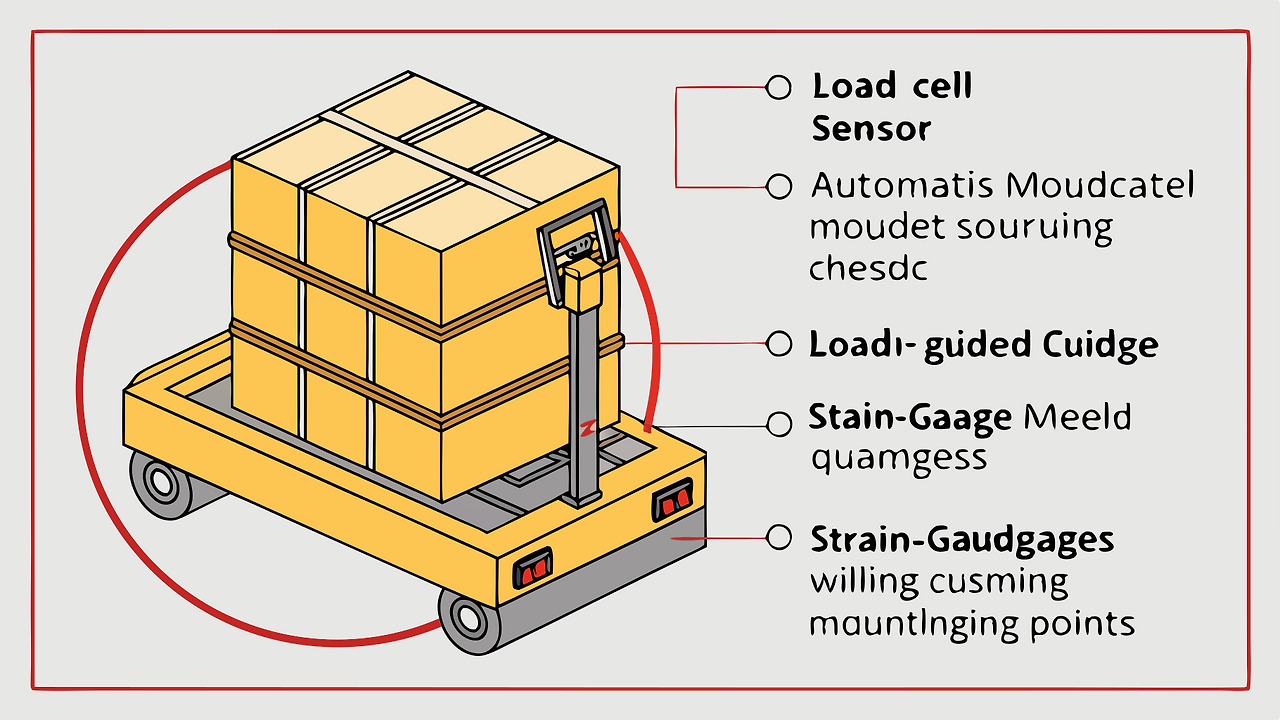
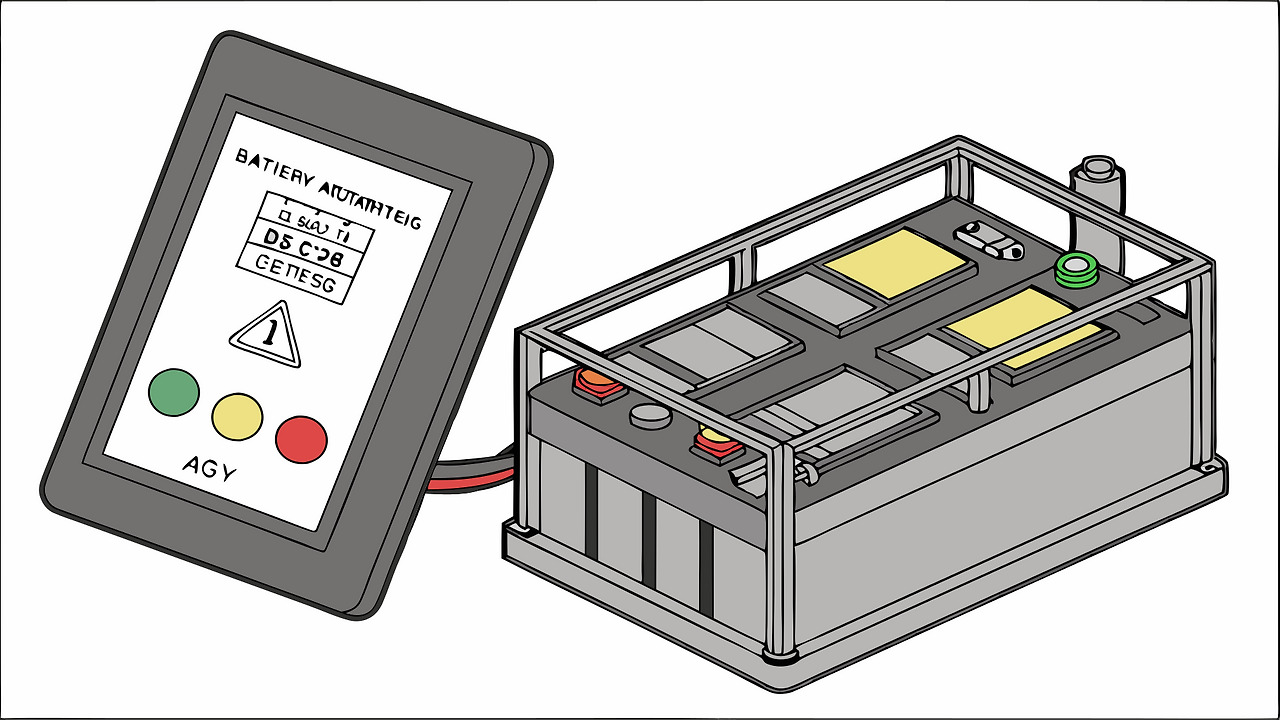
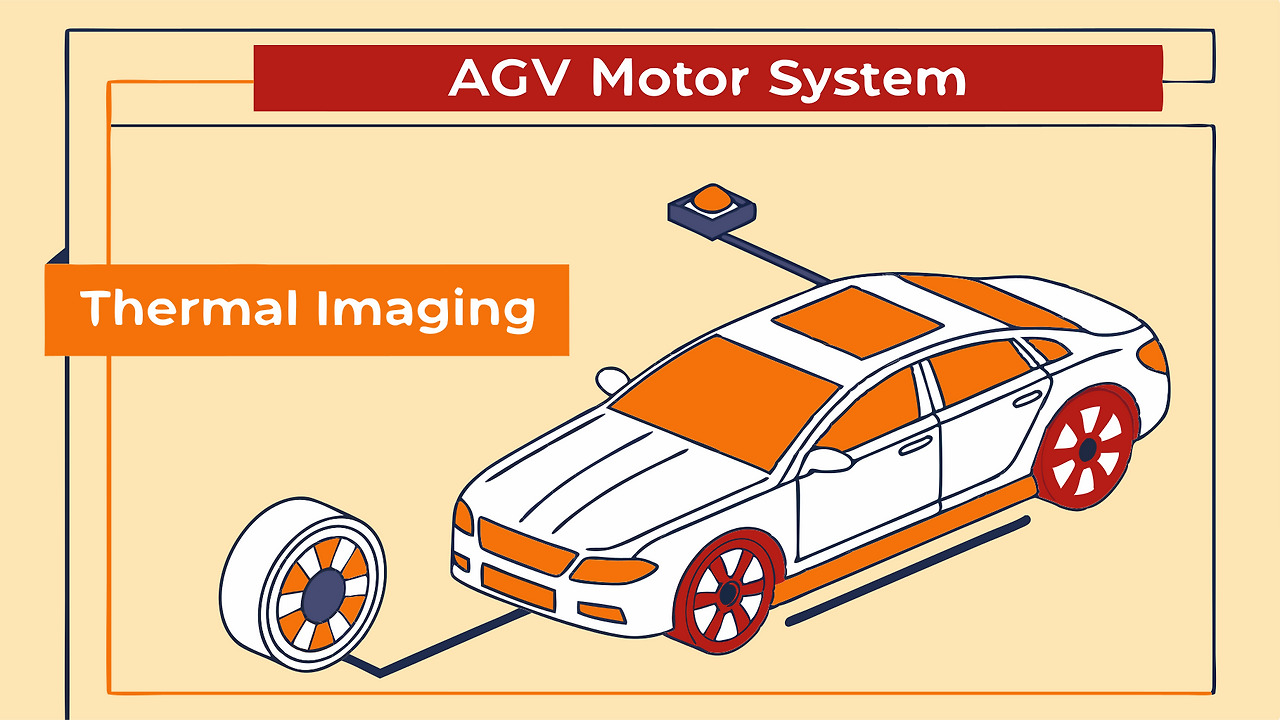
- RFID 리더: 물품, 위치, 작업 지시 등에 부착된 RFID 태그를 읽어 정보를 수집
- 하중 센서: 적재된 화물의 무게를 측정하여 과부하 방지 및 최적 속도/가속도 결정
- 배터리 관리 시스템(BMS): 배터리 전압, 전류, 온도, 충전 상태를 모니터링
- 온도 센서: 모터, 전자장치, 배터리 등의 온도를 측정하여 과열 방지
- 습도/먼지 센서: 특수 환경(클린룸, 습도 민감 지역)에서 작동하는 AGV에 활용
- 진동 센서: 비정상적인 진동을 감지하여 장비 고장이나 바닥 상태 불량 파악
센서 통합과 융합
대부분의 AGV는 단일 센서에 의존하지 않고 여러 센서의 데이터를 결합하여 사용합니다. 이를 센서 퓨전(Sensor Fusion)이라고 하며, 각 센서의 장점을 활용하고 단점을 보완하는 접근 방식입니다.
예를 들어, 내비게이션에서는 라이다의 정확한 위치 측정과 IMU의 실시간 자세 정보, 그리고 휠 엔코더의 거리 정보를 결합하여 더 정확하고 안정적인 위치 정보를 얻을 수 있습니다. 또한 안전 시스템에서는 레이저 스캐너, 3D 카메라, 초음파 센서 등 여러 센서를 동시에 활용하여 다양한 유형의 장애물을 감지하고 안전성을 극대화합니다.
센서 기술의 최신 발전 동향으로는 더 작고 경제적인 3D 라이다 개발, AI 기반 카메라 인식 기술의 발전, 엣지 컴퓨팅을 통한 센서 데이터 실시간 처리 능력 향상, 그리고 여러 AGV 간 센서 데이터 공유를 통한 협업적 인식 능력 강화 등이 있습니다. 특히 5G 네트워크와 클라우드 시스템의 발전으로 AGV의 현장 데이터를 실시간으로 중앙 시스템에 전송하고 분석하는 기능이 강화되고 있습니다.
AGV 제어 소프트웨어 개요
AGV 제어 소프트웨어는 무인운반차의 두뇌 역할을 하는 핵심 요소로, 내비게이션, 작업 관리, 교통 제어, 안전 기능 등 AGV의 모든 작동을 조율합니다. 이 소프트웨어는 개별 AGV의 제어부터 전체 AGV 시스템의 통합 관리까지 다양한 수준에서 작동하며, 하드웨어 구성요소들이 효율적으로 협업할 수 있도록 지원합니다. 고급 AGV 시스템일수록 소프트웨어의 역할과 중요성이 더욱 커지며, 시스템의 확장성과 유연성을 결정짓는 핵심 요소가 됩니다.
AGV 제어 소프트웨어의 계층 구조
AGV 제어 소프트웨어는 일반적으로 다음과 같은 계층 구조로 구성됩니다:
엔터프라이즈 통합 계층
ERP, WMS, MES 등 기업 시스템과 연동
중앙 관제 시스템(FMS)
다수 AGV의 조율 및 전체 시스템 최적화
AGV 제어 시스템
개별 AGV의 내비게이션, 작업 수행, 안전 관리
하드웨어 제어 계층
모터, 센서, 액추에이터 등 직접적인 하드웨어 제어
주요 소프트웨어 구성요소 및 기능
내비게이션 및 경로 계획
- 맵핑 소프트웨어: 작업 환경의 디지털 지도 생성 및 관리
- 위치 추정 알고리즘: 센서 데이터를 기반으로 AGV의 정확한 위치 파악
- 경로 계획 알고리즘: 시작점에서 목적지까지의 최적 경로 계산
- 장애물 회피 시스템: 동적 장애물 감지 및 대응 경로 재계획
- SLAM(Simultaneous Localization and Mapping): 미지 환경에서의 지도 작성과 위치 파악
작업 관리 및 스케줄링
- 작업 할당 알고리즘: 여러 AGV 간 최적 작업 분배
- 우선순위 관리: 작업의 중요도와 긴급성에 따른 처리 순서 결정
- 작업 모니터링: 실시간 작업 진행 상황 추적 및 보고
- 예측적 스케줄링: 과거 패턴 분석을 통한 미래 작업 예측 및 준비
- 충전 및 유지보수 관리: 배터리 상태 모니터링 및 충전 스케줄 관리
교통 및 충돌 관리
- 교통 관제 시스템: 다수 AGV의 이동 조율 및 충돌 방지
- 교차로 관리: 공유 경로 및 교차점에서의 통행 우선순위 결정
- 정체 해소 알고리즘: 병목 구간 파악 및 대체 경로 제안
- 속도 프로파일 관리: 구간별 최적 속도 및 가속도 프로필 계산
- 동적 영역 할당: 여러 AGV의 작업 영역을 효율적으로 분배
안전 시스템
- 안전 구역 설정: 속도에 따른 다중 안전 구역 동적 관리
- 비상 정지 로직: 위험 상황 감지 시 즉각적인 대응
- 오류 감지 및 진단: 시스템 이상 징후 모니터링 및 경고
- 안전 프로토콜: 다양한 예외 상황에 대한 대응 절차
- 로그 기록: 안전 관련 이벤트의 상세 기록 및 분석
사용자 인터페이스 및 시각화
AGV 제어 소프트웨어는 운영자와의 효과적인 상호작용을 위해 다양한 인터페이스를 제공합니다:
운영 대시보드
전체 AGV 시스템의 상태와 성능을 한눈에 파악할 수 있는 시각적 대시보드를 제공합니다. 실시간 위치 표시, 배터리 상태, 작업 진행 상황, 주요 성능 지표 등을 직관적인 그래픽으로 표현합니다.
지도 기반 모니터링
작업 환경의 지도 위에 AGV의 실시간 위치와 이동 경로를 표시합니다. 교통 상황, 정체 구역, 작업 구역 등을 색상 코드와 아이콘으로 시각화하여 운영자의 상황 인식을 지원합니다.
알림 및 경고 시스템
이상 상황, 작업 완료, 배터리 부족 등 다양한 이벤트에 대한 알림을 제공합니다. 중요도에 따라 다양한 채널(화면 알림, 이메일, SMS, 모바일 앱 푸시 등)을 통해 통지합니다.
보고서 및 분석 도구
시스템 성능, 작업 효율성, 안전 기록 등에 대한 종합적인 보고서를 생성합니다. 데이터 시각화 도구를 통해 운영 추세 분석, 병목 현상 파악, 성능 개선 기회 식별을 지원합니다.
시스템 통합 및 API
현대의 AGV 제어 소프트웨어는 다른 기업 시스템과의 원활한 통합을 위한 다양한 인터페이스를 제공합니다:
- WMS(창고 관리 시스템) 연동: 재고 위치, 피킹 작업, 입출고 정보 등 교환
- MES(제조 실행 시스템) 통합: 생산 계획, 자재 요청, 공정간 이동 등 조율
- ERP(전사적 자원 관리) 연결: 주문 정보, 자원 할당, 비용 추적 등 연동
- IoT 플랫폼 통합: 다양한 센서, 장비, 시스템과의 실시간 데이터 교환
- API(Application Programming Interface): 표준화된 방식으로 외부 시스템과 통신
- SDK(Software Development Kit): 고객 맞춤형 기능 개발을 위한 도구 제공
최신 소프트웨어 기술 동향
인공지능 및 기계학습
패턴 인식을 통한 최적 경로 학습, 예측적 유지보수, 교통 흐름 최적화, 환경 변화 적응 등에 AI 기술 활용. 특히 딥러닝 기반 비전 시스템을 통한 복잡한 환경 인식 능력 향상.
클라우드 및 엣지 컴퓨팅
중앙 서버와 로컬 처리의 장점을 결합한 하이브리드 아키텍처 확산. 실시간 처리가 필요한 내비게이션은 AGV 내부에서, 빅데이터 분석과 최적화는 클라우드에서 처리하는 방식.
디지털 트윈
물리적 AGV 시스템의 가상 복제본을 만들어 실시간 모니터링, 시뮬레이션, 최적화에 활용. 새로운 레이아웃이나 작업 방식을 실제 적용 전에 가상 환경에서 테스트 가능.
군집 지능 알고리즘
중앙 제어 없이도 여러 AGV가 자율적으로 협업하는 분산형 알고리즘 개발. 자연계 집단 행동에서 영감을 받은 자가 조직화 시스템으로 확장성과 유연성 향상.
AGV 제어 소프트웨어는 하드웨어 플랫폼 못지않게 중요한 경쟁력 요소로, 꾸준한 업데이트와 기능 향상을 통해 시스템의 성능과 가치를 높여갑니다. 특히 오픈 소스 플랫폼과 모듈식 아키텍처의 발전으로 맞춤형 기능 개발과 확장이 용이해지고 있으며, 사용자 경험(UX) 중심의 설계로 복잡한 시스템도 직관적으로 운영할 수 있게 발전하고 있습니다.
미래의 AGV 제어 소프트웨어는 더욱 자율적이고 적응력 있는 시스템으로 진화할 것으로 예상됩니다. 특히 인공지능과 예측 분석을 통해 환경 변화와 작업 패턴에 자동으로 적응하고, 예외 상황에 더 지능적으로 대응하는 능력이 강화될 것입니다. 또한 증강현실(AR)과 가상현실(VR)을 활용한 직관적 인터페이스와 원격 관리 기능으로 운영의 편의성이 더욱 향상될 전망입니다.
AGV 교통 및 충돌관리 시스템
다수의 AGV가 동일한 공간에서 작동할 때 효율적인 이동 조율과 충돌 방지는 시스템의 성능과 안전성을 결정짓는 핵심 요소입니다. AGV 교통 및 충돌관리 시스템은 여러 AGV 간의 이동을 최적화하고, 병목 현상을 방지하며, 잠재적 충돌 상황을 사전에 감지하고 해결하는 복합적인 제어 시스템입니다. 이 시스템은 고도의 알고리즘과 실시간 통신을 기반으로 AGV들이 마치 교통 규칙을 준수하는 차량처럼 질서 있게 이동할 수 있도록 지원합니다.
교통 관리 시스템의 구성 요소
효과적인 AGV 교통 관리를 위한 주요 구성 요소들은 다음과 같습니다:
경로 네트워크 관리
- 가상 경로망: 작업 환경 내 AGV가 이동할 수 있는 허용된 경로 정의
- 노드 및 링크: 주요 지점(노드)과 이를 연결하는 경로(링크)로 구성된 네트워크
- 경로 속성: 방향성(일방통행/양방향), 속도 제한, 우선순위 등의 규칙 정의
- 특수 구역: 감속 구역, 대기 구역, 충전 구역 등 특별한 규칙이 적용되는 영역 관리
교통 제어 알고리즘
- 중앙집중식 제어: 중앙 시스템이 모든 AGV의 이동을 통합적으로 관리하는 방식
- 분산 제어: 각 AGV가 일정한 규칙에 따라 자율적으로 의사결정하는 방식
- 하이브리드 제어: 중앙 시스템과 개별 AGV의 판단을 조합하는 방식
- 우선순위 기반 제어: 작업 중요도, 배터리 상태 등에 따른 AGV 우선순위 관리
교차로 관리
- 구역 예약 시스템: AGV가 특정 교차로 구역을 미리 예약하여 독점적 사용권 획득
- 시간 슬롯 할당: 각 AGV에 교차로 통과 시간대를 할당하여 충돌 방지
- 신호등 방식: 가상 신호등 시스템을 통한 교통 흐름 제어
- 라운드로빈: 순환식 우선권 부여로 모든 AGV에 공정한 기회 제공
정체 관리
- 교통 밀도 모니터링: 구역별 AGV 밀집도 실시간 추적
- 대체 경로 제안: 정체 구간을 우회하는 대체 경로 계산
- 동적 속도 조정: 교통 상황에 따른 AGV 속도 자동 조절
- 대기 구역 활용: 전략적 위치에 대기 공간을 마련하여 일시적 정체 해소
충돌 방지 시스템
AGV 간 또는 AGV와 다른 물체 간의 충돌을 방지하기 위한 시스템은 여러 계층의 안전 메커니즘으로 구성됩니다:
계획 단계 충돌 방지
경로 계획 시점에서 이미 알려진 다른 AGV의 예상 경로와 충돌하지 않도록 사전에 조정하는 방식입니다. 시간-공간 경로 계획을 통해 동일 공간을 다른 시간에 사용하도록 계획합니다.
실시간 조정 단계
AGV 간 통신을 통해 실시간으로 위치와 의도를 공유하고 잠재적 충돌 상황을 감지하면 속도 조절, 일시 정지, 경로 재계산 등의 조치를 수행합니다.
센서 기반 충돌 방지
각 AGV의 센서(레이저 스캐너, 카메라, 초음파 등)를 통해 주변 환경을 감지하고 예상치 못한 장애물이나 다른 AGV를 감지하면 자동으로 감속 또는 정지합니다.
긴급 제동 시스템
모든 예방 조치가 실패할 경우 작동하는 최후의 안전장치로, 충돌 직전 상황에서 긴급 제동을 실행하여 충격을 최소화합니다.
교착 상태(Deadlock) 관리
교착 상태란 여러 AGV가 서로 진행을 막는 상황에서 아무도 이동할 수 없게 되는 상태를 말합니다. 이러한 교착 상태를 방지하고 해결하기 위한 방법으로는 다음과 같은 접근법이 있습니다:
교착 상태 예방
- 자원 할당 그래프: 경로와 교차점을 자원으로 간주하고 순환 의존성이 발생하지 않도록 관리
- 일방통행 설계: 가능한 경우 일방통행 경로를 설정하여 마주치는 상황 최소화
- 우선순위 규칙: 모든 AGV에 고유한 우선순위를 부여하여 의사결정 충돌 방지
- 시간 제한: 특정 구역 점유에 시간 제한을 두어 무한 대기 방지
교착 상태 감지 및 해결
- 감지 알고리즘: 정지 시간 모니터링, 기대 진행 상태 비교 등으로 교착 상태 감지
- 강제 우선순위 적용: 교착 상태 발생 시 특정 AGV에 우선 통행권 부여
- 임시 후진: 한 AGV가 잠시 뒤로 물러나 다른 AGV에 길 양보
- 중앙 개입: 교착 상태 감지 시 중앙 제어 시스템이 개입하여 모든 관련 AGV에 새 지시 하달
교통 최적화 전략
AGV 시스템의 전체 처리량과 효율성을 높이기 위한 다양한 교통 최적화 전략이 적용됩니다:
교통 흐름 밸런싱
작업 환경 내 모든 구역에 AGV가 균등하게 분포되도록 관리하여 특정 지역의 혼잡을 방지합니다. 실시간 교통 밀도 맵을 기반으로 새로운 작업을 할당하거나 경로를 조정합니다.
배터리 관리 통합
배터리 상태를 교통 관리에 통합하여 충전이 필요한 AGV에 우선적으로 충전소 접근 권한을 부여하거나, 배터리 잔량에 따라 작업 할당을 조정합니다.
예측적 경로 계획
과거 데이터와 패턴 분석을 통해 혼잡이 예상되는 시간과 구역을 미리 파악하고, 이를 고려한 선제적 경로 계획을 수립합니다. 특히 정기적인 패턴이 있는 작업 환경에서 효과적입니다.
구역 기반 제어
작업 환경을 여러 구역으로 나누고 각 구역에 최대 AGV 수를 제한하여 혼잡을 관리합니다. 한 구역이 최대 용량에 도달하면 추가 AGV의 진입을 일시적으로 제한합니다.
교통 관리 시스템의 유형
AGV 교통 관리 시스템은 크게 다음과 같은 유형으로 분류할 수 있습니다:
유형 | 특징 | 장점 | 단점 |
중앙집중식 | 단일 중앙 시스템이 모든 AGV의 이동을 제어 | 전체적 최적화 가능, 복잡한 조율 용이 | 단일 장애점 위험, 확장성 제한 |
분산식 | 각 AGV가 자율적으로 의사결정 | 견고성, 확장성, 실시간 대응력 | 전체적 최적화 어려움, 교착 상태 위험 |
하이브리드 | 중앙 조율과 로컬 자율성 결합 | 유연성, 견고성과 최적화 균형 | 시스템 복잡성 증가 |
구역 기반 | 작업 영역을 구역으로 나누고 각 구역 독립 관리 | 모듈성, 확장성, 관리 용이성 | 구역 경계에서 조율 필요 |
최신 기술 동향으로는 인공지능과 기계학습을 활용한 적응형 교통 관리 시스템의 발전이 두드러집니다. 이러한 시스템은 작업 패턴, 교통 흐름, AGV 성능 등의 데이터를 학습하여 더 효율적인 경로와 스케줄을 자동으로 생성합니다. 또한 디지털 트윈 기술을 활용하여 가상 환경에서 다양한 교통 시나리오를 시뮬레이션하고 최적의 전략을 도출하는 접근법도 증가하고 있습니다.
5G와 같은 고속 저지연 통신 기술의 발전으로 실시간 위치 데이터 공유와 즉각적인 명령 전송이 더욱 원활해지고 있으며, 엣지 컴퓨팅을 통해 AGV 자체의 의사결정 능력이 향상되어 하이브리드형 교통 관리가 더욱 효과적으로 이루어지고 있습니다. 더불어 군집 로봇공학(swarm robotics)에서 영감을 받은 자가 조직화 알고리즘의 도입으로 중앙 제어 없이도 효율적인 협업이 가능한 시스템이 연구되고 있습니다.
자동 충전 및 에너지관리 기술
AGV(무인운반차)의 연속적이고 효율적인 작동을 위해서는 효과적인 에너지 공급과 관리가 필수적입니다. 자동 충전 및 에너지관리 기술은 AGV가 인간의 개입 없이도 배터리 잔량을 모니터링하고, 필요 시 충전소로 이동하여 충전을 수행한 후 다시 작업을 재개할 수 있도록 하는 시스템입니다. 이러한 기술은 AGV 시스템의 가용성, 생산성, 그리고 전체 수명 주기 비용에 직접적인 영향을 미치며, 24시간 운영 환경에서 특히 중요한 역할을 합니다.
AGV 전원 공급 방식
AGV에 에너지를 공급하는 주요 방식들은 다음과 같습니다:
배터리 기반 시스템
- 납산 배터리: 전통적인 방식으로 비용이 저렴하지만 무겁고 충전 시간이 김
- 리튬이온 배터리: 높은 에너지 밀도, 빠른 충전, 긴 수명이 특징이나 비용이 높음
- LFP(리튬인산철) 배터리: 안전성이 뛰어나고 수명이 길지만 에너지 밀도가 낮음
- 니켈-금속수소 배터리: 중간 수준의 성능과 비용으로 특정 용도에 적합
연료전지 시스템
- 수소 연료전지: 수소와 산소의 화학 반응으로 전기 생성
- 장점: 긴 작동 시간, 빠른 연료 보충, 친환경적
- 단점: 인프라 구축 비용, 안전 관리 필요성, 높은 초기 투자
- 적용: 대형 AGV, 연속 작동 요구 환경, 친환경 정책 중시 기업
하이브리드 시스템
- 배터리와 다른 에너지원 결합: 슈퍼캐패시터, 발전기 등
- 장점: 에너지 효율 증가, 피크 전력 수요 대응, 배터리 수명 연장
- 단점: 시스템 복잡성 증가, 비용 상승
- 적용: 가변적 전력 요구사항, 회생 제동 기회가 많은 환경
유선 전력 공급
- 전도성 트랙 방식: 바닥 또는 천장의 전도성 레일에서 전력 공급
- 유도성 전력 전송: 바닥에 매립된 케이블에서 무선으로 전력 전송
- 장점: 지속적 전력 공급, 배터리 관리 불필요
- 단점: 인프라 의존성, 경로 유연성 제한
자동 충전 시스템 유형
AGV의 자동 충전을 위한 다양한 기술적 접근법이 있습니다:
접촉식 충전
AGV가 충전소에 물리적으로 접촉하여 전기를 공급받는 방식입니다. 일반적으로 충전 단자나 핀이 AGV의 접촉점과 연결됩니다. 간단하고 신뢰성이 높지만, 접촉부 마모와 정밀한 도킹이 필요한 단점이 있습니다. 대부분의 상용 AGV 시스템에서 널리 사용되고 있습니다.
무선 충전
전자기 유도나 공진 결합 방식으로 물리적 접촉 없이 충전하는 방식입니다. 충전 패드 위에 AGV가 위치하면 자동으로 충전이 시작됩니다. 마모나 접촉 문제가 없지만, 효율이 낮고 충전 속도가 느릴 수 있으며 정밀한 위치 조정이 필요합니다. 클린룸, 위험물 취급 환경에 적합합니다.
배터리 교체 시스템
방전된 배터리를 완충된 배터리로 자동으로 교체하는 방식입니다. 배터리 교체 스테이션에서 로봇 메커니즘이 배터리 팩을 신속하게 교체합니다. 충전 대기 시간 없이 즉시 작업 복귀가 가능하며 배터리 수명 최적화에 유리하지만, 추가 배터리와 교체 인프라 비용이 발생합니다. 24/7 운영 환경에 적합합니다.
기회 충전
작업 중 짧은 휴식 시간이나 대기 시간을 활용하여 부분 충전하는 전략입니다. 작업 구역 여러 곳에 충전 스테이션을 분산 배치하여 활용합니다. 가동 시간을 최대화하고 배터리 크기를 최적화할 수 있지만, 복잡한 충전 관리와 추가 인프라가 필요합니다. 피크 시간과 비피크 시간이 명확한 환경에 적합합니다.
배터리 관리 시스템(BMS)
효율적인 배터리 사용과 수명 연장을 위한 배터리 관리 시스템은 다음과 같은 핵심 기능을 수행합니다:
모니터링 및 진단
- 실시간 상태 모니터링: 전압, 전류, 온도, SOC(충전 상태), SOH(건강 상태) 등 추적
- 셀 밸런싱: 배터리 팩 내 모든 셀의 균등한 충전 상태 유지
- 이상 감지: 과전압, 과전류, 과열 등 위험 상황 감지 및 알림
- 성능 분석: 충전/방전 사이클, 용량 감소율 등 장기적 성능 추적
충전 최적화
- 적응형 충전 프로필: 배터리 상태와 필요에 따른 최적 충전 방식 선택
- 충전 일정 관리: 전력 요금이 저렴한 시간대나 작업 부하가 낮은 시간대에 충전
- 급속 충전 관리: 필요 시 급속 충전과 배터리 수명 간 균형 조정
- 온도 보상: 온도에 따른 충전 매개변수 자동 조정
충전 일정 및 전략 최적화
AGV 시스템의 전체 효율성을 높이기 위한 충전 일정 관리 전략은 다음과 같은 요소를 고려합니다:
충전 임계값 관리
배터리 잔량의 하한선을 설정하여 이에 도달하면 충전을 진행합니다. 임계값은 작업 패턴, 배터리 특성, 충전소까지의 거리 등을 고려하여 동적으로 조정될 수 있습니다. 너무 낮은 임계값은 비상 상황 위험을, 너무 높은 임계값은 불필요한 충전 빈도 증가를 초래할 수 있습니다.
예측적 충전 관리
작업 패턴과 에너지 소비율을 분석하여 충전 필요성을 미리 예측합니다. 작업 우선순위, 예상 에너지 소비, 충전소까지의 거리를 고려한 알고리즘이 최적의 충전 시점을 결정합니다. 이를 통해 긴급 충전 상황을 방지하고 작업 연속성을 향상시킬 수 있습니다.
충전소 부하 분산
여러 충전소의 사용률을 균등하게 분배하여 특정 충전소의 과부하나 대기 시간을 방지합니다. 각 충전소의 가용성, 위치, 현재 대기 AGV 수, 전력 공급 상태 등을 고려하여 AGV를 최적의 충전소로 안내합니다.
플릿 전체 최적화
개별 AGV가 아닌 전체 AGV 플릿의 관점에서 충전 일정을 최적화합니다. 작업량 피크 시간에 충분한 AGV가 가용되도록 교대 충전 일정을 수립하고, 충전 일정을 작업 할당과 통합하여 시스템 전체의 생산성을 극대화합니다.
에너지 효율 최적화 기술
AGV의 에너지 사용을 최소화하고 배터리 수명을 연장하기 위한 다양한 기술이 활용됩니다:
- 회생 제동: 감속 시 발생하는 운동 에너지를 전기 에너지로 변환하여 배터리 충전
- 경량 설계: 프레임과 구성요소의 경량화를 통한 에너지 소비 감소
- 에너지 효율적 경로 계획: 에너지 소비를 고려한 최적 경로 선택(평지 우선, 급가속 회피)
- 동적 속도 프로파일: 상황에 따라 속도와 가속도를 최적화하여 에너지 효율 향상
- 유휴 모드 관리: 대기 시간 동안 비필수 시스템의 전력 소비 최소화
- 고효율 구동 시스템: 에너지 효율이 높은 모터와 드라이브 시스템 채택
- 적응형 전력 관리: 작업 부하에 따라 시스템 성능과 전력 소비를 동적으로 조절
자동 충전 관련 시스템 통합
자동 충전 시스템은 다른 AGV 관리 시스템과 긴밀하게 통합되어야 효과적으로 작동합니다:
교통 관리 시스템과의 통합
충전을 위한 이동 경로를 교통 시스템에 통합하여 우선순위를 부여하고, 충전소 주변의 교통 흐름을 최적화합니다. 배터리 부족 AGV의 충전소 접근을 위한 특별 권한을 부여하고, 충전소 진입/퇴출 경로의 원활한 흐름을 관리합니다.
작업 관리 시스템과의 통합
배터리 상태를 작업 할당 결정에 반영하여 에너지 소비가 높은 작업은 충전 상태가 좋은 AGV에 할당합니다. 또한 충전 일정을 고려하여 작업을 분배하고, 충전 시간을 작업 계획에 포함시켜 전체 시스템 가용성을 최적화합니다.
유지보수 시스템과의 통합
배터리 성능 데이터를 유지보수 일정 계획에 활용하고, 배터리 교체 작업을 다른 유지보수 작업과 조율합니다. 충전 패턴과 배터리 성능의 상관관계를 분석하여 예방적 유지보수 계획을 수립합니다.
최신 기술 동향으로는 배터리 기술의 지속적인 발전으로 에너지 밀도 증가와 충전 시간 단축이 이루어지고 있으며, 인공지능 기반 배터리 관리 시스템이 충전 패턴 학습과 최적화를 통해 더욱 효율적인 에너지 사용을 가능하게 하고 있습니다. 또한 고속 무선 충전 기술의 발전으로 접촉식 충전과 비슷한 속도로 충전이 가능해지고 있으며, 녹색 에너지(태양광, 풍력 등)와 연계한 AGV 충전 시스템이 환경 친화적인 물류 시스템 구축에 기여하고 있습니다.
자동 충전 및 에너지 관리 기술은 AGV 시스템의 지속 가능한 운영을 위한 핵심 요소로, 배터리 기술, 충전 인프라, 에너지 관리 소프트웨어 등 다양한 기술의 통합적 발전을 통해 계속 진화하고 있습니다. 특히 24시간 연속 운영이 필요한 산업 환경에서는 효율적인 에너지 관리가 시스템 성공의 필수 조건이 되고 있습니다.
AGV 유지보수 및 원격진단
AGV 시스템의 원활한 운영과 장기적인 신뢰성을 확보하기 위해서는 체계적인 유지보수와 효과적인 문제 진단 시스템이 필수적입니다. 현대의 AGV 유지보수는 단순한 고장 수리를 넘어 예방적 관리, 예측적 유지보수, 그리고 원격 모니터링과 진단을 통한 선제적 대응을 포함하는 종합적인 접근법으로 발전하고 있습니다. 이러한 첨단 유지보수 전략은 AGV의 가동률을 높이고, 예상치 못한 가동 중단을 최소화하며, 장비의 수명을 연장시키는 데 기여합니다.
AGV 유지보수의 종류
AGV 시스템의 유지보수는 크게 다음과 같은 유형으로 분류할 수 있습니다:
사후 유지보수(Reactive Maintenance)
- 특징: 고장 발생 후 수리하는 방식
- 적용: 비핵심 구성요소, 예측이 어려운 고장
- 장점: 초기 유지보수 비용 최소화
- 단점: 예상치 못한 가동 중단, 연쇄 고장 위험
예방적 유지보수(Preventive Maintenance)
- 특징: 정해진 일정에 따라 정기적으로 점검 및 부품 교체
- 적용: 마모성 부품, 안전 관련 구성요소
- 장점: 예측 가능한 정비 일정, 갑작스러운 고장 감소
- 단점: 실제 필요보다 조기 교체로 인한 비용 발생
상태 기반 유지보수(Condition-based Maintenance)
- 특징: 장비 상태 모니터링에 기반한 유지보수 수행
- 적용: 센서로 상태 측정이 가능한 구성요소
- 장점: 실제 필요에 따른 유지보수, 자원 효율성
- 단점: 모니터링 시스템 구축 비용, 데이터 해석 복잡성
예측적 유지보수(Predictive Maintenance)
- 특징: 데이터 분석과 머신러닝을 통한 고장 예측
- 적용: 패턴 기반 열화가 발생하는 시스템
- 장점: 최적 시점 유지보수, 가동 중단 시간 최소화
- 단점: 고급 분석 시스템 필요, 초기 데이터 축적 시간
유지보수 대상 주요 구성요소
효과적인 AGV 유지보수 계획을 위해 주요 구성요소별 유지보수 요구사항을 이해하는 것이 중요합니다:
기계적 구성요소
- 구동 시스템: 모터, 기어, 벨트, 체인 등의 마모 및 윤활 점검
- 휠 및 타이어: 마모, 균열, 이물질 점검 및 교체
- 브레이크: 성능 테스트, 패드 마모 점검, 유압 시스템 상태 확인
- 리프팅 메커니즘: 유압 시스템, 실린더, 씰, 액추에이터 점검
- 프레임 및 구조물: 균열, 변형, 부식 여부 점검
전기 및 전자 시스템
- 배터리: 용량, 충전 상태, 단자 부식, 수명 상태 점검
- 전기 연결부: 느슨함, 부식, 손상 여부 확인
- 제어 보드: 오류 로그 확인, 냉각 상태 점검
- 센서: 정확도, 반응성, 청결 상태 확인
- 통신 장치: 신호 강도, 연결 안정성, 안테나 상태 점검
원격 모니터링 및 진단 시스템
현대의 AGV 시스템은 다양한 센서와 통신 기술을 활용하여 원격에서 상태 모니터링과 문제 진단이 가능합니다:
실시간 상태 모니터링
각종 센서를 통해 AGV의 주요 구성요소 상태를 실시간으로 모니터링합니다. 온도, 진동, 전류, 압력, 소음 등의 데이터를 수집하여 정상 범위에서 벗어나는 이상 징후를 감지합니다. 트렌드 분석을 통해 점진적인 성능 저하도 식별 가능합니다.
자가 진단 기능
AGV에 내장된 진단 소프트웨어가 주기적으로 또는 이상 감지 시 자가 진단을 수행합니다. 내부 알고리즘이 센서 데이터와 작동 패턴을 분석하여 구체적인 문제 유형과 위치를 식별하고, 심각도에 따라 경고 수준을 분류합니다.
원격 접속 및 제어
인터넷이나 전용 네트워크를 통해 AGV 시스템에 원격으로 접속하여 상태 확인, 설정 변경, 소프트웨어 업데이트 등을 수행할 수 있습니다. VPN 또는 암호화된 연결을 통해 보안을 유지하면서 원격지에서도 서비스 엔지니어가 시스템에 접근할 수 있습니다.
알림 및 경고 시스템
문제 발생 또는 예방적 조치가 필요한 상황에서 관리자나 유지보수 담당자에게 자동 알림을 전송합니다. 이메일, SMS, 모바일 앱 푸시 알림 등 다양한 채널을 통해 상황의 심각도에 맞는 알림을 제공합니다.
예측적 유지보수 기술
데이터 분석과 인공지능을 활용한 예측적 유지보수는 최적의 시점에 유지보수를 수행하여 비용을 절감하고 가동률을 높이는 첨단 접근법입니다:
데이터 수집
센서, 로그파일, 작동 기록 등 다양한 소스에서 유지보수 관련 데이터를 지속적으로 수집
데이터 분석
수집된 데이터를 통계적 방법, 기계학습, 패턴 인식 등으로 분석하여 이상 징후와 패턴 식별
고장 예측
분석 결과를 바탕으로 구성요소의 잔여 수명과 고장 가능성 예측, 고장 시점과 유형 추정
유지보수 계획
예측된 고장 시점, 부품 가용성, 작업 일정 등을 고려하여 최적의 유지보수 계획 수립
원격 소프트웨어 업데이트 및 관리
AGV 시스템의 소프트웨어를 효율적으로 관리하고 업데이트하는 방법은 다음과 같습니다:
- OTA(Over-The-Air) 업데이트: 무선 네트워크를 통해 AGV의 소프트웨어를 원격으로 업데이트
- 점진적 배포: 일부 AGV에 먼저 적용하여 검증 후 전체 시스템으로 확대
- 스케줄링된 업데이트: 운영에 미치는 영향을 최소화하기 위해 비작동 시간에 업데이트 수행
- 롤백 기능: 문제 발생 시 이전 버전으로 신속하게 되돌릴 수 있는 안전장치
- 변경 관리: 모든 소프트웨어 변경사항의 문서화 및 영향 분석
- 구성 관리: 여러 AGV의 소프트웨어 버전과 설정을 중앙에서 관리
효과적인 유지보수 관리 프로세스
체계적인 유지보수 관리를 위한 프로세스 구축이 중요합니다:
문서화 및 기록 관리
모든 유지보수 활동, 고장 이력, 부품 교체 기록을 체계적으로 문서화하여 추세 분석 및 의사결정 지원
부품 재고 관리
주요 소모품 및 교체 부품의 적정 재고 유지, 공급망 관리, 자동 재주문 시스템 구축
기술 인력 훈련
유지보수 담당자의 지속적인 교육 및 훈련, 신기술 적응 능력 배양, 문제 해결 능력 강화
성능 지표 관리
MTBF(평균 고장 간격), MTTR(평균 수리 시간), OEE(설비종합효율) 등 핵심 성능 지표 추적 및 개선
유지보수 최적화 전략
AGV 유지보수의 효율성과 효과를 극대화하기 위한 전략적 접근법:
전략 | 설명 | 기대 효과 |
중요도 기반 접근법 | 구성요소의 중요도와 고장 영향에 따른 유지보수 우선순위 설정 | 제한된 자원의 효율적 활용, 핵심 기능 안정성 확보 |
통합 유지보수 일정 | 여러 유지보수 작업을 동시에 수행하여 가동 중단 시간 최소화 | 전체 가동 중단 빈도 감소, 유지보수 작업 효율 증가 |
비작동 시간 활용 | 생산성에 영향이 적은 시간대(야간, 주말 등)에 유지보수 수행 | 운영 중단으로 인한 생산성 손실 최소화 |
표준화된 절차 | 유지보수 작업의 표준 절차와 체크리스트 개발 및 적용 | 품질 일관성 확보, 실수 감소, 교육 용이성 |
복구 시간 최적화 | 빠른 고장 진단과 효율적인 수리 프로세스 구축 | MTTR(평균 수리 시간) 감소, 가동률 향상 |
최신 기술 동향으로는 증강현실(AR)을 활용한 원격 지원 시스템이 발전하고 있어, 현장 기술자가 AR 글래스를 착용하고 원격지 전문가의 실시간 지원을 받으며 복잡한 수리를 수행할 수 있게 되었습니다. 또한 디지털 트윈 기술을 활용하여 가상 환경에서 유지보수 작업을 시뮬레이션하고 최적화하는 접근법이 확산되고 있으며, 5G 네트워크의 발전으로 대용량 진단 데이터의 실시간 전송과 원격 모니터링 능력이 크게 향상되고 있습니다.
효과적인 유지보수 및 원격진단 시스템은 AGV의 전체 수명주기 비용(TCO)을 최적화하고, 예상치 못한 가동 중단으로 인한 생산성 손실을 최소화합니다. 특히 24시간 연속 운영 환경에서는 신속한 문제 감지와 해결이 핵심적인 경쟁 요소가 되며, 선제적이고 체계적인 유지보수 전략은 AGV 시스템의 장기적인 성공과 투자 수익률을 결정짓는 중요한 요소입니다.
AGV 데이터 수집 및 분석
AGV 시스템은 운영 과정에서 방대한 양의 데이터를 생성합니다. 이러한 데이터를 체계적으로 수집하고 분석함으로써 운영 효율성 향상, 문제점 조기 발견, 의사결정 최적화 등 다양한 가치를 창출할 수 있습니다. 최신 AGV 시스템은 단순한 물류 자동화 도구를 넘어 데이터 기반 인사이트를 제공하는 지능형 플랫폼으로 진화하고 있으며, 빅데이터 분석과 인공지능 기술의 발전은 이러한 가치 창출 가능성을 더욱 확장시키고 있습니다.
AGV 시스템에서 수집되는 주요 데이터
AGV 시스템은 다양한 유형의 데이터를 생성하며, 이를 목적에 따라 체계적으로 수집합니다:
운영 데이터
- 이동 경로 및 거리: AGV가 이동한 경로와 총 주행 거리
- 임무 완료 시간: 작업 시작부터 완료까지 소요된 시간
- 대기 시간: 새로운 작업 할당을 기다리는 시간
- 교통 상황: 정체 발생 지점과 시간, 대기 시간
- 적재량: 운반한 화물의 무게, 크기, 유형
- 충전 주기: 충전 빈도, 시간, 소요 시간
성능 데이터
- 속도 프로파일: 구간별 속도, 가속/감속 패턴
- 위치 정확도: 목표 위치와 실제 도달 위치 간 오차
- 배터리 성능: 방전 곡선, 충전 효율, 잔존 용량
- 모터 성능: 토크, RPM, 전류 소비량
- 내비게이션 정확도: 경로 추종 오차, 위치 추정 신뢰도
- 반응 시간: 명령 수신부터 실행까지 지연 시간
상태 및 진단 데이터
- 센서 판독값: 모든 센서의 실시간 및 이력 데이터
- 오류 로그: 발생한 오류의 유형, 시간, 상황
- 부품 상태: 구성요소의 건강 상태, 마모도
- 환경 조건: 온도, 습도, 진동 등 작동 환경
- 소프트웨어 상태: 프로세스 상태, 메모리 사용량
- 통신 품질: 신호 강도, 지연 시간, 패킷 손실
환경 인식 데이터
- 장애물 감지: 감지된 장애물의 위치, 크기, 유형
- 트래픽 패턴: 사람과 다른 차량의 이동 패턴
- 맵 업데이트: 환경 변화에 따른 지도 데이터 변경
- 바닥 상태: 마찰, 경사, 불규칙성 등 감지
- 빛과 소음: 작업 환경의 조명 조건과 소음 수준
- 특이 사항: 일상적이지 않은 환경적 특이사항
데이터 수집 아키텍처
AGV 시스템의 데이터를 효과적으로 수집하기 위한 아키텍처는 다음과 같은 계층 구조로 구성됩니다:
분석 및 시각화 계층
수집된 데이터의 분석, 인사이트 도출, 시각화 및 보고
데이터 저장 및 처리 계층
클라우드 또는 온프레미스 서버에서의 데이터 저장, 정제, 가공
게이트웨이 및 중개 계층
엣지 컴퓨팅, 데이터 압축, 전처리, 우선순위 설정
데이터 수집 계층
AGV의 센서, 로그, 제어 시스템에서 원시 데이터 캡처
데이터 분석 방법론
수집된 AGV 데이터를 가치 있는 인사이트로 변환하기 위한 다양한 분석 방법이 활용됩니다:
기술적 분석(Descriptive Analytics)
"무슨 일이 일어났는가?"에 대한 답을 제공하는 분석 방법으로, 과거 데이터를 요약하고 패턴을 식별합니다. KPI 대시보드, 운영 보고서, 히스토그램, 열지도 등을 통해 AGV 운영 현황을 파악하고, 시간대별, 구역별, 작업 유형별 성능 차이를 시각화합니다.
진단적 분석(Diagnostic Analytics)
"왜 일어났는가?"에 대한 답을 찾는 분석 방법으로, 원인과 결과의 관계를 파악합니다. 상관관계 분석, 근본 원인 분석, 이상 감지 등의 기법을 통해 성능 저하, 오류 발생, 효율성 변화의 원인을 식별하고 문제 해결에 활용합니다.
예측적 분석(Predictive Analytics)
"앞으로 무슨 일이 일어날 것인가?"를 예측하는 분석 방법으로, 과거 데이터 패턴을 기반으로 미래 상황을 예측합니다. 회귀 분석, 시계열 예측, 기계학습 모델 등을 활용하여 장비 고장, 배터리 수명, 작업량 변동, 교통 패턴 등을 예측합니다.
처방적 분석(Prescriptive Analytics)
"어떻게 해야 하는가?"에 대한 지침을 제공하는 가장 고급 형태의 분석으로, 최적의 의사결정을 지원합니다. 시뮬레이션, 최적화 알고리즘, 인공지능 기반 추천 시스템 등을 통해 경로 최적화, 작업 할당, 충전 일정, 유지보수 계획 등의 최적 방안을 제시합니다.
데이터 분석 활용 사례
AGV 데이터 분석은 다양한 영역에서 가치를 창출할 수 있습니다:
운영 최적화
- 경로 효율성 분석: 혼잡 구간과 비효율적 경로 식별 및 개선
- 작업 할당 최적화: 작업 특성과 AGV 위치를 고려한 최적 할당
- 교통 흐름 개선: 병목 구간 식별 및 레이아웃/알고리즘 개선
- 충전 일정 최적화: 배터리 사용 패턴 분석을 통한 충전 전략 개발
- 가동률 최대화: 비생산적 대기 시간 분석 및 최소화
예측적 유지보수
- 고장 예측: 성능 저하 패턴 분석을 통한 고장 사전 예측
- 부품 수명 최적화: 실제 사용 조건에 기반한 교체 주기 결정
- 비정상 감지: 정상 작동 프로파일에서 벗어난 이상 징후 식별
- 정비 계획 최적화: 생산성 영향 최소화 위한 유지보수 일정 계획
- 품질 보증: 시스템 성능의 일관성 모니터링 및 보장
안전성 향상
- 위험 구역 매핑: 충돌이나 사고가 자주 발생하는 구역 식별
- 안전 규정 준수 모니터링: 속도 제한, 안전 구역 준수 여부 추적
- 근접 사고 분석: 실제 사고로 이어지지 않은 위험 상황 분석
- 작업자 상호작용 패턴: 사람과 AGV의 상호작용 방식 분석 및 개선
- 예방적 안전 조치: 데이터 기반 안전 프로토콜 강화
자원 계획 및 확장
- 용량 계획: 작업량 추세 분석을 통한 AGV 수량 최적화
- 투자 수익률 분석: AGV 시스템의 실제 비용 절감 및 생산성 향상 측정
- 병목 현상 예측: 성장에 따라 발생할 수 있는 시스템 제약 예측
- 시뮬레이션 기반 계획: 다양한 시나리오에서의 성능 예측
- 배치 전략: 신규 AGV 도입 시 최적 배치 계획 수립
데이터 시각화 및 대시보드
복잡한 AGV 데이터를 직관적으로 이해하고 빠른 의사결정을 지원하기 위한 시각화 도구들이 활용됩니다:
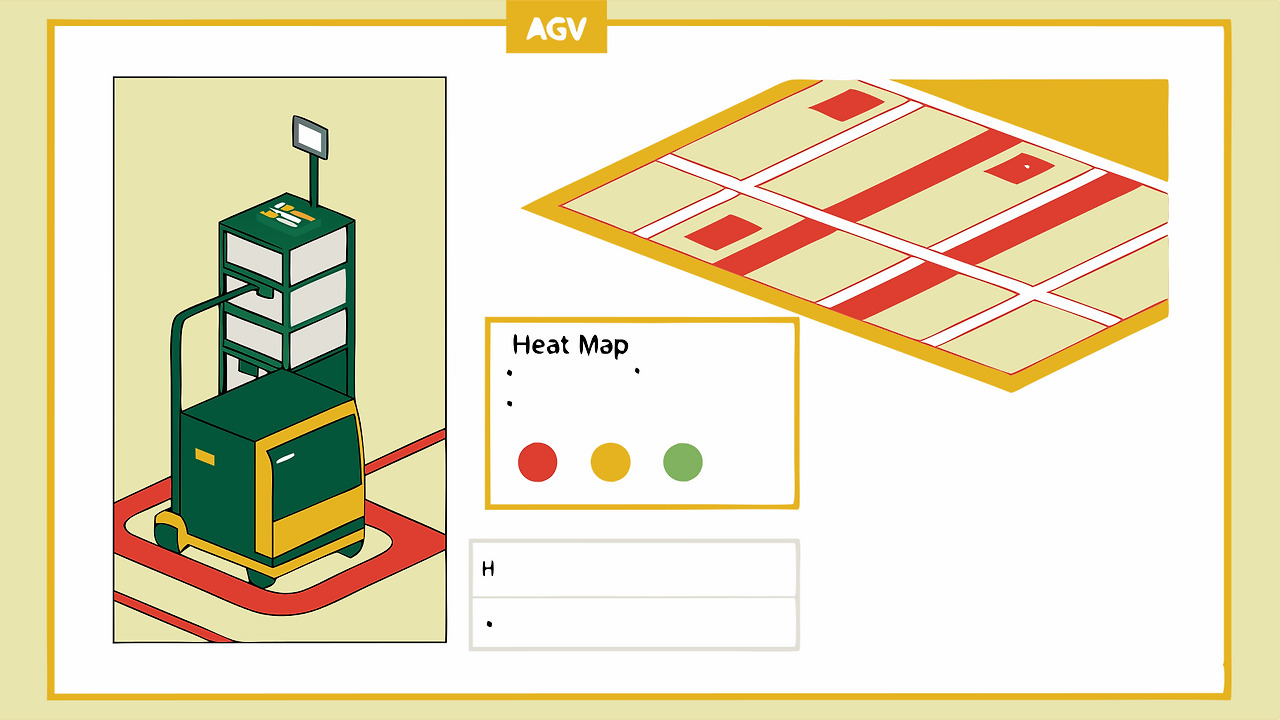
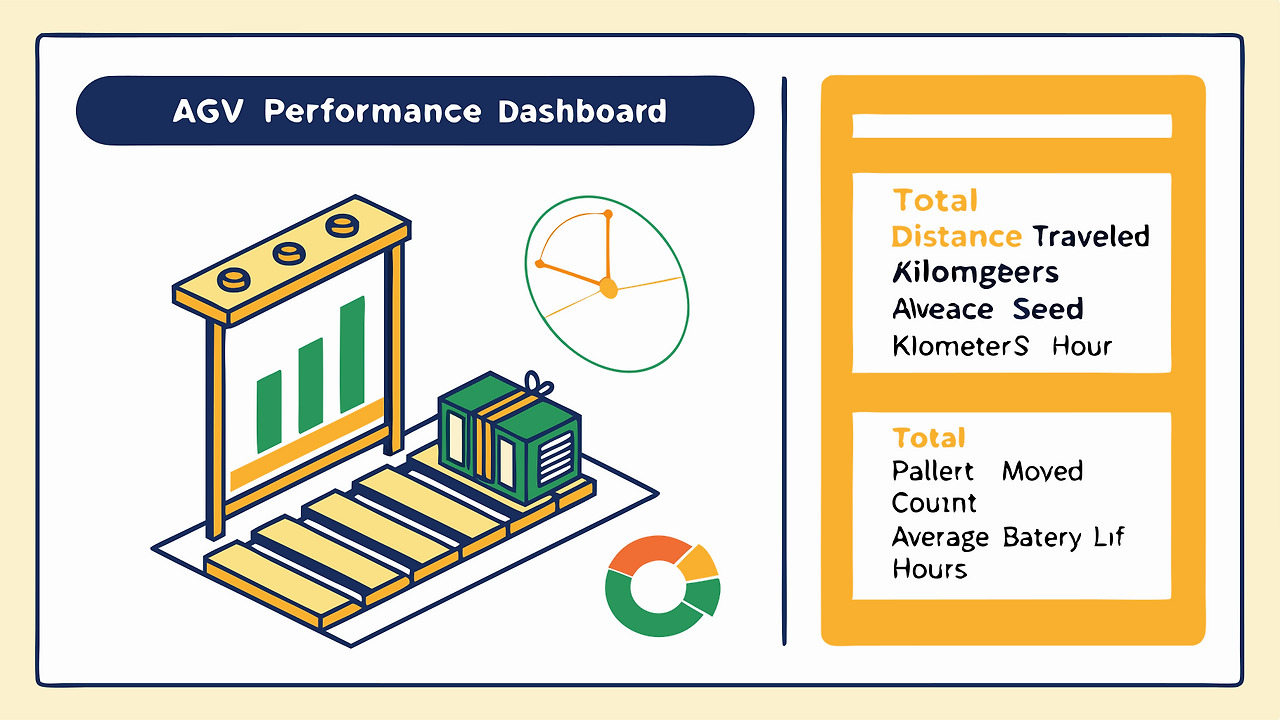
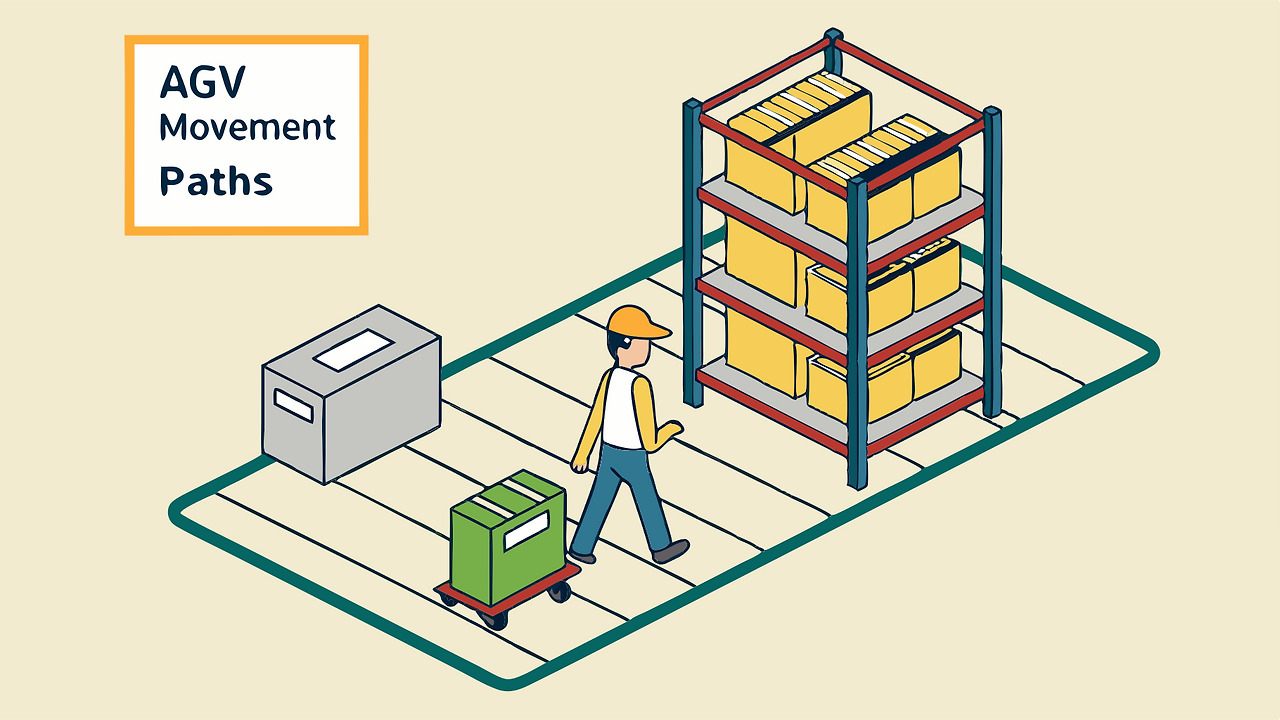
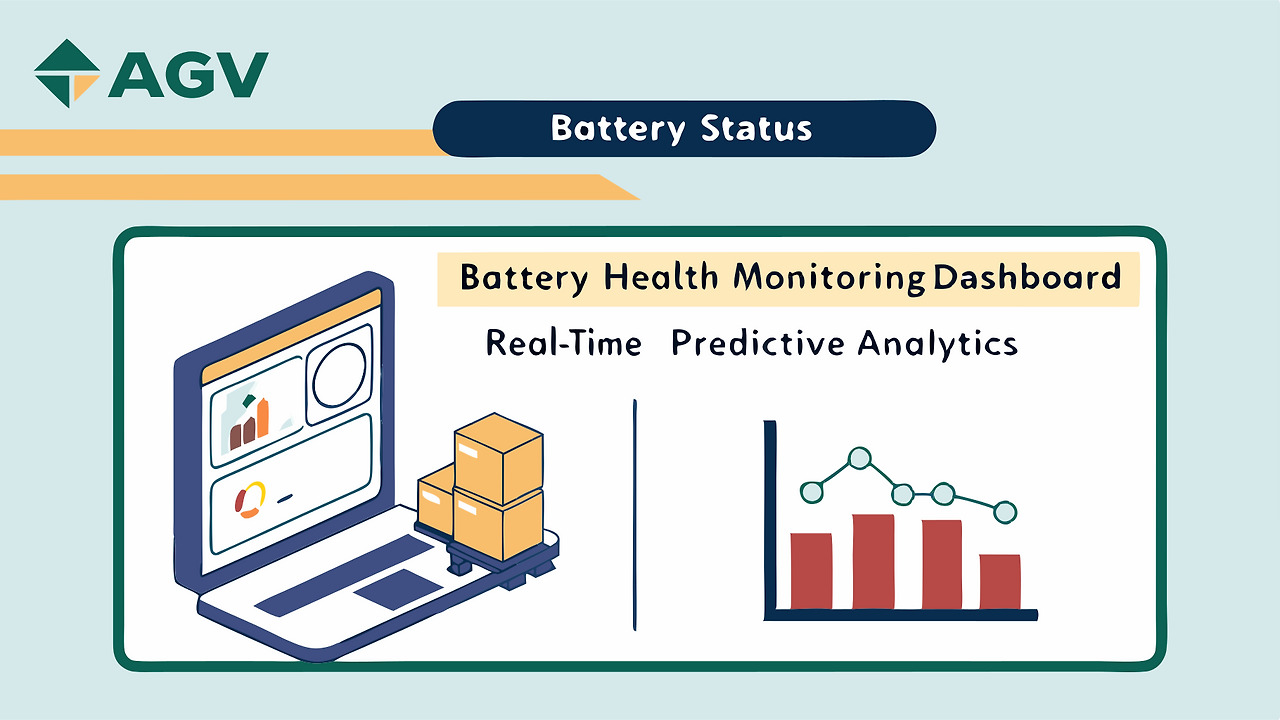
- 실시간 모니터링 대시보드: AGV 위치, 상태, 작업 진행 상황을 실시간으로 표시
- 열지도(Heatmap): 교통 밀도, 대기 시간, 속도 등을 색상으로 구분하여 시각화
- 산키 다이어그램(Sankey Diagram): 물류 흐름과 경로 분포를 시각적으로 표현
- 시계열 차트: 시간에 따른 성능 지표, 배터리 상태 등의 변화를 표시
- 3D 디지털 트윈: 실제 환경의 3D 가상 복제본에 AGV 작동 상태를 시각화
- 경보 및 알림 시스템: 중요 이벤트나 임계값 초과 시 즉각적인 시각적 알림 제공
최신 기술 및 발전 동향
AGV 데이터 수집 및 분석 분야의 최신 기술 동향은 다음과 같습니다:
인공지능과 기계학습
딥러닝 기술을 활용한 비정형 데이터(이미지, 소리 등) 분석, 강화학습을 통한 자율적 경로 최적화, 행동 패턴 학습 기반 예측 알고리즘 등이 발전하고 있습니다. 이를 통해 더 복잡한 패턴을 식별하고 예측 정확도를 높이며, 지속적으로 자가 학습하는 시스템이 구현되고 있습니다.
엣지 컴퓨팅
AGV 자체에서 데이터를 처리하는 엣지 컴퓨팅 기술이 발전하면서 네트워크 지연 없이 실시간 의사결정이 가능해지고 있습니다. 중앙 서버 의존도 감소로 네트워크 장애에도 지속 작동이 가능하며, 데이터 전송량 감소로 통신 효율성이 향상되고 있습니다.
통합 데이터 플랫폼
AGV 데이터, WMS, ERP, MES 등 다양한 시스템의 데이터를 통합하는 플랫폼이 발전하고 있습니다. 이를 통해 엔드투엔드 프로세스 가시성이 확보되고, 부서간 데이터 사일로가 해소되며, 전사적 관점의 최적화가 가능해지고 있습니다.
디지털 트윈
물리적 AGV 시스템의 디지털 복제본을 만들어 실시간 모니터링, 시뮬레이션, 최적화에 활용하는 기술이 발전하고 있습니다. 가상 환경에서 변경 사항을 테스트하여 위험을 최소화하고, "what-if" 시나리오 분석을 통해 의사결정을 지원하며, 물리적 시스템과 디지털 모델 간 실시간 동기화가 구현되고 있습니다.
AGV 데이터 수집 및 분석의 발전은 단순한 운영 자동화를 넘어 지속적인 최적화와 혁신을 가능하게 합니다. 특히 빅데이터 기술, IoT, 인공지능의 발전과 함께 AGV 시스템은 지능형 의사결정 플랫폼으로 진화하고 있으며, 이는 물류 및 제조 환경에서의 운영 효율성과 경쟁력을 크게 향상시키고 있습니다.
그러나 이러한 발전과 함께 데이터 보안, 프라이버시, 시스템 복잡성 관리 등의 새로운 과제도 등장하고 있습니다. 성공적인 AGV 데이터 전략을 위해서는 기술적 역량과 함께 명확한 비즈니스 목표 설정, 데이터 거버넌스 구축, 그리고 데이터 기반 조직 문화 조성이 균형있게 이루어져야 합니다.
스마트팩토리와 AGV의 통합
스마트팩토리는 디지털 기술을 활용하여 생산 공정을 자동화, 최적화하고 시스템 간 실시간 연결성을 구현한 차세대 제조 환경입니다. 이러한 스마트팩토리에서 AGV(무인운반차)는 단순한 물류 자동화 도구를 넘어 전체 생산 시스템의 유연성과 효율성을 높이는 핵심 요소로 자리잡고 있습니다. AGV와 스마트팩토리의 통합은 물리적 물류 이동과 디지털 정보 흐름을 결합하여 진정한 사이버-물리 시스템(Cyber-Physical System)을 구현하는 핵심 가교 역할을 수행합니다.
스마트팩토리의 핵심 요소와 AGV의 역할
스마트팩토리를 구성하는 주요 기술 요소와 각 요소에서 AGV가 담당하는 역할을 살펴보겠습니다:
IoT(사물인터넷)
- 스마트팩토리 관점: 센서, 액추에이터, 기계 등 모든 장비의 네트워크 연결 및 데이터 공유
- AGV의 역할: 이동형 IoT 플랫폼으로서 공장 전역에서 데이터 수집 및 전송
- 통합 사례: 환경 모니터링 센서를 탑재한 AGV가 공장 내 온도, 습도, 공기질 등 실시간 측정
빅데이터 및 분석
- 스마트팩토리 관점: 생산 데이터 분석을 통한 인사이트 도출 및 의사결정 지원
- AGV의 역할: 이동 패턴, 작업 효율성, 설비 상태 등의 데이터 제공
- 통합 사례: AGV 이동 데이터 분석을 통한 공장 레이아웃 최적화 및 물류 흐름 개선
AI 및 기계학습
- 스마트팩토리 관점: 패턴 인식, 예측 분석, 자율 의사결정을 통한 지능형 제조
- AGV의 역할: 학습 기반 경로 최적화, 작업 우선순위 결정, 예측적 유지보수
- 통합 사례: 생산 일정 변화에 자동으로 적응하여 최적의 자재 운반 계획 수립
클라우드/엣지 컴퓨팅
- 스마트팩토리 관점: 유연한 컴퓨팅 리소스 활용 및 실시간 데이터 처리
- AGV의 역할: 현장 데이터 전처리(엣지) 및 시스템 전체 최적화(클라우드) 참여
- 통합 사례: AGV가 엣지 컴퓨팅으로 긴급 상황 즉시 대응, 클라우드 연계로 전체 최적화
스마트팩토리-AGV 통합 아키텍처
AGV를 스마트팩토리 시스템과 효과적으로 통합하기 위한 계층적 아키텍처는 다음과 같습니다:
기업 통합 계층
ERP, SCM 등 기업 전체 시스템과의 연계 및 비즈니스 목표 조율
공장 운영 계층
MES, WMS 등 생산 관리 시스템과 AGV 시스템 간 작업 조율
제어 계층
AGV 관제 시스템과 다른 자동화 장비(로봇, 컨베이어 등) 제어 시스템 간 통합
디바이스 계층
개별 AGV와 작업 스테이션, 센서, 액추에이터 등 물리적 장치 간 통신
주요 통합 접점과 인터페이스
스마트팩토리 환경에서 AGV가 다른 시스템 및 장비와 통합되는 주요 접점들은 다음과 같습니다:
생산 설비 연계
- 자동화 생산 라인: 생산 라인의 작업 완료 신호에 따른 자동 자재 공급/완제품 수거
- 로봇 시스템: 협동 로봇과 AGV 간 작업 조율을 통한 원활한 물류 흐름
- 자동 보관 시스템: AS/RS(자동창고)와 AGV의 연동으로 원활한 입출고 자동화
- 작업 스테이션: 작업장별 자재 요청 시그널에 대응한 적시 물품 공급
IT 시스템 연계
- MES(제조실행시스템): 생산 계획과 연동된 물류 작업 생성 및 우선순위 설정
- WMS(창고관리시스템): 재고 위치 정보 공유 및 피킹/적재 작업 조율
- ERP(전사적자원관리): 주문 정보와 연계한 생산-물류 통합 관리
- SCADA/HMI: 공장 운영 현황과 AGV 상태의 통합적 모니터링 및 제어
통합 표준 및 프로토콜
AGV와 스마트팩토리 시스템 간의 원활한 통합을 위해 활용되는 주요 표준과 프로토콜은 다음과 같습니다:
- OPC UA(Open Platform Communications Unified Architecture): 산업 장비 간 안전하고 신뢰성 높은 데이터 교환 표준
- MQTT(Message Queuing Telemetry Transport): 경량 메시징 프로토콜로 제한된 대역폭 환경에서 효과적
- VDA 5050: 자동화된 차량의 인터페이스 표준화를 위한 독일 자동차 산업 협회 표준
- ISA-95: 기업 제어 시스템과 제조 운영 시스템 간 통합을 위한 국제 표준
- REST API: 시스템 간 HTTP 기반 통신을 위한 웹 서비스 아키텍처
- JSON/XML: 구조화된 데이터 교환을 위한 데이터 형식
통합 구현 사례 및 시나리오
스마트팩토리 환경에서 AGV 통합의 실제 적용 사례와 작동 시나리오를 살펴보겠습니다:
주문 기반 생산-물류 통합
ERP 시스템에 신규 고객 주문이 입력되면 MES가 생산 계획을 수립하고, 이에 따라 WMS가 필요 자재를 식별합니다. AGV 관제 시스템은 이 정보를 받아 최적의 AGV를 선택하여 창고에서 생산라인으로 자재를 운반합니다. 생산 완료 후에는 자동으로 완제품을 출하 구역으로 이동시킵니다. 전 과정이 디지털로 연결되어 실시간 추적 및 조정이 가능합니다.
로봇-AGV 협업 시스템
협동 로봇이 작업을 완료하면 자동으로 AGV에 신호를 보내 완성품 수거를 요청합니다. AGV가 로봇 작업 구역에 도착하면 로봇이 완성품을 AGV에 정확히 적재하고, AGV는 이를 다음 공정이나 창고로 운반합니다. 두 시스템 간 정밀한 위치 동기화와 작업 타이밍 조율을 통해 원활한 자동화 흐름이 구현됩니다.
적응형 물류 자동화
생산 라인의 실시간 상태(작업 진행도, 자재 소비율 등)를 모니터링하여 AGV의 물류 지원을 동적으로 조정합니다. 특정 라인에서 자재 소비가 예상보다 빠르면 AI 기반 시스템이 이를 감지하고 AGV 작업 우선순위를 자동으로 재조정하여 해당 라인에 우선적으로 자재를 공급합니다. 이를 통해 생산 중단 없이 유연하게 변화에 대응합니다.
품질 관리 연계 시스템
품질 검사 시스템이 불량품을 감지하면 해당 정보가 MES와 AGV 시스템에 동시에 전달됩니다. AGV는 자동으로 불량 제품을 수거하여 재작업 구역이나 폐기 구역으로 운반합니다. 동시에 품질 데이터는 분석 시스템에 전송되어 불량 원인 파악 및 개선 조치에 활용됩니다. 이러한 통합은 품질 문제의 신속한 감지와 대응을 가능하게 합니다.
통합 구현 시 고려사항 및 과제
AGV와 스마트팩토리 시스템의 성공적인 통합을 위해 고려해야 할 주요 사항들은 다음과 같습니다:
상호 운용성
다양한 제조사의 장비와 시스템 간 호환성 확보는 가장 기본적인 과제입니다. 개방형 표준 및 프로토콜 채택, 미들웨어 활용, 표준화된 인터페이스 정의 등을 통해 시스템 간 원활한 통신과 데이터 교환을 보장해야 합니다.
실시간 성능
생산 현장에서는 시스템 간 지연 없는 실시간 통신이 중요합니다. 네트워크 인프라 최적화, 우선순위 기반 메시지 처리, 엣지 컴퓨팅 활용 등을 통해 중요 신호의 실시간 전달을 보장해야 합니다.
보안 및 안전성
통합 시스템의 사이버 보안과 물리적 안전은 필수적입니다. 데이터 암호화, 접근 제어, 네트워크 세분화 등의 보안 조치와 함께 물리적 안전을 위한 이중화된 안전 시스템이 구현되어야 합니다.
확장성 및 유연성
생산 환경 변화와 사업 성장에 대응할 수 있는 확장 가능한 아키텍처가 필요합니다. 모듈식 설계, 서비스 지향 아키텍처(SOA), 클라우드 기반 인프라 등을 통해 시스템 변경이나 확장 시 최소한의 중단으로 대응할 수 있어야 합니다.
통합의 비즈니스 가치 및 효과
AGV와 스마트팩토리의 성공적인 통합은 다음과 같은 비즈니스 가치를 창출합니다:
- 엔드투엔드 가시성: 전체 생산 및 물류 프로세스의 실시간 모니터링과 추적
- 적응형 생산: 시장 수요 변화에 신속하게 대응할 수 있는 유연한 생산 체계
- 자원 최적화: 장비, 인력, 자재, 에너지 등 모든 자원의 효율적 활용
- 품질 향상: 자동화된 검사와 데이터 기반 품질 관리로 불량률 감소
- 지속가능성: 에너지 사용 최적화, 자재 낭비 감소, 탄소 발자국 감소
- 의사결정 개선: 통합 데이터를 기반으로 한 인사이트 도출과 전략적 결정
최신 발전 동향으로는 5G 기술을 활용한 초저지연 통신으로 더욱 정밀한 AGV-설비 간 조율이 가능해지고 있으며, 디지털 트윈 기술을 통해 물리적 AGV와 가상 환경 간 실시간 동기화가 구현되어 시뮬레이션과 최적화가 고도화되고 있습니다. 또한 블록체인 기술을 활용한 안전한 데이터 공유 체계도 도입되고 있습니다.
AGV와 스마트팩토리의 통합은 단순한 기술적 연결을 넘어 제조 패러다임의 변화를 의미합니다. 이는 대량 맞춤 생산, 적시 생산, 지속가능한 제조 등 미래 제조업의 핵심 경쟁력을 구현하는 토대가 되며, 4차 산업혁명 시대에 기업의 디지털 전환과 경쟁력 강화를 위한 필수적인 전략이 되고 있습니다.
AGV와 MES/ERP 시스템 연동
현대 제조 및 물류 환경에서 AGV 시스템은 독립적으로 운영되기보다 기업의 핵심 정보 시스템인 MES(Manufacturing Execution System, 제조실행시스템)와 ERP(Enterprise Resource Planning, 전사적자원관리) 시스템과 긴밀하게 연동되어 운영됩니다. 이러한 통합은 실시간 데이터 공유, 프로세스 자동화, 의사결정 최적화를 가능하게 하여 생산성 향상과 비용 절감, 그리고 전체 공급망의 가시성 확보에 크게 기여합니다. AGV 시스템과 기업 정보 시스템의 연동은 물리적 물류 흐름과 정보 흐름을 완벽하게 동기화하는 디지털 트랜스포메이션의 핵심 요소입니다.
MES, ERP, AGV 시스템의 기본 역할
각 시스템의 기본적인 역할과 책임 영역을 이해하는 것이 통합의 첫 단계입니다:
ERP(전사적자원관리) 시스템
- 비즈니스 수준의 계획 및 관리: 판매, 구매, 재무, 인사 등 전사적 자원 관리
- 장기적 생산 계획: 주문, 수요 예측 기반의 생산 계획 수립
- 재고 관리: 원자재, 부품, 완제품의 재고 수준 관리
- 비용 및 수익 분석: 생산 및 물류 활동의 재무적 영향 추적
- 통합 데이터 저장소: 기업 전체의 비즈니스 데이터 중앙 관리
MES(제조실행시스템)
- 생산 현장 실행 및 모니터링: 실시간 생산 일정 관리 및 진행 상황 추적
- 작업 지시 관리: 생산 작업 지시서 생성 및 배포
- 품질 관리: 공정 중 품질 검사 및 결과 기록
- 설비 모니터링: 생산 설비의 상태 및 성능 모니터링
- 작업자 관리: 작업 할당, 작업 시간 추적, 작업 지침 제공
AGV(무인운반차) 시스템
- 물리적 물류 이동: 원자재, 부품, 완제품의 자동화된 운반
- 운반 작업 관리: 운반 요청 접수, 우선순위 설정, AGV 할당
- 경로 계획 및 교통 관리: 최적 경로 선택, AGV 간 충돌 방지
- 상태 모니터링: AGV 위치, 배터리 상태, 작업 진행 상황 추적
- 장애물 감지 및 안전 관리: 안전한 운행을 위한 환경 감지
연동 아키텍처 및 데이터 흐름
AGV 시스템과 MES/ERP 시스템의 효과적인 연동을 위한 아키텍처와 데이터 흐름은 다음과 같습니다:
AGV-MES 연동
MES는 생산 계획, 작업 지시, 자재 요구사항을 AGV 시스템에 전달합니다. AGV 시스템은 운반 작업 상태, 물류 이동 현황, 작업 완료 보고를 MES에 제공합니다. 이 인터페이스는 실시간 성이 중요하며, 생산 라인의 필요에 맞춰 적시에 물류 지원이 이루어져야 합니다.
AGV-ERP 연동
ERP는 장기 생산 계획, 자재 및 제품 마스터 데이터, 재고 정보를 AGV 시스템에 제공합니다. AGV 시스템은 재고 이동 확인, 리소스 활용 데이터, 운영 비용 정보를 ERP에 전달합니다. 이 인터페이스는 전사적 자원 계획과 물류 실행의 조율을 가능하게 합니다.
통합 데이터 흐름
ERP에서 생성된 생산 계획은 MES로 전달되어 상세 작업 지시로 변환됩니다. MES는 이를 바탕으로 AGV 시스템에 물류 작업을 지시합니다. AGV 작업 실행 결과는 MES로 전달되어 생산 진행 상황에 반영되고, 이는 다시 ERP로 전송되어 전사적 자원 계획과 의사결정에 활용됩니다.
연동 방식 및 기술
AGV 시스템과 MES/ERP 시스템 간의 연동은 다양한 기술적 방식으로 구현될 수 있습니다:
API(Application Programming Interface) 기반 통합
각 시스템이 제공하는 표준 API를 활용하여 직접 연동하는 방식입니다. REST API, SOAP 웹 서비스 등이 주로 사용되며, 특정 이벤트나 요청에 따라 실시간 정보 교환이 가능합니다. 시스템 간 직접적인 통신으로 지연이 적고 유연한 데이터 교환이 가능하지만, 시스템 변경 시 API 업데이트가 필요할 수 있습니다.
미들웨어 기반 통합
Enterprise Service Bus(ESB), Integration Platform as a Service(iPaaS) 등의 통합 미들웨어를 활용하는 방식입니다. 미들웨어가 각 시스템 간 데이터 변환, 라우팅, 프로토콜 변환을 담당하여 느슨한 결합(Loose Coupling)을 제공합니다. 여러 시스템의 복잡한 통합에 적합하며 확장성이 우수하지만, 추가 인프라 비용이 발생합니다.
데이터베이스 통합
공유 데이터베이스나 데이터 복제를 통해 시스템 간 정보를 공유하는 방식입니다. 배치 프로세스, 트리거, ETL(Extract, Transform, Load) 도구 등이 활용됩니다. 구현이 상대적으로 간단하고 대량 데이터 이전에 적합하지만, 실시간성이 떨어질 수 있으며 데이터 일관성 유지 관리가 필요합니다.
메시지 큐 기반 통합
MQTT, AMQP, Kafka 등의 메시지 브로커를 통해 비동기 통신을 구현하는 방식입니다. 발행-구독(Publish-Subscribe) 모델로 시스템 간 결합도를 낮추고 확장성을 높입니다. 시스템 부하 분산, 내결함성 확보, 비동기 처리에 적합하지만, 메시지 순서 보장과 중복 처리 방지를 위한 추가 로직이 필요할 수 있습니다.
주요 연동 영역 및 기능
AGV 시스템과 MES/ERP 시스템 연동을 통해 구현되는 주요 기능과 영역은 다음과 같습니다:
생산 계획 및 작업 할당
- ERP의 생산 계획을 기반으로 MES가 작업 지시 생성
- MES의 작업 지시에 따른 AGV 물류 작업 자동 생성
- 실시간 생산 우선순위 변경 시 AGV 작업 우선순위 자동 조정
- 작업 상태 피드백을 통한 생산 계획 실시간 업데이트
- 생산 라인별 필요 시점과 물량에 맞춘 JIT(Just-In-Time) 물류 지원
재고 및 자재 관리
- ERP 재고 데이터 기반의 정확한 픽업 위치 정보 제공
- AGV 이동에 따른 실시간 재고 위치 및 상태 업데이트
- 자재 소진 예측에 따른 선제적 보충 작업 생성
- AGV 운반 작업과 자재 로트 추적 연계
- 재고 정확도 향상을 위한 AGV 기반 자동 재고 확인
품질 관리 및 추적성
- 품질 검사 결과에 따른 AGV 라우팅 자동 결정(합격품/불량품)
- 제품 및 자재의 이력 추적을 위한 운반 정보 기록
- 특정 로트 리콜 시 관련 자재/제품의 신속한 위치 파악
- 규제 준수를 위한 물류 이동의 문서화 및 보고
- AGV 센서 데이터를 활용한 운송 중 환경 조건 모니터링
성능 모니터링 및 분석
- AGV 운영 데이터를 ERP/MES 성능 지표와 통합 분석
- 물류 KPI(Key Performance Indicators) 실시간 모니터링
- 병목 현상 및 비효율 구간 식별을 위한 통합 데이터 분석
- AGV 자원 활용도 및 ROI(투자수익률) 평가
- 예측적 유지보수를 위한 운영 패턴 분석
통합의 도전 과제와 해결 방안
AGV와 MES/ERP 시스템의 연동 과정에서 발생할 수 있는 주요 도전 과제와 해결 방안은 다음과 같습니다:
도전 과제 | 영향 | 해결 방안 |
시스템 간 데이터 호환성 | 데이터 형식, 구조, 의미의 불일치로 인한 통합 오류 | 표준 데이터 모델 정의, 변환 매핑 테이블 구축, 산업 표준 채택 |
실시간 성능 요구사항 | 데이터 지연으로 인한 생산-물류 동기화 문제 | 이벤트 기반 아키텍처, 엣지 컴퓨팅 활용, 네트워크 최적화 |
시스템 복잡성 증가 | 유지보수 어려움, 문제 진단 및 해결 지연 | 모듈식 설계, 명확한 인터페이스 정의, 통합 모니터링 도구 도입 |
레거시 시스템 통합 | 오래된 ERP/MES와 최신 AGV 시스템 간 기술 격차 | 중간 연결 계층 개발, API 어댑터 활용, 단계적 현대화 계획 |
보안 및 접근 제어 | 시스템 간 데이터 공유로 인한 보안 취약점 | 세분화된 접근 제어, 암호화, 보안 감사 체계 구축 |
연동 성공 사례 및 효과
AGV와 MES/ERP 시스템의 성공적인 연동이 가져온 실제 비즈니스 효과의 사례입니다:
자동차 부품 제조업체
AGV-MES-ERP 통합으로 생산 라인 변경 시 물류 흐름 자동 조정, 재고 정확도 99.8% 달성, 생산 리드타임 35% 감소
전자제품 물류 센터
주문 처리 시스템과 AGV 연동으로 피킹 오류 90% 감소, 주문 처리 속도 45% 향상, 인력 비용 30% 절감
제약 제조 시설
엄격한 규제 준수 위한 전체 공정 통합, 배치 추적성 100% 확보, 문서화 작업 75% 자동화, 규제 감사 준비 시간 60% 단축
식품 생산 공장
원료에서 완제품까지 콜드체인 모니터링 통합, 식품 안전성 위반 90% 감소, 유통기한 관리 정확도 향상으로 폐기율 45% 감소
구현 접근법 및 로드맵
AGV와 MES/ERP 시스템의 연동을 위한 단계적 접근 방법은 다음과 같습니다:
현황 분석 및 요구사항 정의
현재 시스템 상태 파악, 비즈니스 프로세스 매핑, 통합 요구사항 우선순위 설정
통합 아키텍처 설계
연동 방식 선택, 데이터 모델 정의, 인터페이스 설계, 보안 및 성능 고려사항 반영
파일럿 구현 및 검증
핵심 기능 중심의 프로토타입 개발, 제한된 환경에서 검증, 피드백 수집 및 보완
단계적 구현 및 배포
우선순위에 따른 점진적 기능 구현, 테스트 및 검증, 사용자 교육, 변화 관리
모니터링 및 지속적 개선
통합 시스템 성능 모니터링, 사용자 피드백 수집, 기능 개선 및 최적화
최신 기술 동향으로는 클라우드 기반 통합 플랫폼을 활용한 유연하고 확장성 있는 연동 아키텍처가 증가하고 있으며, API 관리 도구를 통해 다양한 시스템 간 인터페이스를 효율적으로 관리하는 접근법이 확산되고 있습니다. 또한 인공지능과 기계학습을 활용하여 물류-생산 프로세스를 자동으로 최적화하는 지능형 통합 시스템도 등장하고 있습니다.
AGV와 MES/ERP 시스템의 연동은 단순한 기술적 통합을 넘어 디지털 제조와 물류의 핵심 토대를 구축하는 전략적 과제입니다. 성공적인 통합은 생산성 향상, 비용 절감, 품질 개선과 같은 직접적인 효과뿐 아니라, 실시간 의사결정 능력, 변화 대응력, 고객 만족도 향상 등 장기적인 경쟁 우위를 제공합니다. 특히 Industry 4.0과 스마트 물류의 시대에 이러한 통합은 더 이상 선택이 아닌 필수적인 과제로 자리잡고 있습니다.
물류창고 운영에서의 AGV
물류창고는 현대 공급망의 핵심 허브로, 전자상거래의 폭발적 성장과 소비자 기대 상승에 따라 그 중요성이 더욱 커지고 있습니다. 이러한 환경에서 AGV(무인운반차)는 물류창고 운영의 효율성, 정확성, 안전성을 획기적으로 향상시키는 혁신 기술로 주목받고 있습니다. AGV는 단순한 운반 장비를 넘어 지능형 물류 시스템의 핵심 구성요소로 진화하면서, 인력 의존도가 높고 반복 작업이 많은 전통적 창고 운영 방식을 자동화된 스마트 물류 시스템으로 변화시키고 있습니다.
물류창고 내 AGV의 주요 활용 영역
물류창고 운영에서 AGV가 적용되는 주요 영역과 각 영역별 특징은 다음과 같습니다:
입고(Receiving) 및 하역(Unloading)
- 트럭이나 컨테이너에서 하역된 상품을 입고 구역에서 보관 구역으로 운반
- 바코드나 RFID 스캐너와 연동하여 자동 입고 검수 지원
- 대량 입고 시 신속한 처리로 트럭 대기 시간 감소
- 무거운 팔레트나 컨테이너의 인력 운반 부담 경감
이송(Transfer) 및 보관(Storage)
- 입고 물품을 적절한 보관 위치로 자동 운반
- WMS(창고관리시스템)와 연동하여 최적 보관 위치 결정
- 높은 선반 위치까지 접근 가능한 특수 AGV 활용
- 자동 보관 시스템(AS/RS)과 연계하여 완전 자동화된 보관 실현
피킹(Picking) 및 분류(Sorting)
- 주문 처리를 위한 상품 픽업 및 분류 작업 지원
- '상품을 사람에게(Goods-to-Person)' 방식으로 피킹 효율 향상
- 여러 피킹 지점을 순회하며 주문 통합 지원
- 자동 분류 시스템과 연동하여 배송지별 상품 분류
포장(Packing) 및 출하(Shipping)
- 피킹된 상품을 포장 스테이션으로 운반
- 완성된 주문 패키지를 출하 구역으로 이동
- 배송 트럭이나 컨베이어 시스템으로 자동 적재
- 마감 시간에 맞춘 출하 우선순위 관리
물류창고에서 사용되는 AGV 유형
물류창고의 다양한 작업 요구사항과 환경을 고려하여 여러 유형의 AGV가 사용됩니다:
팔레트 운반형 AGV
표준 팔레트를 운반하기 위한 AGV로, 물류창고에서 가장 널리 사용되는 유형입니다. 포크 메커니즘을 갖추고 있어 팔레트를 들어 올려 운반하며, 1-2톤 이상의 중량물 운반이 가능합니다. 주로 입고, 보관, 출하 영역에서 활용되며, 지게차형, 스태커형, 스트래들형 등 다양한 하위 유형이 있습니다. 특히 드롭존(drop zone)에서 팔레트를 들어 올려 보관 구역으로 이동하거나, 보관 구역에서 피킹된 팔레트를 포장 구역으로 이동하는 작업에 효과적입니다.
선반 운반형 AGV(셔틀 AGV)
전체 선반 유닛을 들어 올려 이동시키는 AGV로, 특히 전자상거래 물류에 적합합니다. 낮은 프로파일 설계로 선반 아래로 진입하여 전체 선반을 들어 올린 후 피킹 스테이션으로 이동시킵니다. 'Goods-to-Person' 방식의 피킹 시스템에서 핵심 요소로, 작업자가 고정된 위치에서 작업하므로 이동 시간이 크게 줄고 피킹 효율이 향상됩니다. 선반 레이아웃을 동적으로 변경할 수 있어 인기 상품을 피킹 구역 가까이 배치하는 등의 최적화도 가능합니다.
카트형 AGV
소형 컨테이너나 박스를 운반하기 위한 소형 AGV로, 주로 피킹 및 분류 작업에 활용됩니다. 상단에 평평한 적재 공간 또는 컨베이어가 장착되어 있어 다양한 크기의 물품을 운반할 수 있습니다. 배치 피킹(batch picking) 방식에서 피커(picker)를 따라다니며 여러 상품을 수집하거나, 피킹된 상품을 포장 구역으로 운반하는 용도로 활용됩니다. 가볍고 민첩하여 좁은 공간에서도 효율적으로 작동할 수 있는 장점이 있습니다.
견인형 AGV
여러 개의 카트를 연결하여 견인하는 AGV로, 대량의 물품을 한 번에 운반할 때 효율적입니다. 입고된 대량 상품을 각 보관 구역으로 분산 배치하거나, 여러 주문 상품을 포장 구역으로 한꺼번에 운반하는 작업에 적합합니다. 견인력이 강하고 한 번에 많은 양을 운반할 수 있어 비용 효율적이지만, 넓은 회전 반경이 필요하여 공간 요구사항이 큰 편입니다.
물류창고 AGV의 주요 기능 및 기술
물류창고 환경에서 AGV가 효과적으로 작동하기 위한 핵심 기능과 기술은 다음과 같습니다:
창고 매핑 및 내비게이션
물류창고의 복잡한 환경에서 정확한 이동을 위한 기술입니다. 레이저, 비전, SLAM 등 다양한 내비게이션 기술을 활용하여 레이아웃 변경에도 유연하게 대응할 수 있습니다. 좁은 통로와 높은 선반이 많은 물류창고 특성에 맞춰 정밀한 위치 제어 기능이 중요합니다.
교통 관리 및 작업 최적화
여러 AGV의 움직임을 조율하고 작업 우선순위를 관리하는 시스템입니다. WMS의 주문 데이터를 기반으로 AGV 작업을 자동 생성하고, 교통 흐름, 배터리 상태, 작업 긴급성 등을 고려한 지능적 작업 할당이 이루어집니다. 특히 성수기나 프로모션 기간의 급증하는 주문량에도 유연하게 대응할 수 있는 확장성이 중요합니다.
WMS 통합 및 실시간 인벤토리 추적
창고관리시스템(WMS)과의 원활한 통합을 통해 인벤토리 정보의 실시간 정확성을 보장합니다. AGV의 물품 이동에 따라 WMS의 재고 위치 및 상태 정보가 자동 업데이트되고, 바코드/RFID 스캐너와 연동하여 상품 식별 및 검증이 자동화됩니다. 이를 통해 재고 정확도가 크게 향상되고 분실 재고(lost inventory) 문제가 해결됩니다.
데이터 수집 및 성능 분석
AGV 운영 데이터를 수집하고 분석하여 지속적인 개선을 가능하게 합니다. 이동 패턴, 정체 구역, 물품 흐름, 피킹 속도 등의 데이터를 분석하여 창고 레이아웃 최적화, 상품 배치 전략 수립, 인력 배치 계획 등에 활용합니다. 이를 통해 데이터 기반의 의사결정과 지속적인 프로세스 개선이 가능해집니다.
물류창고 AGV 도입의 효과 및 이점
AGV 도입을 통해 물류창고가 얻을 수 있는 주요 효과와 이점은 다음과 같습니다:
인건비 절감
반복적인 운반 작업 자동화로 인력 필요성 감소, 특히 24시간 운영 환경에서 큰 절감 효과
생산성 향상
무중단 작업, 일관된 속도, Goods-to-Person 방식 적용으로 피킹 효율 증가
오류 감소
잘못된 위치 이동, 잘못된 상품 피킹, 분실 재고 등 인적 오류 대폭 감소
공간 효율 증가
통로 폭 최소화, 수직 공간 활용 극대화로 창고 저장 용량 향상
이 외에도 작업자 안전성 향상(부상 위험 감소, 인체공학적 작업 환경), 운영 유연성 강화(수요 변동에 따른 확장/축소 용이), 지속가능성 개선(에너지 효율화, 탄소 발자국 감소), 그리고 고객 만족도 향상(빠른 주문 처리, 배송 정확도 증가) 등의 효과가 있습니다.
물류창고 AGV 구현 사례
글로벌 물류 환경에서 성공적인 AGV 도입 사례와 그 성과를 살펴보겠습니다:
아마존 로보틱스
아마존은 2012년 키바 시스템즈(Kiva Systems)를 인수하여 아마존 로보틱스로 발전시켰습니다. 수만 대의 선반 운반형 AGV를 전 세계 물류센터에 배치하여 'Goods-to-Person' 피킹 시스템을 구현했습니다. 이를 통해 주문 처리 시간을 75분에서 15분으로 단축하고, 창고 저장 용량을 40% 증가시켰으며, 운영 비용을 20% 이상 절감했습니다. 특히 블랙 프라이데이와 같은 피크 시즌에 유연하게 대응할 수 있는 능력이 크게 향상되었습니다.
오카도(Ocado)
영국의 온라인 식료품 유통업체 오카도는 "The Hive"(벌집)라 불리는 혁신적인 AGV 기반 창고 자동화 시스템을 개발했습니다. 3D 그리드 위에서 1,100대 이상의 AGV가 작동하며 식료품 컨테이너를 운반합니다. 이 시스템은 시간당 65,000개 이상의 주문 처리가 가능하며, 220,000개 이상의 상품을 관리합니다. 신선식품의 특성을 고려한 최적 온도 관리, 유통기한 관리, 깨지기 쉬운 상품 처리 등의 기능을 갖추고 있으며, 기존 창고 대비 인건비를 50% 절감했습니다.
DHL 공급망
글로벌 물류 기업 DHL은 다양한 유형의 AGV를 조합한 하이브리드 자동화 시스템을 여러 물류센터에 도입했습니다. 팔레트 운반용 AGV, 카트형 AGV, 협동 로봇 등을 상황에 맞게 활용하며, 특히 협동 로봇(LocusBot)을 도입하여 피커의 이동 거리를 60% 감소시켰습니다. 또한 인공지능 기반 수요 예측 시스템과 AGV를 연동하여 계절적 변동과 캠페인에 대응한 물류 흐름을 최적화했습니다. 이러한 접근법으로 첫 해에 ROI 129%를 달성하고, 피킹 오류를 95% 감소시켰습니다.
물류창고 AGV 도입 시 고려사항
물류창고에 AGV 시스템을 도입할 때 고려해야 할 주요 사항들은 다음과 같습니다:
물류 흐름 및 요구사항 분석
현재 물류 프로세스, 상품 특성(크기, 무게, 취급 요구사항), 피크 시간 처리량, 계절적 변동성 등을 상세히 분석하여 AGV 유형과 수량을 결정해야 합니다. 특히 다양한 상품을 취급하는 물류창고의 경우, 상품별 취급 방식과 요구사항을 고려한 맞춤형 AGV 구성이 필요합니다.
창고 레이아웃 및 인프라
기존 창고 레이아웃의 적합성 평가, AGV 운행을 위한 바닥 상태, 통로 폭, Wi-Fi 커버리지, 충전 스테이션 위치 등 인프라 요건을 검토해야 합니다. 필요한 경우 AGV 도입에 맞춰 레이아웃 재설계나 인프라 업그레이드가 선행되어야 합니다.
WMS 통합 및 IT 시스템 준비
기존 WMS와 AGV 제어 시스템 간의 원활한 통합을 위한 인터페이스 개발, 데이터 형식 정의, 통신 프로토콜 설정이 필요합니다. 실시간 재고 추적, 작업 할당, 성능 모니터링 등을 위한 시스템 간 데이터 흐름을 설계해야 합니다.
변화 관리 및 인력 준비
AGV 도입에 따른 작업자 역할 변화, 새로운 기술에 대한 교육 및 훈련, 조직 구조 조정 등 변화 관리 계획이 필요합니다. 기술 도입에 대한 우려와 저항을 해소하고, AGV와 인간 작업자의 효과적인 협업 모델을 구축해야 합니다.
물류창고 AGV의 최신 트렌드 및 미래 전망
물류창고 환경에서의 AGV 기술과 활용 방식은 계속 진화하고 있습니다. 최신 트렌드와 미래 전망을 살펴보겠습니다:
AI 기반 지능형 AGV
인공지능과 기계학습을 활용한 더 지능적인 AGV가 등장하고 있습니다. 작업 패턴 학습을 통한 물류 흐름 예측, 상품 특성 인식을 통한 최적 취급 방법 선택, 수요 변화에 따른 선제적 재배치 등 자율적 의사결정 능력이 향상되고 있습니다. 특히 피크 시즌이나 프로모션 기간의 수요 패턴을 학습하여 미리 대응하는 예측적 물류 관리가 가능해지고 있습니다.
인간-로봇 협업 강화
AGV와 인간 작업자의 장점을 결합한 협업 모델이 발전하고 있습니다. 협동 로봇 기술을 통해 AGV가 작업자에게 필요한 상품을 가져다주고, 완료된 작업을 수거하는 방식으로 작업 효율을 높입니다. 또한 증강현실(AR)을 활용한 직관적 인터페이스로 작업자와 AGV 간 소통이 더욱 자연스러워지고 있습니다.
다양한 로봇 시스템의 통합
AGV, 협동 로봇, 자동 포장 시스템, 드론 등 다양한 로봇 기술을 통합하는 종합적인 자동화 솔루션이 등장하고 있습니다. 각 로봇이 특화된 작업을 수행하면서도 서로 원활하게 협업하는 시스템을 통해 창고 운영의 전 과정을 자동화하는 방향으로 발전하고 있습니다.
유연한 확장 모델
'로봇 어스 어 서비스(RaaS, Robot as a Service)' 모델이 확산되면서 초기 투자 부담 없이 필요에 따라 AGV 시스템을 도입하고 확장할 수 있게 되었습니다. 이는 중소규모 물류업체도 첨단 자동화 기술을 활용할 수 있게 하며, 계절적 변동이 큰 업종에서 수요에 맞춰 AGV 수를 유연하게 조절할 수 있는 장점이 있습니다.
미래 물류창고 환경에서 AGV는 단순 운반 장비를 넘어 지능형 물류 생태계의 핵심 구성요소로 자리매김할 것으로 전망됩니다. 특히 5G 통신, 에지 컴퓨팅, 디지털 트윈 기술 등과 결합하여 더욱 통합적이고 예측 가능한 물류 시스템을 구현할 것으로 예상됩니다. 이러한 변화는 '다음날 배송(Next-day delivery)'을 넘어 '당일 배송(Same-day delivery)', 나아가 '몇 시간 내 배송(Hours delivery)'까지 가능하게 하는 초고속, 초효율 물류 인프라의 토대가 될 것입니다.
그러나 이러한 발전 과정에서 보안, 프라이버시, 안전 기준, 인력 재교육 등 해결해야 할 과제도 존재합니다. 특히 기술 발전에 따른 일자리 변화에 대응하여 창고 작업자들이 새로운 역할(로봇 관리, 운영 감독, 예외 처리 등)로 전환할 수 있도록 지원하는 것이 중요한 사회적 과제가 될 것입니다.
제조업 생산 라인에서의 AGV
제조업 생산 라인은 효율성, 정확성, 일관성이 핵심인 환경으로, AGV(무인운반차)는 이러한 요구사항을 충족시키는 이상적인 솔루션을 제공합니다. 전통적인 컨베이어 벨트나 인력 기반 물류 시스템과 달리, AGV는 유연성과 확장성을 갖추면서도 생산 공정의 자동화와 최적화를 가능하게 합니다. 특히 다품종 생산, 맞춤형 제조, 린 생산 방식(Lean Manufacturing)이 중요해지는 현대 제조 환경에서 AGV는 단순한 운반 장비를 넘어 스마트 제조의 핵심 구성요소로 자리잡고 있습니다.
제조 라인에서 AGV의 주요 용도
제조 환경에서 AGV가 수행하는 주요 역할과 작업은 다음과 같습니다:
자재 및 부품 공급
- 원자재 창고에서 생산 라인으로의 자재 운반
- JIT(Just-In-Time) 방식의 필요 시점에 정확한 부품 공급
- 생산 계획에 따른 선제적 자재 준비 및 배치
- 자재 사용량 모니터링 및 자동 보충
공정 간 이동
- 생산 라인의 각 공정 간 반제품 이동
- 공정별 작업 완료 신호에 따른 자동 이송
- 병렬 공정 간 균형 있는 물류 흐름 관리
- 품질 검사 결과에 따른 라우팅(양품/불량품)
완제품 처리
- 최종 조립 라인에서 포장 구역으로 완제품 운반
- 포장된 제품을 출하 구역 또는 완제품 창고로 이동
- 주문별 분류 및 배치 작업 지원
- 팔레타이징(Palletizing) 작업과의 연계
공구 및 장비 운반
- 생산 설비용 공구, 지그(jig), 금형 등의 운반
- 설비 교체나 셋업 시 필요 장비 공급
- 측정 및 검사 장비의 이동 지원
- 공구실과 생산 현장 간 물류 자동화
제조 환경에 적합한 AGV 유형
제조업의 다양한 환경과 요구사항에 맞춰 여러 유형의 AGV가 활용됩니다:
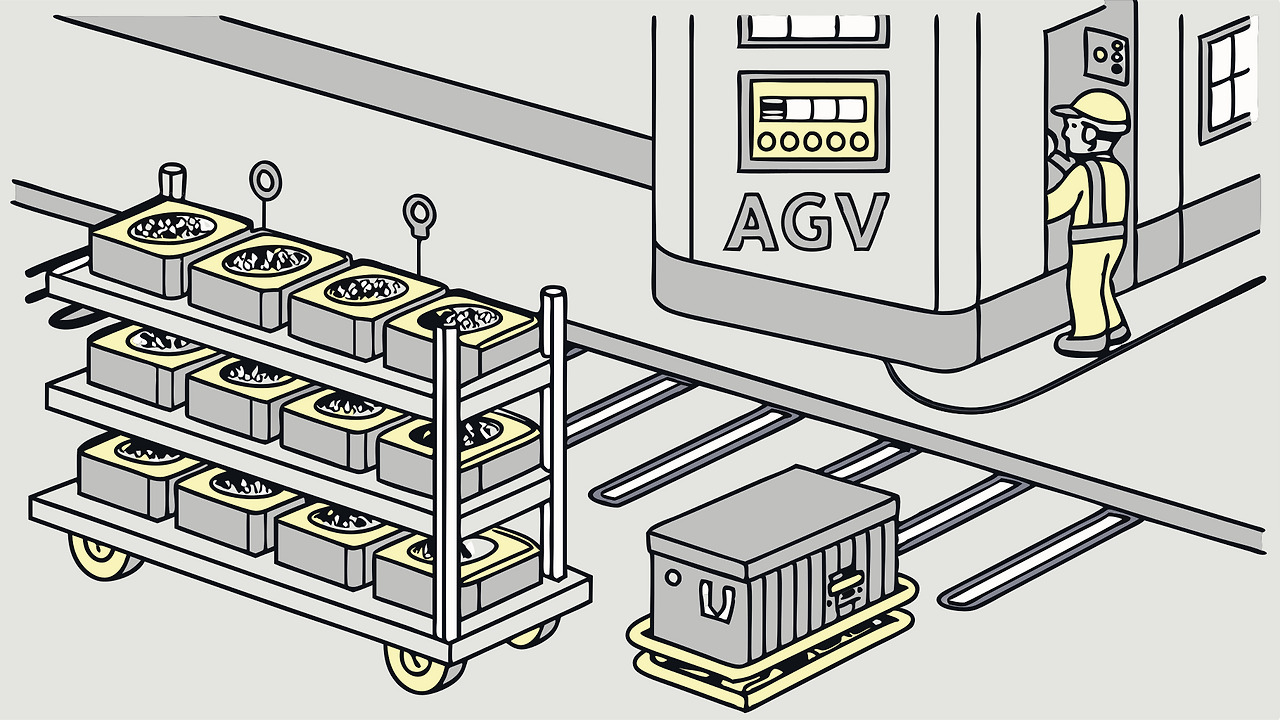
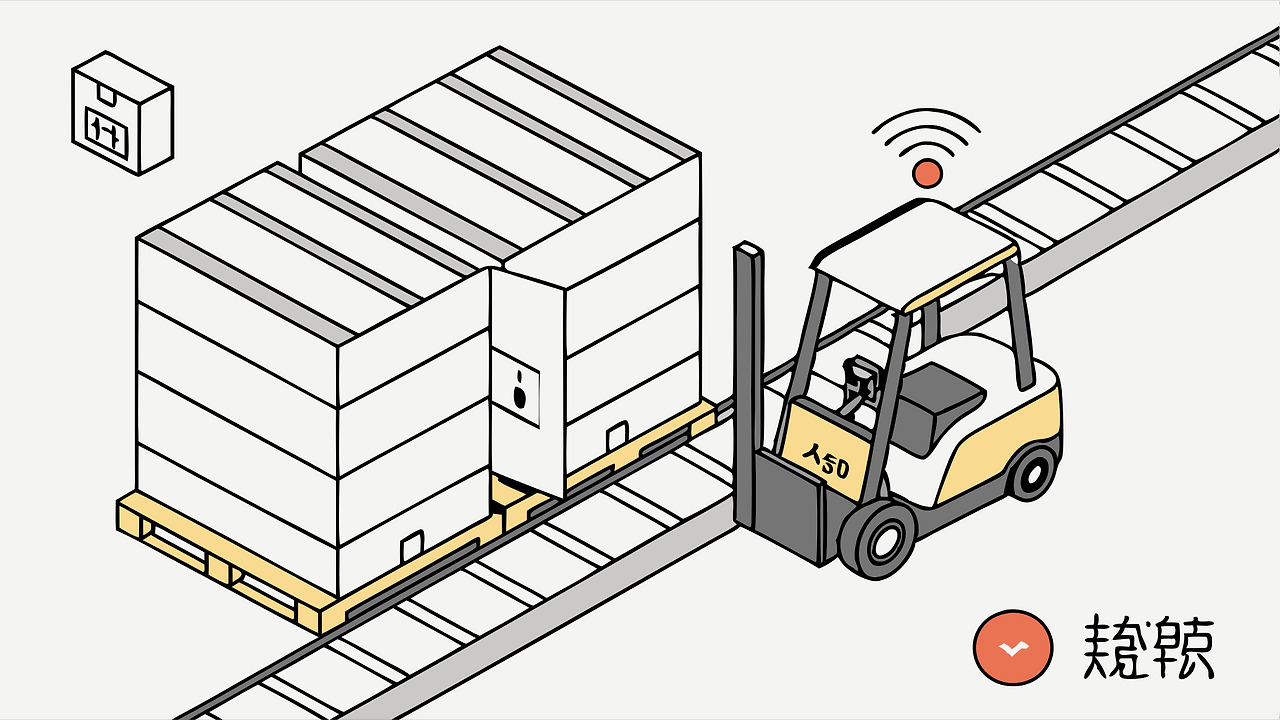
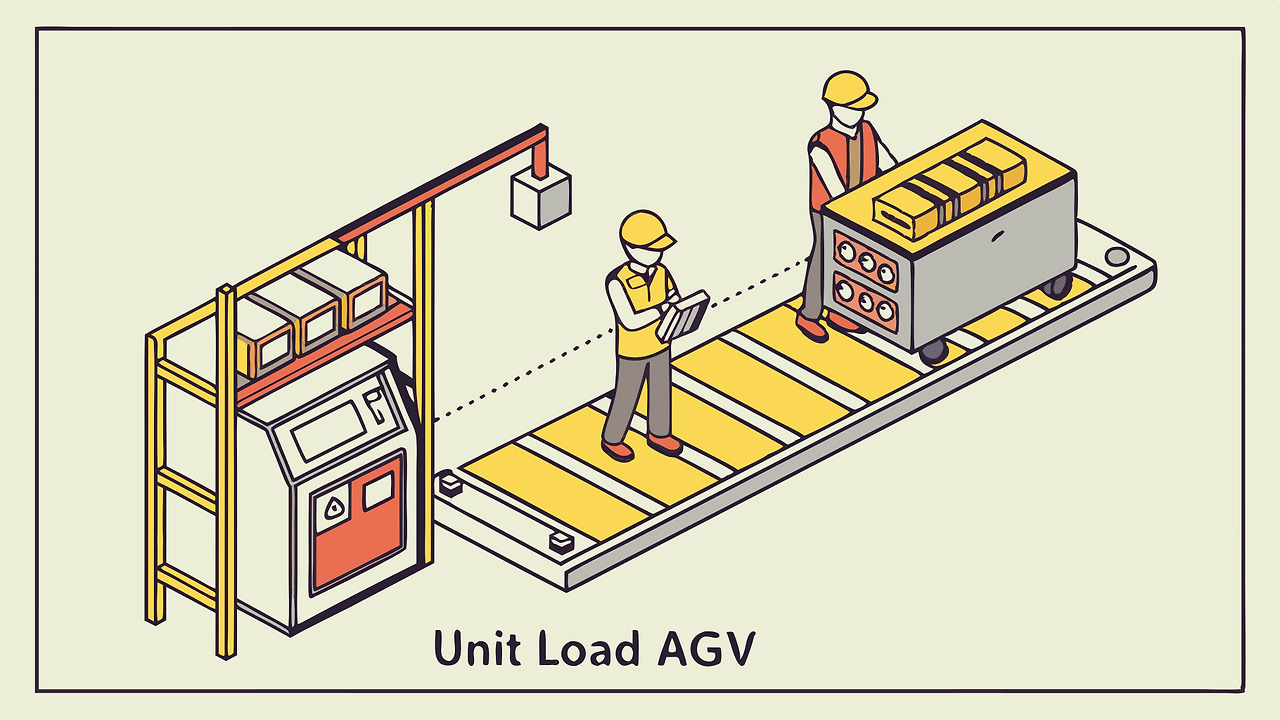

견인형 AGV(Towing AGV)
여러 카트를 연결하여 견인하는 방식으로, 한 번에 많은 양의 자재나 부품을 운반할 수 있습니다. 자동차 조립 라인이나 대형 제조 시설에서 주로 사용되며, 정해진 경로를 따라 각 작업 스테이션에 필요한 자재를 순차적으로 공급합니다. 견인력이 강하고 여러 작업장에 동시 서비스가 가능하여 효율적이지만, 넓은 회전 반경이 필요하고 경로 유연성이 제한적입니다.
지게차형 AGV(Forklift AGV)
팔레트나 대형 컨테이너를 들어 올려 운반하는 AGV로, 무거운 자재나 대형 부품의 이동에 적합합니다. 높은 적재 능력과 수직 이동 기능으로 입고 구역에서 생산 라인으로의 자재 공급, 완제품의 창고 적재 등에 활용됩니다. 특히 높은 랙(rack)이 있는 제조 환경에서 유용하지만, 정밀한 포크 조작이 필요하고 안전 관리가 중요합니다.
유닛로드 AGV(Unit Load AGV)
상단에 평평한 적재 플랫폼이 있어 표준 크기의 컨테이너나 상자를 운반하는 AGV입니다. 생산 라인의 공정 간 반제품 이동, 부품 키트 배송 등에 널리 사용되며, 일부 모델은 컨베이어 시스템과 연동되어 자동 적재/하역이 가능합니다. 중간 크기의 부하를 효율적으로 운반할 수 있고 다목적성이 높아 다양한 제조 환경에 적용 가능합니다.
소형 카트형 AGV
작은 크기의 부품, 전자 부품, 정밀 도구 등을 운반하는 소형 AGV입니다. 전자제품 제조, 정밀 기계 조립, 의료기기 생산 등 정교한 작업이 이루어지는 환경에 적합합니다. 크기가 작고 민첩하여 작업대 사이의 좁은 공간도 이동 가능하며, 작업자 근처에서 안전하게 작동할 수 있습니다. 특히 클린룸이나 정밀 제조 환경에서 활용도가 높습니다.
제조 라인 AGV의 주요 기능 및 특징
제조 환경에서 효과적으로 작동하기 위해 AGV가 갖추어야 할 핵심 기능과 특징은 다음과 같습니다:
생산 시스템 통합
- MES(제조실행시스템)와의 실시간 연동
- 생산 계획 변경에 따른 동적 작업 조정
- 설비 상태 모니터링과 연계한 물류 흐름 관리
- 품질 관리 시스템과의 연동(불량품 자동 분리)
- 생산 데이터 수집 및 분석 지원
정밀한 위치 제어
- 작업 스테이션과의 정확한 도킹(docking)
- 밀리미터 수준의 정밀한 자재 배치
- 자동화 설비와의 인터페이스를 위한 위치 정확도
- 반복적인 경로에서의 일관된 성능 유지
- 진동 최소화 및 안정적인 운반 능력
안전 기능
- 작업자 밀집 환경에서의 안전한 작동
- 다층적 안전 센서와 비상 정지 기능
- 위험 물질 취급 시 특수 안전 프로토콜
- 소음 및 충격 최소화 설계
- 안전 구역 및 속도 제한 자동 적용
환경 적응성
- 제조 환경 특성(온도, 습도, 먼지 등)에 대한 내성
- 다양한 바닥 조건에서의 안정적 주행
- 레이아웃 변경에 유연하게 대응하는 능력
- 24/7 연속 운영을 위한 내구성
- 특수 제조 환경(클린룸, 방폭 등) 대응 능력
제조업에서의 AGV 적용 사례
제조업 생산 라인에서 AGV가 성공적으로 적용된 다양한 산업별 사례를 살펴보겠습니다:
자동차 제조
대형 자동차 제조업체는 차체 조립 라인에 견인형 AGV를 도입하여 JIT 방식으로 부품을 공급합니다. 한 번에 최대 8개의 부품 카트를 견인하며 정해진 일정에 따라 조립 구역을 순회합니다. 이를 통해 부품 공급 정확도가 99.8%로 향상되었으며, 재고 보유량이 40% 감소했습니다. 또한 지게차형 AGV가 엔진, 변속기 등 무거운 부품을 정확한 타이밍에 조립 라인에 공급하며, 유닛로드 AGV는 차량별 맞춤형 부품 키트를 작업자에게 전달합니다.
전자제품 제조
대형 전자제품 제조업체는 스마트폰 조립 라인에 소형 카트형 AGV를 도입하여 정밀 부품을 운반합니다. 클린룸 환경에 맞게 설계된 이 AGV들은 정전기 방지 기능과 미세 진동 제어 시스템을 갖추고 있습니다. 각 AGV는 RFID로 부품 트레이를 식별하고, 조립 진행 상황에 맞춰 필요한 부품을 자동으로 공급합니다. 품질 검사 스테이션과 연동되어 불량 제품은 자동으로 격리 구역으로 이동시킵니다. 이 시스템 도입으로 부품 혼입 오류가 95% 감소하고, 생산 라인 전환 시간이 60% 단축되었습니다.
제약 제조
글로벌 제약 기업은 GMP(Good Manufacturing Practice) 규정을 준수하는 특수 AGV를 도입하여 원료 약품과 완제품을 운반합니다. 이 AGV는 오염 방지를 위한 HEPA 필터, 항균 재질, 자동 세척 시스템을 갖추고 있으며, 각 운반 작업의 모든 기록이 자동으로 문서화됩니다. 특히 교차 오염 방지를 위한 지능적 경로 계획과 약품별 전용 운반 컨테이너 관리 시스템이 통합되어 있습니다. 이 시스템은 배치 간 전환 시간을 70% 단축하고, 문서화 작업을 85% 자동화하여 규제 준수 비용을 크게 절감했습니다.
항공우주 제조
항공기 제조업체는 대형 부품 운반을 위한 중량물 AGV 시스템을 구축했습니다. 이 AGV는 최대 20톤의 항공기 부품을 0.5mm 이내의 정확도로 위치시킬 수 있으며, 레이저 측정 시스템과 고정밀 유압 제어를 통해 조립 지점에 정확히 도킹합니다. 또한 다수의 AGV가 동기화되어 대형 동체 섹션을 함께 운반하는 협업 모드도 지원합니다. 이 시스템은 부품 운반 시간을 80% 단축하고, 정밀 위치 조정에 필요한 인력을 60% 감소시켰으며, 작업자 안전 사고 위험을 크게 줄였습니다.
제조업 AGV 도입의 이점과 효과
제조업 생산 라인에 AGV를 도입함으로써 얻을 수 있는 주요 이점과 그 효과는 다음과 같습니다:
이러한 수치적 개선 외에도 품질 향상(표준화된 물류 프로세스), 유연성 강화(다품종 생산 대응), 생산 데이터 수집 향상(실시간 물류 추적), 작업 환경 개선(인체공학적 작업 설계 가능) 등의 정성적 이점도 있습니다. 특히 린 생산 방식(Lean Manufacturing)의 핵심 원칙인 낭비 제거, 연속 흐름 생산, 풀(Pull) 시스템 구현 등을 AGV가 효과적으로 지원합니다.
제조업 AGV 통합 전략 및 고려사항
제조 환경에 AGV를 성공적으로 통합하기 위한 전략과 주요 고려사항은 다음과 같습니다:
생산 프로세스 분석
기존 물류 흐름, 병목 구간, 사이클 타임 등을 면밀히 분석하여 AGV 도입으로 최대 효과를 얻을 수 있는 영역 식별
시스템 통합 계획
MES, ERP, 품질관리 시스템 등 기존 시스템과의 통합 방안 수립 및 데이터 흐름 설계
단계적 구현
전체 생산 라인에 도입하기 전 일부 구역에서 파일럿 프로젝트 실시 및 검증
지속적 최적화
운영 데이터 분석을 통한 경로, 일정, 작업 할당 등의 지속적 개선
세부 고려사항
- 생산 변동성 대응: 계절적 수요 변화, 신제품 출시, 모델 변경 등에 유연하게 대응할 수 있는 확장성 확보
- 설비 인터페이스: 자동화 생산 설비, 로봇, 컨베이어 등과의 물리적/전자적 인터페이스 설계
- 안전 규정 준수: 산업 안전 표준 및 규정(ISO 3691-4, ANSI/ITSDF B56.5 등) 준수 방안
- 작업자 교육: AGV와 함께 작업하는 작업자들의 새로운 역할과 필요 기술에 대한 교육 계획
- 유지보수 전략: 예방적 유지보수, 예비 부품 관리, 기술 지원 체계 구축
- ROI 평가: 직접적 비용 절감(인건비, 재고 등) 외에 품질, 안전, 유연성 향상 등 간접적 효과를 포함한 종합적 ROI 평가
제조업 AGV의 최신 트렌드 및 미래 방향
제조 환경에서의 AGV 기술과 활용은 지속적으로 진화하고 있습니다. 주요 트렌드와 미래 방향성은 다음과 같습니다:
협동 로봇과의 통합
AGV와 협동 로봇(코봇)을 결합한 모바일 매니퓰레이터 등장. AGV가 이동 기능을 담당하고 코봇이 정밀 작업 수행하는 통합 시스템을 통해 작업 범위와 유연성 확대
AI 기반 예측적 물류
인공지능과 기계학습을 활용한 생산 필요 자재 예측 및 선제적 공급. 과거 패턴, 생산 일정, 재고 상태 등을 학습하여 부품 부족 상황 사전 예방 및 생산 중단 최소화
디지털 트윈 통합
실제 생산 환경의 디지털 복제본과 AGV 시스템 연동. 가상 환경에서 물류 흐름 시뮬레이션, 최적화, 문제 예측이 가능하며 레이아웃 변경 효과를 사전 검증
5G 기반 실시간 제어
초저지연, 고신뢰성의 5G 네트워크를 통한 AGV 실시간 제어 및 동기화. 시간에 민감한 생산 공정에서 정밀한 타이밍 조절이 가능하며 다수 AGV의 밀리초(ms) 단위 협업 구현
이 외에도 에너지 효율 향상을 위한 무선 충전 및 에너지 하베스팅 기술, 인간 작업자와의 자연스러운 상호작용을 위한 증강현실(AR) 인터페이스, 그리고 블록체인 기술을 활용한 공급망 전체의 물류 추적 시스템 등이 개발되고 있습니다.
제조업 환경에서 AGV는 단순한 물류 자동화 도구를 넘어 지능형 생산 시스템의 핵심 구성요소로 발전하고 있습니다. 특히 Industry 4.0과 스마트 제조의 패러다임 속에서 AGV는 물리적 물류 이동과 디지털 정보 흐름을 연결하는 중요한 가교 역할을 수행하며, 유연하고 효율적이며 지속가능한 제조 혁신을 이끌어가고 있습니다.
미래의 제조 환경에서는 AGV, 로봇, 지능형 생산 설비, AR/VR 기술, 디지털 트윈 등이 유기적으로 통합된 완전 연결된 스마트 팩토리가 실현될 것으로 전망됩니다. 이러한 생태계 속에서 AGV는 단순히 지시에 따라 움직이는 장비가 아니라, 자율적으로 상황을 판단하고 다른 시스템과 협업하는 지능형 에이전트로 진화할 것입니다.
자동차 산업 내 AGV 활용 사례
자동차 산업은 대량 생산, 복잡한 조립 공정, 다양한 부품 취급 등의 특성으로 인해 AGV(무인운반차) 기술의 가장 활발한 적용 분야 중 하나입니다. 세계 각국의 자동차 제조사들은 생산 효율성 향상, 품질 관리 강화, 작업 환경 개선을 위해 다양한 유형의 AGV를 도입하고 있습니다. 자동차 생산의 전 과정에 걸쳐 AGV는 부품 공급, 프레스 공정, 차체 공정, 도장 공정, 조립 공정, 검사 및 출하에 이르기까지 물류 자동화의 핵심 역할을 담당하고 있습니다.
자동차 제조 공정별 AGV 활용
자동차 제조의 주요 공정별로 AGV가 어떻게 활용되는지 살펴보겠습니다:
프레스 및 차체 공정
- 대형 코일 및 금속 시트 운반용 중량물 AGV 활용
- 프레스 금형 교체 및 운반 자동화
- 스탬핑된 패널을 용접 공정으로 운반
- 완성된 차체 부품의 조립 라인 공급
- 공정 간 대형 차체 부품 정밀 운반
도장 공정
- 도장 전 차체를 전처리 공정으로 운반
- 도장 장비 및 소모품 자동 공급
- 도장된 차체의 건조로 입출고 자동화
- 특수 환경(고온, 화학물질) 대응 AGV 활용
- 완성된 도장 차체의 조립 라인 이송
최종 조립 공정
- JIT(Just-In-Time) 방식의 부품 공급
- 조립 라인을 따라 차체 운반(모듈러 조립)
- 엔진, 변속기 등 파워트레인 모듈 공급
- 차량별 맞춤형 부품 키트 배송
- 완성 차량의 검사 구역 이동
물류 및 부품 관리
- 공급업체로부터 입고된 부품 창고 이송
- 대형 부품(시트, 대시보드 등) 전용 운반
- 생산 계획에 따른 선제적 부품 준비
- 재고 수준 모니터링 및 자동 보충
- 빈 컨테이너 회수 및 재사용 관리
자동차 산업에서 활용되는 AGV 유형
자동차 산업의 다양한 요구사항을 충족시키기 위해 여러 유형의 AGV가 사용됩니다:
대형 중량물 운반용 AGV
차체, 엔진 블록, 대형 금형 등 무거운 부품을 운반하는 AGV입니다. 수 톤에서 수십 톤까지의 적재 능력을 갖추고 있으며, 정밀한 위치 제어 시스템으로 대형 부품을 정확히 배치합니다. 특히 차체 공정에서 중요한 역할을 하며, 레이저 내비게이션이나 와이어 가이드 방식을 주로 사용합니다. 일부 모델은 여러 대가 동기화되어 초대형 차체를 함께 운반하는 협업 기능을 갖추고 있습니다.
견인형 AGV
여러 개의 부품 카트를 연결하여 견인하는 방식으로, 조립 라인에 다양한 부품을 동시에 공급하는 데 활용됩니다. 기차와 같은 형태로 조립 라인을 따라 이동하며 각 작업 스테이션에 필요한 부품을 순차적으로 공급합니다. 특히 '자동차 키트 시스템'에서 차량별 맞춤형 부품 세트를 배송하는 데 효과적이며, 생산 라인의 모델 변경에도 유연하게 대응할 수 있습니다.
지게차형 AGV
팔레트에 적재된 부품이나 자재를 운반하는 AGV로, 입고 구역에서 생산 라인으로의 자재 이동에 주로 사용됩니다. 창고 랙에서 부품을 픽업하여 생산 라인 근처의 스테이징 구역으로 이동시키는 작업을 자동화합니다. 특히 시트, 휠, 배터리 등 부피가 크거나 무거운 부품의 운반에 효과적이며, 일부 모델은 자동 적재/하역 기능을 갖추고 있습니다.
조립 라인 전용 AGV
자동차 조립 공정에 최적화된 특수 AGV로, 차체를 들어 올려 조립 라인을 따라 이동시키는 역할을 합니다. 전통적인 컨베이어 벨트 대신 사용되며, 각 작업 스테이션에서 최적의 작업 높이로 차체를 조정할 수 있습니다. 이를 통해 작업자의 인체공학적 작업 환경을 제공하고, 차종 변경 시 유연하게 대응할 수 있는 장점이 있습니다. 또한 차량별 작업 시간에 맞춰 속도를 자동 조절하는 기능을 갖추고 있습니다.
글로벌 자동차 제조사의 AGV 도입 사례
세계 주요 자동차 제조사들의 AGV 도입 사례와 그 성과를 살펴보겠습니다:
메르세데스-벤츠 '공장 56'
메르세데스-벤츠는 독일 징델핑겐의 최첨단 '공장 56'에 완전 유연한 조립 라인 시스템인 'TecLine'을 구축했습니다. 이 시스템은 400여 대의 자율주행 AGV를 활용하여 전통적인 컨베이어 벨트를 대체했습니다. 각 AGV는 차체를 정확한 높이로 조절하며 조립 라인을 따라 이동하고, 작업자에게 최적의 작업 환경을 제공합니다. 차종별 작업 시간에 따라 자동으로 속도를 조절하며, 다양한 모델(전기차, 하이브리드, 내연기관차)을 동일 라인에서 유연하게 생산할 수 있습니다. 이 시스템을 통해 생산 유연성이 50% 향상되었고, 모델 전환 시간이 75% 단축되었습니다.
BMW 라이프치히 공장
BMW는 독일 라이프치히 공장에 'Smart Transport Robot'이라는 자율주행 AGV 시스템을 도입했습니다. 이 AGV는 레이저 SLAM 기술을 활용하여 별도의 물리적 가이드 없이 공장 내부를 자유롭게 이동합니다. 특히 부품 물류에 중점을 두어, RFID로 식별된 부품 컨테이너를 정확한 시점에 조립 라인으로 운반합니다. 또한 인공지능 기반 예측 알고리즘을 통해 생산 계획과 부품 수요를 분석하여 선제적으로 부품을 준비합니다. 이 시스템은 물류 오류를 92% 감소시켰고, 부품 대기 시간을 30% 단축했으며, 창고 공간 활용률을 40% 향상시켰습니다.
토요타 '로지스틱스 4.0'
토요타는 일본 다카하마 공장에 '로지스틱스 4.0' 이니셔티브의 일환으로 종합적인 AGV 솔루션을 구축했습니다. 이 시스템은 토요타 생산 방식(TPS)의 원칙에 따라 '풀(Pull)' 방식으로 작동하며, 각 공정의 실제 소비 속도에 맞춰 부품을 공급합니다. 특히 견인형 AGV와 지게차형 AGV가 통합된 하이브리드 시스템을 구현하여 효율성을 극대화했습니다. 또한 스마트 랙 시스템과 연동하여 부품 보관 위치를 동적으로 최적화합니다. 이 시스템은 재고 수준을 45% 감소시켰고, 부품 조달 리드타임을 60% 단축했으며, 에너지 소비를 25% 절감했습니다.
테슬라 '알리언'
테슬라는 미국 프리몬트 공장과 중국 상하이 공장에 자체 개발한 AGV 시스템 '알리언(Alien)'을 도입했습니다. 이 시스템은 차체 운반용 대형 AGV와 부품 운반용 소형 AGV로 구성되며, 기존 자동차 공장의 컨베이어 중심 설계를 완전히 재구성했습니다. 특히 AI 기반 작업 할당과 경로 최적화를 통해 생산 병목 현상을 실시간으로 파악하고 해소합니다. 또한 배터리 팩, 모터 등 전기차 특유의 대형 부품 운반에 최적화된 특수 AGV도 활용합니다. 이 시스템은 공장 면적 활용률을 30% 향상시켰고, 생산 라인 재구성 시간을 90% 단축했으며, 생산 유연성을 대폭 강화했습니다.
자동차 산업 AGV 활용의 주요 이점
자동차 제조 환경에서 AGV 도입을 통해 얻을 수 있는 핵심적인 이점은 다음과 같습니다:
생산 유연성 향상
- 다양한 차종의 혼류 생산(Mixed Model Production) 지원
- 생산 볼륨 변화에 따른 유연한 확장/축소 가능
- 신차 도입 시 생산 라인 재구성 시간 단축
- 계절적 수요 변동에 효과적 대응
- 모델별 생산 비율 변경에 신속 적응
품질 향상 및 오류 감소
- 부품 공급 정확도 증가로 조립 오류 감소
- 차량별 맞춤형 부품 키트 제공으로 혼입 방지
- 정밀한 위치 제어로 조립 품질 향상
- 물리적 충격 최소화로 부품 손상 방지
- 디지털 추적을 통한 품질 이슈 신속 파악
린 생산 원칙 구현
- JIT 부품 공급으로 재고 최소화
- 부가가치 없는 이동 및 대기 시간 제거
- 공간 활용 최적화(좁은 통로, 수직 공간 활용)
- 과잉 생산 방지 및 흐름 생산 촉진
- 지속적 개선(카이젠)을 위한 데이터 수집
작업 환경 및 안전성 개선
- 무거운 부품 운반으로 인한 작업자 부상 감소
- 인체공학적 작업 높이 자동 조정
- 위험 구역(프레스, 도장 등)에서의 자동화
- 반복적이고 단조로운 이동 작업 대체
- 작업장 소음 및 공기질 개선
자동차 산업 AGV 구현 시 도전 과제 및 해결 방안
자동차 산업에 AGV를 도입할 때 직면하게 되는 주요 도전 과제와 해결 방안은 다음과 같습니다:
도전 과제 | 원인 및 영향 | 해결 방안 |
생산 중단 없는 구현 | 24시간 가동되는 자동차 공장에서 생산 중단은 막대한 손실 초래 | 단계적 구현 전략, 주말/휴일 활용 설치, 하이브리드 운영 기간 설정 |
다양한 부품 처리 | 자동차 한 대당 2만여 개 부품의 다양한 크기, 무게, 형태 | 부품 특성별 맞춤형 AGV 구성, 표준화된 운반 컨테이너 설계 |
기존 시스템 통합 | ERP, MES, 공급망 관리 등 복잡한 레거시 시스템과의 연동 | 표준 인터페이스 개발, 중간 연결 계층 구축, 단계적 통합 접근 |
높은 신뢰성 요구 | AGV 고장이 전체 생산 라인 중단으로 이어질 위험 | 중복 시스템 구축, 예측적 유지보수, 빠른 대체 전략 수립 |
작업자 수용성 | 자동화에 대한 불안과 저항, 새로운 작업 방식 적응 문제 | 포괄적 교육 프로그램, 점진적 도입, 작업자 참여 설계 |
자동차 산업 AGV의 최신 트렌드 및 미래 전망
자동차 제조 분야에서의 AGV 기술과 활용은 다음과 같은 방향으로 발전하고 있습니다:
로봇 통합 AGV 시스템
AGV와 로봇팔을 통합한 모바일 로봇 시스템이 등장하고 있습니다. AGV가 필요한 위치로 이동한 후 로봇팔이 부품 조립, 용접, 검사 등의 작업을 수행하는 방식입니다. 이를 통해 고정식 로봇의 한계를 극복하고 생산 라인의 유연성을 극대화할 수 있습니다. 특히 소량 다품종 생산 환경에서 효과적이며, 생산 계획 변경에 따라 로봇의 위치와 작업을 동적으로 재구성할 수 있습니다.
디지털 트윈 기반 최적화
자동차 공장의 모든 AGV, 생산 설비, 작업자, 부품의 디지털 복제본을 만들어 실시간으로 동기화하는 디지털 트윈 기술이 확산되고 있습니다. 이를 통해 가상 환경에서 다양한 생산 시나리오와 레이아웃을 시뮬레이션하고, AGV 경로 및 작업 할당을 최적화할 수 있습니다. 또한 생산 중단 없이 새로운 AGV 시스템을 테스트하고 통합할 수 있는 환경을 제공합니다.
군집 지능형 AGV
자연계의 집단 행동에서 영감을 받은 군집 지능(Swarm Intelligence) 알고리즘을 적용한 AGV 시스템이 개발되고 있습니다. 중앙 제어 없이도 다수의 AGV가 자율적으로 협업하여 복잡한 물류 작업을 수행하는 방식입니다. 이를 통해 시스템 확장성이 향상되고, 개별 AGV의 고장이 전체 시스템에 미치는 영향이 최소화됩니다. 특히 대규모 공장에서 수백 대의 AGV를 효율적으로 조율하는 데 효과적입니다.
이 외에도 탄소 중립 및 지속가능성을 위한 친환경 AGV(수소 연료전지, 태양광 충전 등), 증강현실(AR)을 활용한 AGV-작업자 협업 인터페이스, 그리고 예측적 물류를 위한 AI 기반 수요 예측 시스템 등이 발전하고 있습니다.
자동차 산업의 미래 전망으로는 전기차와 자율주행차 생산 증가에 따른 새로운 AGV 요구사항 등장, 모듈식 생산 방식 확대에 따른 AGV 역할 확대, 그리고 글로벌 공급망 최적화를 위한 공장 간 AGV 시스템 표준화 등이 예상됩니다. 특히 자동차 산업의 생산 패러다임이 대량 생산에서 대량 맞춤화(Mass Customization)로 전환됨에 따라, AGV의 유연성과 지능화는 더욱 중요한 경쟁 요소가 될 것입니다.
종합하면, 자동차 산업에서 AGV는 단순한 운반 장비를 넘어 지능형 생산 시스템의 핵심 요소로 자리매김하고 있으며, 미래 자동차 제조의 패러다임 변화를 이끄는 핵심 동력이 될 것입니다. 기술 발전과 함께 AGV 시스템의 지능화, 유연화, 통합화가 지속적으로 진행되면서, 자동차 제조의 효율성, 품질, 지속가능성을 새로운 차원으로 끌어올릴 것으로 전망됩니다.
반도체·전자 산업의 AGV 적용
반도체·전자 산업은 정밀도, 청정도, 효율성이 핵심인 제조 환경으로, AGV(무인운반차)는 이러한 엄격한 요구사항을 충족시키는 이상적인 물류 솔루션입니다. 반도체 웨이퍼 처리부터 정밀 전자부품 조립, 디스플레이 패널 제조에 이르기까지 다양한 전자 제조 공정에서 AGV는 오염 최소화, 제품 손상 방지, 추적성 보장 등 핵심적인 역할을 수행합니다. 특히 클린룸 환경에서의 물류 자동화와 정밀 운반이 가능한 특수 AGV의 도입으로 반도체·전자 산업의 생산성과 품질이 크게 향상되고 있습니다.
반도체·전자 산업 AGV 적용의 특수성
반도체·전자 산업 환경에서 AGV 적용이 갖는 고유한 특성과 요구사항은 다음과 같습니다:
클린룸 환경 적합성
반도체 제조는 클래스 1~10 수준의 초청정 환경에서 이루어지며, AGV는 이러한 환경을 오염시키지 않아야 합니다. 입자 발생을 최소화하는 특수 재질과 설계, HEPA 필터 내장, 정전기 방지 처리, 무진 타이어 등이 적용됩니다. 또한 모든 구성품은 클린룸 인증을 받아야 하며, 정기적인 클린룸 호환성 검사가 필요합니다.
정밀 운반 요구사항
반도체 웨이퍼, 마스크, LCD 패널 등은 충격에 매우 취약하며 미세한 진동에도 손상될 수 있습니다. AGV는 부드러운 가감속 제어, 진동 흡수 시스템, 정밀한 위치 제어(±0.5mm 수준)를 갖추어야 합니다. 또한 웨이퍼 카세트나 FOSB(Front Opening Shipping Box)와 같은 특수 운반 용기와의 정확한 인터페이스가 필요합니다.
철저한 추적성과 통제
반도체 제조는 수백 단계의 공정을 거치며, 각 단계별 제품 이동과 상태를 완벽하게 추적해야 합니다. AGV는 RFID, 바코드 등을 통해 운반 중인 제품을 식별하고, MES(제조실행시스템)와 실시간 연동하여 이동 이력, 대기 시간, 환경 조건 등을 기록합니다. 특히 로트 혼입 방지와 공정 간 교차 오염 방지를 위한 엄격한 프로토콜이 적용됩니다.
고가 제품과 높은 신뢰성
반도체 웨이퍼 한 장의 가치는 수만 달러에 이를 수 있으며, AGV 고장으로 인한 제품 손상이나 생산 지연은 막대한 손실을 초래합니다. 따라서 AGV 시스템은 99.9% 이상의 가용성과 무오류 운영을 보장해야 합니다. 중복 설계, 실시간 상태 모니터링, 예측적 유지보수, 신속한 오류 복구 메커니즘 등이 필수적으로 구현됩니다.
반도체·전자 산업에서 활용되는 AGV 유형
반도체·전자 제조 환경의 특수 요구사항을 충족시키기 위한 다양한 AGV 유형이 있습니다:
웨이퍼 운반용 AGV
반도체 웨이퍼와 포토마스크를 운반하기 위한 특수 AGV로, 보통 25장 또는 50장의 웨이퍼를 담은 FOUP(Front Opening Unified Pod) 또는 FOSB를 정밀하게 운반합니다. 클린룸 등급에 적합한 재질과 설계를 갖추고 있으며, 정전기 방지(ESD) 기능과 정밀한 진동 제어 시스템이 특징입니다. 일부 모델은 로드포트(Load Port)와 직접 연결되어 자동 도킹 및 웨이퍼 로딩이 가능합니다. 레이저 내비게이션이나 자기 유도 방식을 주로 사용하며, 최대 3개의 FOUP을 동시에 운반할 수 있는 모델도 있습니다.
OHT(Overhead Hoist Transport)
천장에 설치된 레일을 따라 이동하면서 웨이퍼 컨테이너를 운반하는 시스템입니다. 엄밀히 말하면 AGV는 아니지만, 반도체 팹(FAB)에서 AGV와 함께 또는 대체 솔루션으로 널리 사용됩니다. 바닥 공간을 차지하지 않아 클린룸 면적을 효율적으로 활용할 수 있고, 작업자 이동과 간섭이 없는 장점이 있습니다. 최신 모델은 AI 기반 경로 최적화와 예측적 유지보수 기능을 갖추고 있으며, 일부 시스템은 바닥 AGV와 OHT 간의 통합 운영을 지원합니다.
LCD/OLED 패널 운반용 AGV
대형 디스플레이 패널과 글래스 기판을 운반하기 위한 특수 AGV입니다. 대형 평판 유리의 안전한 운반을 위해 충격 흡수 시스템과 정밀한 수평 유지 기능을 갖추고 있으며, 클린룸 환경에 적합한 설계로 입자 발생을 최소화합니다. 일부 모델은 대형 글래스(2.5m × 2.5m 이상)를 수직으로 운반하기 위한 특수 고정 장치와 진동 제어 시스템을 갖추고 있습니다. 특히 8세대 이상 대형 디스플레이 제조 라인에서 중요한 역할을 수행합니다.
PCB 조립 라인용 AGV
인쇄회로기판(PCB) 제조 및 조립 공정에 최적화된 AGV입니다. SMT(Surface Mount Technology) 라인의 각 공정 간 PCB 운반, 테스트 스테이션으로의 이동, 포장 구역으로의 운반 등을 자동화합니다. 정전기 방지 기능과 온습도 모니터링 시스템을 갖추고 있으며, 일부 모델은 SMT 장비와 직접 연동되어 자동 적재/하역이 가능합니다. 특히 다품종 소량 생산 환경에서 라인 전환 유연성을 제공하며, MES와의 연동을 통해 PCB 이력 추적을 지원합니다.
반도체·전자 산업의 주요 AGV 적용 영역
반도체·전자 제조의 각 영역에서 AGV가 어떻게 활용되는지 살펴보겠습니다:
반도체 전공정(Front-end)
- 웨이퍼 팹 내 공정 장비 간 웨이퍼 운반
- 웨이퍼 보관소(stocker)와 공정 장비 간 이동
- 포토마스크 및 레티클(reticle) 운반
- 웨이퍼 검사 및 측정 장비로의 샘플 이동
- 클린룸 구역 간 웨이퍼 운반
반도체 후공정(Back-end)
- 테스트 장비로의 칩 운반
- 패키징 라인 공정 간 제품 이동
- 본딩, 몰딩, 마킹 등 장비 간 운반
- 최종 검사 및 포장 구역으로 이동
- 자재 창고와 생산 라인 간 물류
디스플레이 제조
- 글래스 기판 운반 및 적재
- 코팅, 노광, 에칭 등 공정 간 이동
- 대형 패널 조립 라인 물류
- 검사 및 수리 구역으로의 운반
- 포장 및 출하 구역으로 완제품 이동
전자제품 조립
- SMT 라인 공정 간 PCB 운반
- 부품 공급 및 키트 제공
- 테스트 스테이션으로의 제품 이동
- 완제품 포장 및 팔레타이징
- 자재 창고 관리 및 공급
글로벌 반도체·전자 기업의 AGV 도입 사례
세계 주요 반도체·전자 기업들의 AGV 도입 사례와 성과를 살펴보겠습니다:
TSMC의 '300mm 자동화 팹'
세계 최대 파운드리 업체인 TSMC는 12인치(300mm) 웨이퍼 생산 라인에 완전 자동화된 물류 시스템을 구축했습니다. 바닥 AGV와 천장 OHT 시스템이 통합된 이 시스템은 AI 기반 작업 할당 알고리즘을 통해 각 운송 작업의 최적 운반 수단을 자동으로 결정합니다. 특히 공정 장비 별 대기 시간을 고려한 지능형 웨이퍼 공급 기능을 통해 장비 가동률을 극대화합니다. 이 시스템 도입으로 웨이퍼 사이클 타임이 30% 단축되었고, 인적 오류로 인한 웨이퍼 손상이 95% 감소했으며, 클린룸 활용 효율이 25% 향상되었습니다.
삼성전자의 '스마트 팹'
삼성전자는 평택과 화성의 반도체 공장에 AI 기반 '스마트 팹' 시스템을 구축했습니다. 이 시스템은 웨이퍼 운반을 위한 특수 AGV 300여 대와 OHT 시스템을 통합 운영하며, 실시간 생산 상황에 따라 우선순위와 경로를 동적으로 최적화합니다. 특히 머신러닝을 활용한 예측적 운반 기능이 특징으로, 공정 완료 전에 미리 AGV를 배치하여 대기 시간을 최소화합니다. 또한 AGV의 모든 운행 데이터는 빅데이터 분석을 통해 물류 흐름 최적화와 장비 배치 개선에 활용됩니다. 이러한 시스템을 통해 웨이퍼 운반 시간이 40% 단축되었고, 전체 생산 효율성이 20% 향상되었습니다.
LG디스플레이의 '스마트 글래스 물류'
LG디스플레이는 파주 OLED 공장에 대형 글래스 기판 운반을 위한 특수 AGV 시스템을 도입했습니다. 이 시스템은 8.5세대 이상 대형 글래스(2200mm × 2500mm)를 안전하게 운반할 수 있는 진동 제어 기술과 정밀 위치 제어 시스템을 갖추고 있습니다. 특히 글래스 기판의 휨 현상을 방지하기 위한 능동형 수평 유지 시스템과 충격 흡수 메커니즘이 특징입니다. 또한 RFID 기반 추적 시스템을 통해 각 글래스 기판의 이동 경로와 상태를 실시간으로 모니터링합니다. 이 시스템 도입으로 글래스 파손률이 80% 감소했고, 생산 라인 전환 시간이 65% 단축되었으며, 클린룸 면적 활용률이 30% 향상되었습니다.
반도체·전자 산업 AGV 도입의 핵심 이점
반도체·전자 제조 환경에 AGV를 도입함으로써 얻을 수 있는 주요 이점은 다음과 같습니다:
품질 향상
인적 오류 제거, 오염 최소화, 일관된 취급으로 인한 제품 손상 감소, 특히 수율 향상에 직접 기여
생산성 증대
지속적인 자재 흐름, 장비 대기 시간 감소, 24/7 운영, 공정 간 사이클 타임 단축으로 전체 생산성 향상
추적성 확보
제품 이동의 완벽한 디지털 기록, 로트 추적, 공정 이력 관리, 규제 준수 용이성 제공
유연성 강화
다품종 생산 대응, 빠른 라인 전환, 생산량 변동에 유연한 대응, 공장 레이아웃 최적화 용이
이 외에도 클린룸 공간 활용 최적화, 작업자 안전성 향상(유해 물질 취급 최소화), 통합 데이터 수집을 통한 공정 개선, 그리고 규제 준수 및 문서화 자동화 등의 이점이 있습니다. 특히 반도체 산업의 미세 공정화와 대형 웨이퍼 전환에 따른 정밀도 요구 증가는 인간 작업자보다 일관된 성능을 제공하는 AGV의 가치를 더욱 높이고 있습니다.
반도체·전자 산업 AGV 구현 시 고려사항
반도체·전자 제조 환경에 AGV를 성공적으로 도입하기 위한 주요 고려사항은 다음과 같습니다:
철저한 리스크 평가
고가 제품과 민감한 환경을 고려한 철저한 FMEA(고장 모드 및 영향 분석), 다중 안전 시스템 구축, 오작동 시나리오 대비 계획 수립
통합 계획 수립
MES, ERP, 장비 제어 시스템 등 기존 IT 인프라와의 긴밀한 통합 설계, 데이터 흐름 및 인터페이스 정의, 표준 프로토콜 채택
생산 연속성 보장
24/7 가동 환경에서 생산 중단 없는 구현 전략, 단계적 도입, 백업 시스템 구축, 신속한 전환 메커니즘 설계
검증 및 인증
클린룸 규격 인증, 정전기 방지 검증, 정밀도 테스트, 내구성 검증 등 반도체 환경에 필요한 엄격한 품질 관리 및 인증 절차 수행
반도체·전자 산업 AGV의 최신 트렌드 및 미래 전망
반도체·전자 제조 분야에서의 AGV 기술과 활용은 다음과 같은 방향으로 발전하고 있습니다:
AI 기반 예측적 물류
인공지능을 활용한 공정 완료 시점 예측 및 선제적 AGV 배치가 확산되고 있습니다. 장비 상태, 공정 특성, 과거 패턴 등을 학습하여 웨이퍼나 패널이 다음 공정으로 이동해야 할 정확한 시점을 예측하고, 미리 AGV를 배치하여 대기 시간을 최소화합니다. 특히 복잡한 반도체 공정에서 공정 장비의 가동률을 극대화하고 전체 사이클 타임을 단축하는 데 큰 기여를 합니다.
3D 통합 물류 시스템
바닥 AGV, 천장 OHT, 수직 리프트 등을 통합한 3차원 물류 시스템이 발전하고 있습니다. 클린룸의 제한된 공간을 최대한 활용하기 위해 수직 방향의 이동을 포함한 종합적인 물류 최적화가 이루어지고 있으며, 각 운반 수단의 장점을 결합한 하이브리드 시스템이 확산되고 있습니다. 특히 대형 반도체 팹에서 여러 층의 클린룸을 효율적으로 연결하는 통합 물류 시스템이 중요해지고 있습니다.
엣지 컴퓨팅 기반 자율 의사결정
AGV에 강력한 엣지 컴퓨팅 능력을 탑재하여 중앙 제어 없이도 자율적 의사결정이 가능한 시스템이 등장하고 있습니다. 네트워크 지연이나 중앙 서버 장애에도 영향 받지 않고 실시간 상황에 신속하게 대응할 수 있으며, 다른 AGV와의 직접 통신을 통한 분산형 협업도 가능합니다. 특히 반도체 공정의 예민한 타이밍 요구사항을 충족시키기 위한 실시간 의사결정 능력이 중요해지고 있습니다.
초청정 및 오염 모니터링 기술
반도체 공정의 미세화에 따라 더욱 엄격한 청정도 요구사항을 충족시키기 위한 기술이 발전하고 있습니다. 자체 정화 기능, 입자 발생 실시간 모니터링, 정전기 차단 기술 등이 적용된 AGV가 등장하고 있으며, 일부 모델은 클린룸 내 오염원을 감지하고 매핑하는 기능도 갖추고 있습니다. 특히 3nm 이하 공정에 대응하기 위한 초청정 AGV 기술이 중요한 연구 분야로 부상하고 있습니다.
반도체·전자 산업의 미래 전망으로는 초대형 웨이퍼(450mm) 도입에 따른 새로운 AGV 요구사항 등장, 반도체 공급망 다변화에 따른 글로벌 표준화된 AGV 시스템 필요성 증가, 그리고 특히 친환경 반도체 제조를 위한 에너지 효율적 AGV 시스템 개발 등이 예상됩니다.
또한 반도체 설계-제조의 디지털 트윈 개념이 확대되면서, 가상 환경과 실제 AGV 시스템이 실시간으로 동기화되는 스마트 팹 구현이 가속화될 것으로 전망됩니다. 이를 통해 공정 변화, 생산량 조정, 신제품 도입 등의 시나리오를 사전 시뮬레이션하고 최적화할 수 있어, 반도체 산업의 민첩성과 경쟁력 강화에 기여할 것입니다.
종합하면, 반도체·전자 산업에서 AGV는 단순한 물류 자동화 수단을 넘어 스마트 제조의 핵심 인프라로 자리매김하고 있으며, 공정의 미세화와 복잡화, 생산 규모의 확대, 품질 요구사항의 강화에 따라 그 중요성은 더욱 커질 것으로 예상됩니다.
'자동차 전문 채널 > 자동차 부품업계 관련 업무 지식' 카테고리의 다른 글
자동차용 외장부품에 적용하는 PMMA(아크릴) 소재 개요 (5) | 2025.05.11 |
---|---|
현대기아자동차 개발프로세스와 FULL TOOL 조건의 이해 및 세부 준비사항 (0) | 2025.05.08 |
전통 부품업체의 전기차 전환 성공 사례 (0) | 2025.04.25 |
전기차 충전 인프라 부품 시장 성장성 (1) | 2025.04.25 |
디지털 전환을 위한 회사조직 변화 관리 (1) | 2025.04.25 |
차량 경량화를 위한 소재 개발 동향 (0) | 2025.04.25 |